Basic principles of engine thrust plates
The basic principles of engine thrust plates revolve around their role in ensuring the smooth and efficient operation of the engine. Here are the key principles:
- Transmission of Thrust: Engine thrust plates are designed to transmit the thrust or force generated by the piston to the crankshaft. As the piston moves up and down within the cylinder bore, the thrust plate transfers this force to the crankshaft, which converts linear motion into rotational motion.
- Reducing Friction: Thrust plates incorporate bearing surfaces that minimize friction between the piston and the crankshaft. By providing smooth and low-friction contact surfaces, the thrust plates help reduce wear and ensure efficient power transfer.
- Axial Load Balancing: Thrust plates also play a crucial role in balancing the axial load within the engine. They help counteract the thrust forces generated by the reciprocating motion of the pistons, preventing excessive wear on the engine components and maintaining the structural integrity of the engine.
- Lubrication: Proper lubrication is essential to minimize friction and ensure the longevity of the thrust plates. Engine oil is circulated to lubricate the bearing surfaces of the thrust plates, reducing heat and frictional wear.
- Material Strength and Durability: Thrust plates are typically made from high-strength materials, such as steel or cast iron, to withstand the high-pressure and high-temperature conditions within the engine. The materials used should have high wear resistance and durability to withstand the repetitive loading cycles.
Overall, the basic principles of engine thrust plates revolve around facilitating the smooth transfer of thrust forces, minimizing friction, balancing axial loads, ensuring proper lubrication, and providing strength and durability to withstand engine operating conditions. These principles contribute to the overall performance and reliability of the engine.
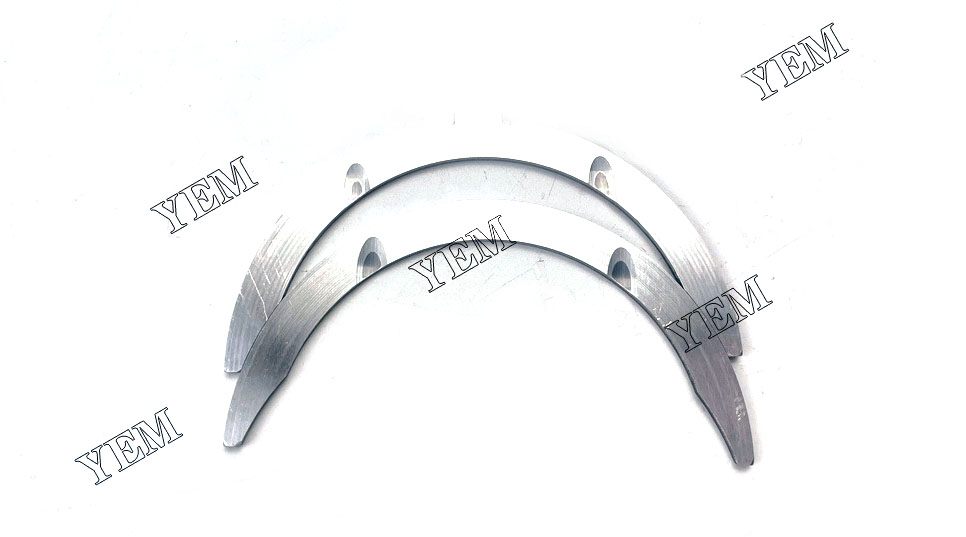
Structure and working mechanism of engine thrust plate
The structure and working mechanism of an engine thrust plate can vary depending on the type of engine, but I will provide a general overview:
Structure:
An engine thrust plate is typically a flat or curved plate-like component located at the bottom of the engine cylinder block or on the side of the engine block. It is usually made of a durable material, such as steel or cast iron, to withstand the forces and high temperatures generated by the engine.
Working Mechanism:
The working mechanism of an engine thrust plate involves several components and interactions. Here are the key elements:
- Piston: Within the engine cylinder, the piston moves up and down in response to combustion forces. The piston is connected to the connecting rod, which is further connected to the crankshaft.
- Cylinder Bore: The piston moves within the cylinder bore, creating pressure forces during the combustion process.
- Thrust Bearing: The thrust plate incorporates a thrust bearing, which is a low friction bearing surface. The thrust bearing helps to transmit the axial thrust forces generated by the piston to the crankshaft.
- Lubrication: Proper lubrication is crucial for the smooth operation of the thrust plate. Engine oil is circulated throughout the engine to lubricate the bearing surfaces, including the thrust plate. The lubricant reduces friction and heat, preventing excessive wear and ensuring optimal performance.
Working Process:
When the engine is running, the combustion process generates forces that push the piston downward. These forces create axial thrust, trying to push the piston along the axis of the cylinder bore. The thrust plate is designed to counteract this axial thrust force and transmit it to the crankshaft.
As the piston moves downward, the axial thrust force is transferred through the piston skirt, which presses against the thrust bearing surface on the thrust plate. The thrust bearing helps to distribute the force evenly and reduces friction between the piston and the thrust plate.
From the thrust plate, the axial thrust force is transmitted to the crankshaft, where it is converted into rotary motion. The thrust plate helps balance and distribute this force, preventing excessive wear on the engine components and maintaining the stability and integrity of the entire engine system.
In summary, the structure and working mechanism of an engine thrust plate involve the integration of a thrust bearing, proper lubrication, and the transfer of axial thrust forces from the piston to the crankshaft. This mechanism ensures smooth operation, reduces friction, and contributes to the overall performance and longevity of the engine.
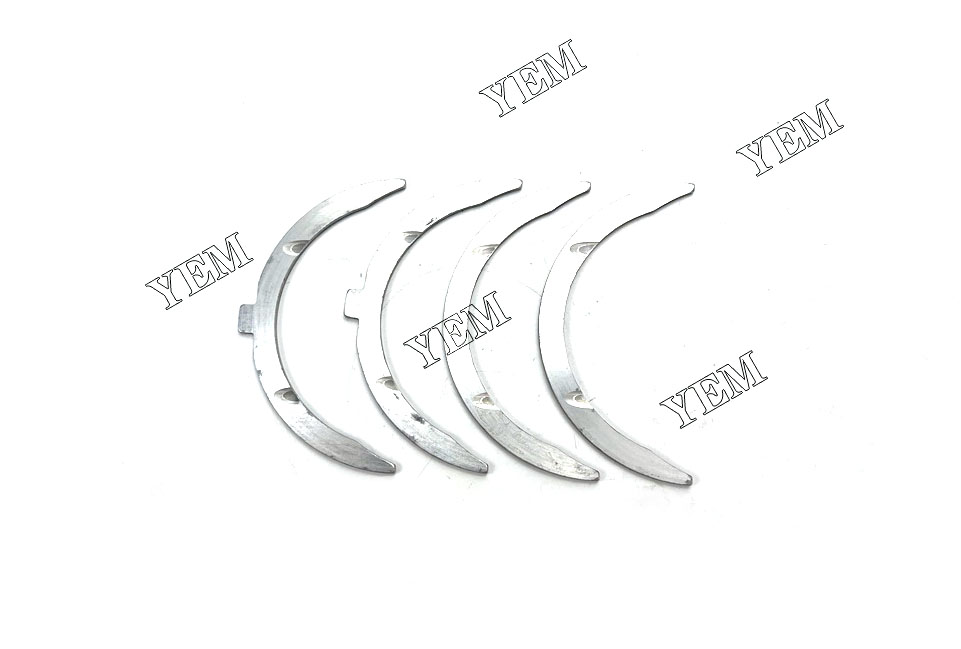
Materials and manufacturing processes of engine thrust plates
Engine thrust plates are typically made from high-strength materials that can withstand the forces generated by engine thrust. These materials include steel, titanium, and even composites. The manufacturing process for these plates typically involves precision machining and forming to ensure accuracy and durability.
For steel thrust plates, the raw material is first shaped into a rough plate through either casting or rolling. The plate is then machined to its final dimensions and surface finish. Titanium thrust plates are typically formed using a combination of forging and machining processes to achieve the desired shape and strength. Composite thrust plates are made through a layering process where fibers such as carbon or fiberglass are layered and bound together with a resin. The resulting composite material is then machined to form the final thrust plate.
Regardless of the material used, manufacturing processes for engine thrust plates typically involve strict quality control measures to ensure the plate meets the precise requirements of the engine it is being used in.
Engine Thrust Plate Failures and Frequently Asked Questions
Here are some frequently asked questions and answers about engine thrust plate failures:
Q: What causes engine thrust plate failures?
A: There are several factors that can contribute to engine thrust plate failures, including improper installation, manufacturing defects, excessive wear, and high operating temperatures.
Q: How can I tell if my engine thrust plate is failing?
A: Signs of a failing engine thrust plate can include unusual vibrations or noises, loss of engine power, decreased fuel efficiency, and poor overall performance.
Q: Can I drive with a failing engine thrust plate?
A: It is not recommended to drive with a failing engine thrust plate, as it can lead to further engine damage and potentially dangerous situations.
Q: How can I prevent engine thrust plate failures?
A: Regular engine maintenance and inspections are crucial for preventing thrust plate failures. It is also important to use high-quality materials and proper installation techniques.
Q: Can I repair a failed engine thrust plate?
A: In some cases, a failed engine thrust plate can be repaired, but it is often more cost-effective to replace the plate with a new one.
Q: How often should I replace my engine thrust plate?
A: The lifespan of an engine thrust plate can vary based on usage and other factors. It is recommended to replace the thrust plate as part of regular engine maintenance or if signs of wear and damage are detected.
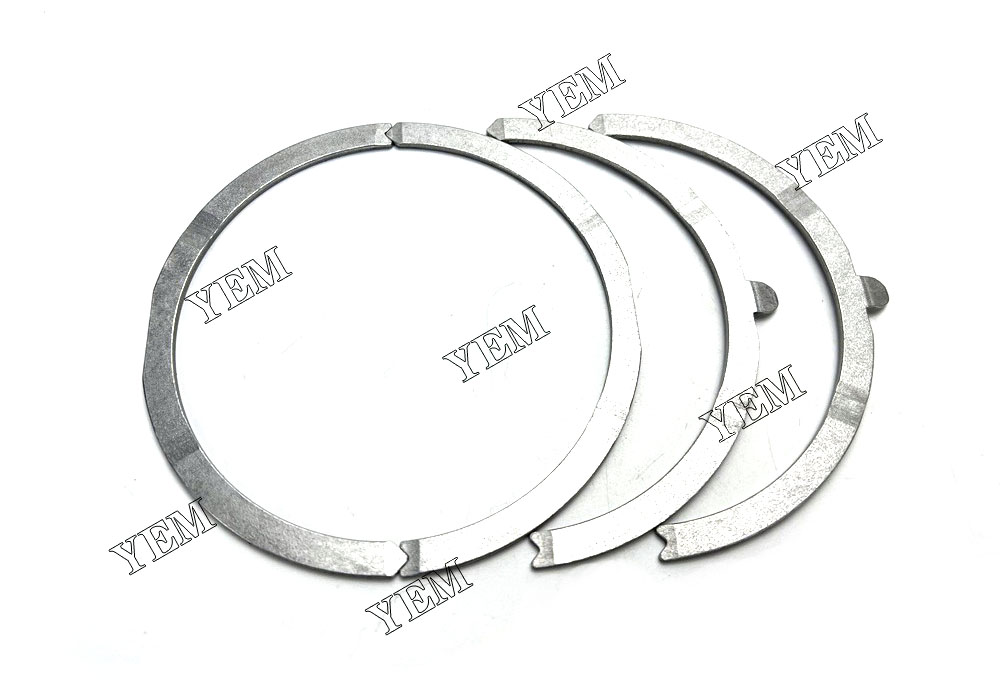
The improvement and technological development of engine thrust plates have focused on enhancing their durability, efficiency, and overall performance. Here are some notable advancements:
- Material selection: Manufacturers have been exploring the use of advanced materials with high strength-to-weight ratios, such as composite materials and alloys, to improve the strength and longevity of thrust plates. These materials offer better resistance to wear, heat, and corrosion.
- Surface coatings: Applying specialized coatings to the thrust plate’s surface can enhance its performance and reduce friction. Coatings like diamond-like carbon (DLC) and thermal barrier coatings (TBC) provide increased hardness, reduced friction, and improved heat resistance.
- Advanced manufacturing techniques: Precision machining methods, such as computer numerical control (CNC) machining, have enabled the production of thrust plates with higher accuracy and tighter tolerances. This ensures optimal fit and alignment with other engine components.
- Computational fluid dynamics (CFD) analysis: CFD simulations help engineers analyze the fluid flow around thrust plates, optimizing their design for improved performance and efficiency. CFD analysis aids in identifying potential weak spots or areas prone to high stress, allowing for targeted design improvements.
- Integrated sensor technology: Integrating sensors into thrust plates allows for real-time monitoring of various parameters, such as temperature, pressure, and vibrations. This data can help detect potential failures or anomalies, enabling proactive maintenance and preventing catastrophic damage.
- Advanced testing methods: Non-destructive testing techniques, such as ultrasound, X-ray, and thermography, are now being employed to inspect thrust plates for hidden defects, cracks, or material degradation. This ensures the quality and reliability of the thrust plates before installation.
Overall, these advancements contribute to more robust and efficient engine thrust plates, reducing the likelihood of failures and enhancing the overall performance and longevity of engines.
Application cases of engine thrust plates
Engine thrust plates are commonly used in different types of engines, including aircraft, military vehicles, and heavy machinery. Here are a few application cases:
- Aero-engines: Aero-engines require high-power output to propel aircraft, generating substantial thrust forces. Thrust plates are used to support the axial forces produced by the engine during operation. In addition, thrust plates facilitate the transfer of engine power to the aircraft, reducing vibration, enhancing fuel efficiency, and improving engine reliability.
- Gas turbines: Gas turbines are widely used in the energy industry to generate electricity. Thrust plates are utilized in gas turbines to support the thrust loads generated by the blades, ensuring that the rotor remains stable during high-power operation. By distributing the load across the thrust plate, the pressure on individual components is reduced, leading to lower wear and tear and a longer lifespan for the engine.
- Marine diesel engines: Marine diesel engines are used to power ships and boats. Thrust plates are commonly used in marine diesel engines to support propeller thrust and balance the load on the transmission and engine components. They also help dampen vibration and ensure smooth operation of the engine.
- Heavy machinery: Heavy machinery, such as excavators, bulldozers, and cranes, also rely on powerful engines to operate. Thrust plates are used in these machines to support the axial forces generated by the engine and ensure that the components are working efficiently and safely. Additionally, thrust plates can enhance the longevity of moving parts and reduce wear and tear on the entire system.
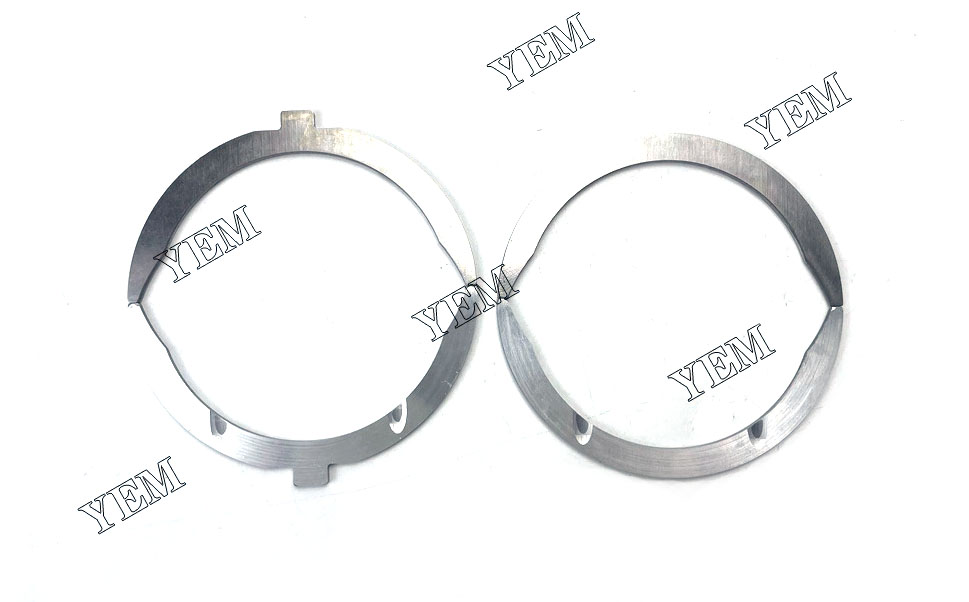
Overall, the application of thrust plates plays an essential role in many engine-related applications by improving the efficiency, stability, and safety of different engines.
Contact us
YEM Excavator Parts Co., Ltd. is a company specializing in the research, development, production and sales of excavator parts. We are committed to providing high-quality, high-performance excavator accessories solutions to global customers.
As a professional company, we have an experienced and skilled R&D team, capable of continuous research and innovation, and design and develop excavator accessories products that meet market demand. We pay attention to product quality control, adopt advanced production technology and equipment to ensure that each product can meet international standards and pass strict quality inspections.
Our product range covers all kinds of excavator accessories, including hydraulic cylinders, oil seals, filters, cabs, etc. These accessories have been carefully selected and designed to ensure compatibility with a wide range of excavators and to maintain outstanding performance and reliability in harsh operating environments.
We not only provide existing excavator accessories, but also customize design and production according to customer needs. Whether it is standard parts or non-standard parts, we can precisely manufacture and provide high-quality solutions according to the requirements provided by customers.
Our company not only pays attention to product quality, but also attaches great importance to customer service. We have a professional customer service team that can answer customer inquiries and solve customer problems in a timely manner. We also provide installation, maintenance and after-sales service of accessories to ensure that customers can get all-round support and assistance.