The role and importance of main bearings
The main bearing plays a key role in the engine and is of great importance. The following are several aspects of the role and importance of main bearings:
- Carrying engine load: The main bearing bears the huge load generated by the rotating parts of the engine (such as the crankshaft). They support and bear the weight and torque of the engine and help maintain the stability of rotating components.
- Reduce friction and wear: The main bearing reduces friction and wear between the rotating parts inside the engine by providing a lubricating oil film. They ensure smooth movement of the engine’s rotating parts at high speeds and reduce energy losses.
- Controls the alignment of rotating parts: Main bearings help control the alignment of rotating parts of the engine. They ensure that rotating parts such as the crankshaft maintain the correct position and alignment at high speeds, thus avoiding vibration and imbalance in the engine.
- Provide structural support: The main bearing not only carries the engine load, but also provides structural support. They help keep the engine’s internal components stable and ensure the engine maintains its structural integrity during operation.
- Affects engine performance and reliability: The state of the main bearing directly affects the performance and reliability of the engine. Good main bearings can reduce energy loss, provide smooth power output, and extend the service life of the engine.
All in all, main bearings are a critical component of an engine. They not only support and carry the load of the engine, they also reduce friction and wear, control the alignment of rotating parts, and provide structural support. They play a vital role in engine performance and reliability.
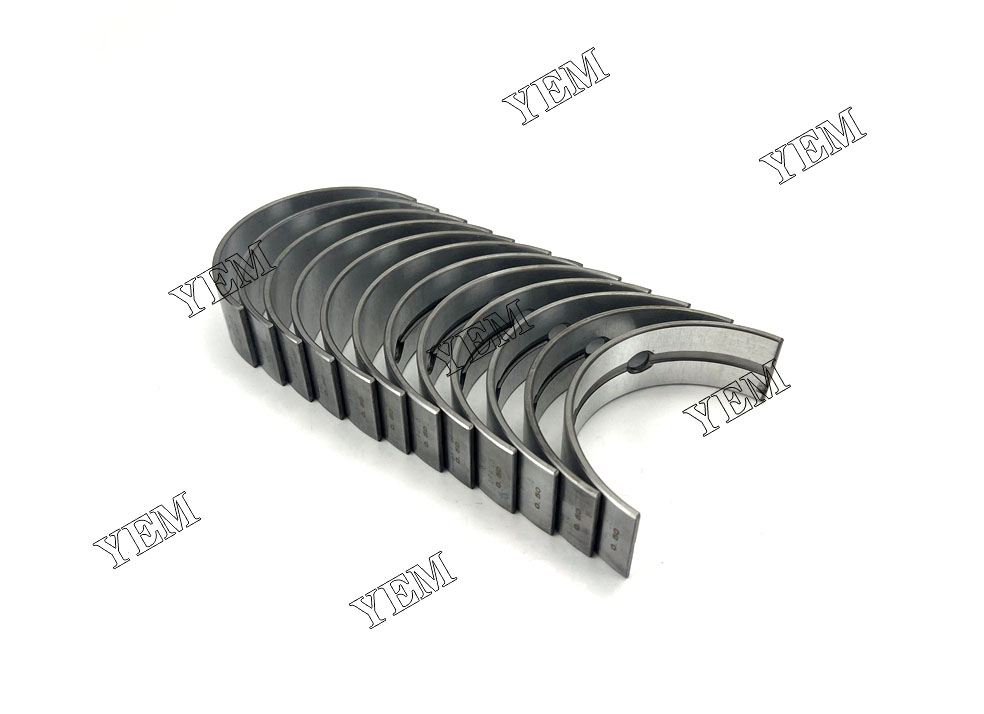
Main bearing construction and types
Main bearings are an essential component in engines, providing support for the crankshaft and helping to reduce friction and wear. They come in different construction designs and types, including:
- Journal Bearings: Also known as plain or sleeve bearings, journal bearings consist of an inner race (journal) that rotates within an outer race (bearing shell). The space between the journal and bearing shell is filled with oil for lubrication. Journal bearings are commonly used in engines due to their simplicity and cost-effectiveness.
- Thrust Bearings: Thrust bearings are used to control axial (thrust) loads, which occur when the engine’s rotational forces apply pressure in the direction parallel to the crankshaft’s axis. They are typically positioned at the ends of the crankshaft and help maintain its proper axial alignment.
- Split Bearings: Split bearings, as the name suggests, are designed in two or more separate pieces. They allow for easier installation and replacement without the need to disassemble the entire engine. Split bearings are especially useful in situations where accessibility is limited.
- Bi-Metal Bearings: Bi-metal bearings are constructed with two layers—a soft metal layer (such as aluminum or copper alloy) on the inside and a stronger metal layer (such as steel) on the outside. The soft metal layer provides good conformability and embeddability, while the outer layer provides strength and support.
- Tri-Metal Bearings: Tri-metal bearings are similar to bi-metal bearings but consist of three layers. The intermediate layer, situated between the soft metal and outer shell, is typically made of a copper-lead alloy. Tri-metal bearings offer enhanced load-carrying capacity and durability.
- Coated Bearings: Coated bearings feature a special coating applied to the bearing surface. These coatings can provide improved wear resistance, reduced friction, and enhanced seizure resistance. Common coating materials include polymer-based materials, such as PTFE (polytetrafluoroethylene), and metallic layers like silver.
It’s important to note that the specific construction and types of main bearings used can vary depending on the engine design, application, and manufacturer preferences. Different engines may require different types of main bearings to meet specific performance and durability requirements.
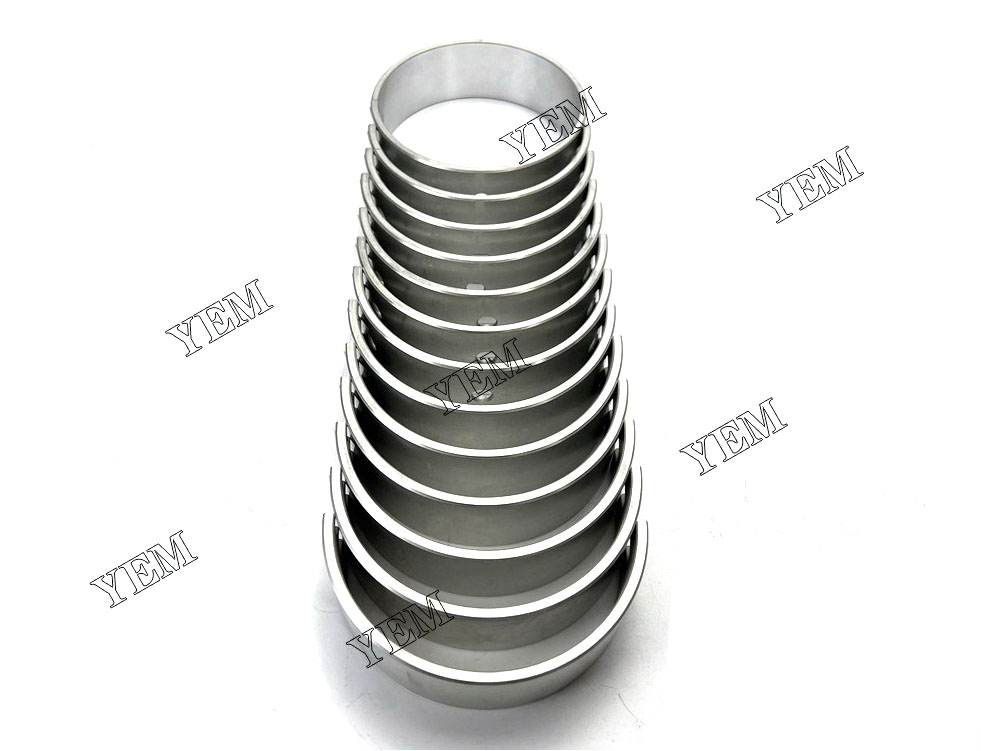
Main bearing material selection and manufacturing process
The selection of main bearing materials is crucial to ensuring proper engine performance and durability. Factors that need to be considered when selecting a bearing material include load-carrying capacity, wear resistance, conformability, embeddability, and corrosion resistance.
Common materials used for main bearings include:
- Babbitt: A soft and malleable tin-based alloy that offers good load-carrying capacity and conformability. However, it can be prone to wear and corrosion.
- Copper-lead: A durable and corrosion-resistant material that provides good wear resistance and embeddability. However, it may have lower conformability than Babbitt.
- Aluminum: A lightweight material that offers good wear resistance and load-carrying capacity. However, it may be more prone to corrosion and seizure.
- Steel-backed: Combines a steel backing with a softer overlay material (such as Babbitt or copper-lead) for enhanced durability and load-carrying capacity.
The manufacturing process for main bearings can vary depending on the material and bearing type. In general, the manufacturing process involves the following steps:
- Melting and casting the bearing material into the desired shape and size.
- Machining the bearing to the correct dimensional tolerances.
- Applying any necessary surface coatings or treatments (such as plating or lubricant impregnation).
- Quality control testing to ensure the bearing meets industry standards and specifications.
- Packaging and delivery of the bearings to the engine manufacturers or assembly plants.
Manufacturing processes for different types of main bearings and materials may involve additional steps or variations in the above process. It is important to note that proper quality control and testing is essential to ensure the reliability and performance of main bearings.
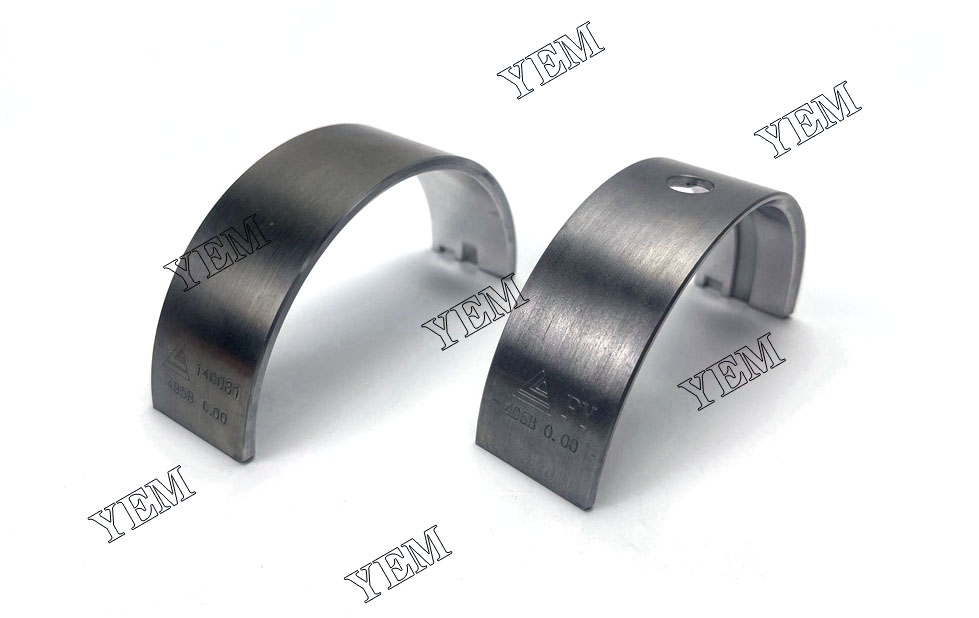
Main bearing faults and fault diagnosis
Main bearings are critical components in engines, and faults can lead to serious engine damage and failure if not addressed promptly. Common main bearing faults include:
- Worn bearings: Over time, the constant friction and load on the bearings can cause them to wear down. Worn bearings may exhibit symptoms such as increased engine noise, low oil pressure, and excessive bearing clearance. Visual inspection or measuring the bearing clearance can help diagnose this fault.
- Bearing seizure: Bearing seizure occurs when the bearing seizes onto the crankshaft journal due to insufficient lubrication or excessive heat. This can lead to a loss of oil supply to other engine components and cause catastrophic engine failure. Signs of bearing seizure include overheating, knocking or rattling noises, and loss of power. Disassembling the engine and inspecting the bearings can confirm this fault.
- Bearing fatigue: Main bearings can develop fatigue due to high loads, improper installation, or inadequate lubrication. Fatigue cracks can lead to bearing failure and generate metal debris in the oil system. Symptoms may include engine vibration, increased bearing clearance, and visible signs of wear or damage. Visual inspection and microscopic examination of the bearing surface can help diagnose fatigue-related issues.
- Bearing misalignment: Incorrect bearing installation or misaligned crankshaft can cause uneven loading and operating stresses on the main bearings. This can result in premature wear, excessive heat generation, and increased bearing clearance. Diagnosing misalignment may involve measurement of bearing clearances and assessing the alignment of the crankshaft.
Fault diagnosis for main bearings can involve several methods:
- Visual inspection: Examining the bearings for signs of wear, damage, or discoloration can provide initial clues about potential faults.
- Measurement and testing: Using tools such as a bore gauge or micrometer to measure bearing clearances can indicate abnormal wear or misalignment. Oil pressure testing can help assess the lubrication system and identify potential issues.
- Oil analysis: Regular oil analysis can detect the presence of metal particles or abnormal wear debris in the lubricant, indicating a potential bearing fault.
- Vibration analysis: Monitoring engine vibrations can provide insights into bearing condition. Unusual vibrations can signal bearing misalignment, fatigue, or other faults.
If main bearing faults are suspected, it is recommended to consult with a qualified mechanic or engine specialist to perform a thorough diagnosis and determine the appropriate course of action for repair or replacement.
Main bearing maintenance and care
Main bearings are a critical component of an internal combustion engine and require proper maintenance and care to ensure their longevity. Here are some tips for maintaining and caring for main bearings:
- Regular oil changes: The engine oil lubricates the main bearings and helps to prevent wear and tear. It’s important to follow the manufacturer’s recommendations for oil changes to keep the engine operating at peak performance.
- Monitor oil pressure: Low oil pressure can indicate a problem with the main bearings. Always keep an eye on the oil pressure gauge and immediately address any issues or concerns.
- Avoid harsh driving conditions: Hard acceleration, abrupt stops and starts, and heavy loads can stress the main bearings and lead to premature wear. It’s important to drive the vehicle in a manner that doesn’t place unnecessary stress on the engine.
- Check for signs of wear: Regular inspections of the main bearings can help catch any problems early on. Look for signs of wear, such as metal shavings in the oil or inexplicable engine noises.
- Proper installation: Main bearings should always be installed according to manufacturer specifications. Failure to do so can lead to premature wear and tear.
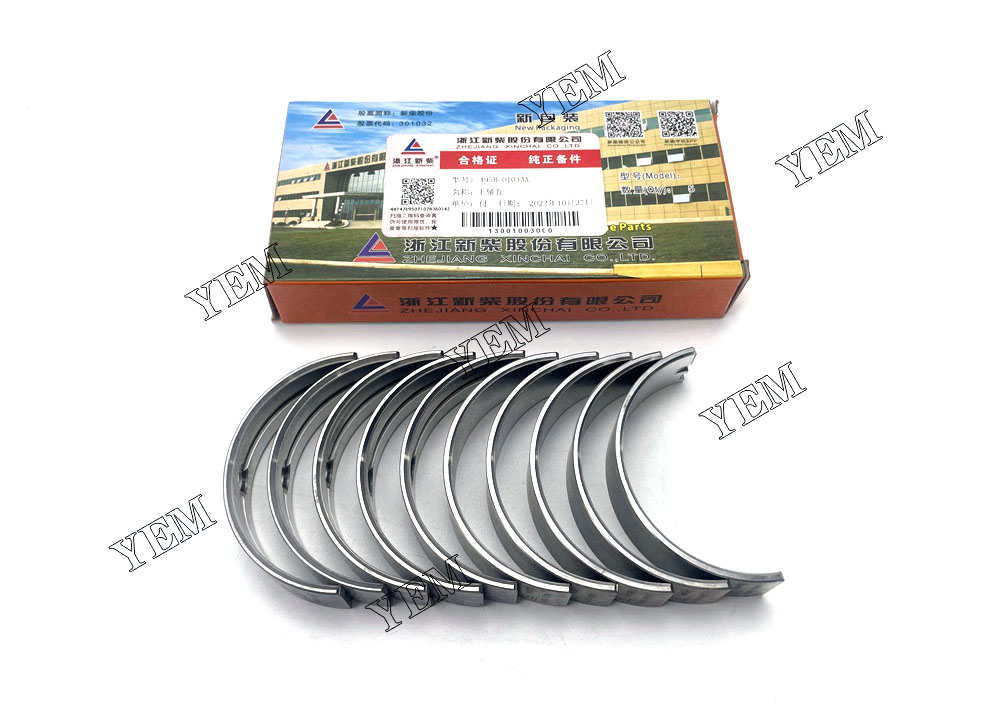
By following these tips, you can keep your main bearings in good condition and ensure a long-lasting engine.
Main bearing improvements and innovations
Over the years, there have been several improvements and innovations in main bearing design and technology. These advancements aim to enhance performance, durability, and overall lifespan. Here are some notable improvements:
- Material advancements: Main bearings are commonly made from various materials, including steel, aluminum alloy, or bimetallic compositions. Advancements in metallurgy have led to the development of high-strength materials with improved resistance to wear, heat, and corrosion. These materials help prolong the life of the bearing and increase its load-bearing capacity.
- Coatings and surface treatments: Various coatings and surface treatments have been introduced to improve the performance of main bearings. These treatments can enhance the bearing’s resistance to wear, reduce friction, and promote better oil retention. Examples include polymer coatings, diamond-like carbon (DLC) coatings, and micro-textured surfaces.
- Lubrication systems: Lubrication is crucial for main bearing performance. Advanced lubrication systems, such as variable oil pressure systems or active oil control systems, have been developed to optimize the distribution of oil to the main bearings. These systems ensure proper lubrication under various operating conditions, reducing friction and wear.
- Engine management systems: Modern engine management systems play a significant role in main bearing performance. These systems monitor various parameters, including oil pressure, temperature, and engine speed, to optimize engine operation. They can adjust oil flow, activate warning indicators, and aid in the prevention of catastrophic bearing failures.
- Computational design and simulation: Computational modeling and simulation techniques have improved the design and development process of main bearings. These tools allow engineers to assess bearing performance under different operating conditions, leading to optimized designs with better load distribution and reduced friction.
These improvements and innovations have collectively contributed to the overall reliability, performance, and longevity of main bearings in internal combustion engines. Continuous research and development in this field continue to bring about further advancements in main bearing technology.
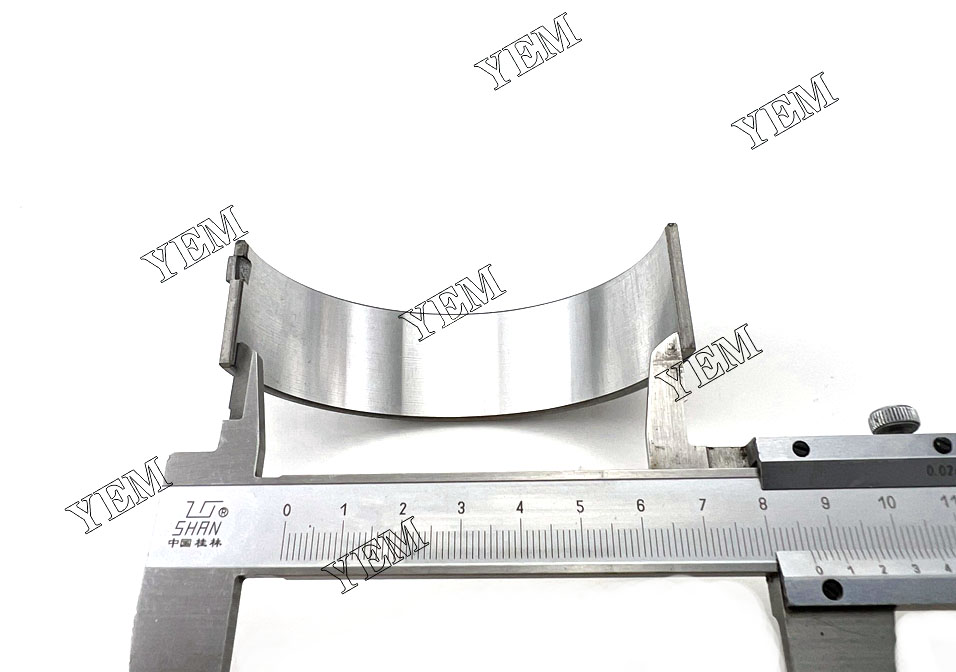
Main bearing application cases and industry trends
Main bearings are widely used in various industries and applications where rotating machinery is involved. Here are some prominent application cases and industry trends:
- Automotive Industry: Main bearings are extensively used in automobile engines, where they support and facilitate the smooth rotation of the crankshaft. With trends towards more efficient engines, main bearings are being designed to handle higher loads, reduce friction, and improve overall engine performance.
- Aerospace Industry: Main bearings play a crucial role in aircraft engines, where they ensure the smooth and reliable operation of the crankshaft. In the aerospace industry, trends focus on lightweight materials, improved lubrication systems, and advanced coatings to enhance fuel efficiency, reduce maintenance requirements, and meet stringent safety and reliability standards.
- Power Generation: Main bearings are utilized in various power generation applications, such as gas turbines, steam turbines, and hydroelectric generators. The industry trend is towards larger and more efficient power generation systems. This drives the need for main bearings capable of handling higher loads, operating at high temperatures, and providing extended service life.
- Industrial Machinery: Main bearings find applications in a wide range of industrial machinery, including pumps, compressors, fans, and gearboxes. The industry trend is towards more compact and energy-efficient machinery. Main bearings need to be designed to accommodate higher speeds, heavier loads, and offer improved reliability and maintenance intervals.
- Wind Turbines: Main bearings are critical components in wind turbines, as they support the massive rotor blades and ensure their rotational movement. Industry trends in wind energy focus on larger turbines with increased power output. This requires main bearings capable of withstanding higher loads, longer service life, and improved reliability in harsh environmental conditions.
- Marine Industry: Main bearings are essential in marine applications, including ship propulsion systems and marine engines. Industry trends in the marine sector involve the development of more environmentally friendly propulsion systems, such as electric or hybrid systems. Main bearings need to be designed to support these new propulsion technologies while ensuring high efficiency and reliability.
- Bearing Maintenance and Monitoring: Industry trends emphasize the importance of proactive bearing maintenance and monitoring techniques. Predictive maintenance strategies, such as condition monitoring and remote monitoring, are increasingly adopted to detect potential issues and optimize maintenance schedules. This trend aims to minimize unplanned downtime, reduce maintenance costs, and extend bearing lifespan.
As industries evolve and technology advances, main bearings continue to face challenges related to higher loads, increased efficiency requirements, and better performance. Industry trends strive to address these challenges by focusing on material advancements, lubrication systems, design optimization, and advanced monitoring techniques to ensure safer, more reliable, and more efficient machinery operation.
Contact us
Our YEM team is composed of a group of experienced, enthusiastic and professional excavator parts engineers and technicians. We are committed to providing customers with high-quality excavator accessories and related solutions to meet customer needs.
Our team has many years of industry experience and is familiar with all types and brands of excavators. We have an in-depth understanding of the working principle of excavators and the functions of accessories, and can provide customers with accurate and professional suggestions. We cooperate with many well-known excavator parts manufacturers and suppliers to ensure that the products we provide to our customers are of high quality and reliability.
Whether it is necessary to replace a damaged excavator accessory or to upgrade the function and performance of the excavator, our team can provide customers with a comprehensive solution. We can provide the most suitable accessory options according to the needs and budget of customers, and ensure the smooth progress of installation and maintenance work.
Our services are not limited to providing excavator accessories, but also include transportation, installation, repair and after-sales support of accessories. We always take customer satisfaction as our primary goal and strive to provide customers with excellent service and the best solutions.
Thank you for your interest in Yem excavator parts team, if you have any needs or questions, please feel free to contact us. We look forward to working with you to provide you with high-quality excavator accessories and professional technical support.