The working principle and structure of the oil transfer pump
The working principle of the oil transfer pump is to use mechanical or electric power to suck and discharge liquid (such as oil, fuel, etc.) through the inner cavity of the pump. Its basic structure includes the following parts:
- Pump body: The pump body is the main part of the oil transfer pump, usually made of cast iron, steel and other materials. It includes the inlet and outlet ports, and the inlet and outlet pipes connected to the pump chamber.
- Impeller: The impeller is a rotating part in the oil pump, which generates centrifugal force through its own rotation, sucks the liquid from the inlet and discharges it to the outlet. The impeller is usually made of metal and can be open or closed, and the direction of rotation can be clockwise or counterclockwise depending on the application.
- Pump cavity: The pump cavity is the space where the impeller rotates, and the liquid in the pump cavity is compressed and discharged by the centrifugal force of the impeller. The pump chamber is usually lined with an abrasion resistant material for durability and corrosion resistance.
- Seals: Oil transfer pumps usually require seals to prevent fluid leakage. Common sealing methods include packing seals and mechanical seals. The packing seal forms a seal by filling soft materials (such as PTFE, soft DuPont, etc.), while the mechanical seal achieves the seal through the contact between the seal ring and the rotating part.
- Driving device: The driving device can be an electric motor, engine or other power source, which transmits power to the impeller of the oil transfer pump through a transmission device (such as a belt, chain, etc.), making it rotate and driving the flow of liquid.
The above is the basic working principle and structure of the oil pump. Different types of oil transfer pumps may have some special structures and working principles, but in general, they all rely on the rotation of the impeller to generate centrifugal force to suck and discharge liquid.
Classification and types of oil transfer pumps
Oil pumps can be classified according to different classification standards, the following are the common classifications and types:
- According to the working principle:
- Centrifugal pumps: use centrifugal force to draw liquid from the center and expel it from the edges.
- Positive Displacement Pump: A fixed volume is formed by vanes, gears or plungers, so that the liquid is pushed from the suction port to the discharge port.
- Vortex pump: liquid is sucked in from the center and discharged from the edge by the principle of vortex flow.
- Axial piston pump: the plunger reciprocates in the axial direction to realize the suction and discharge of liquid.
- According to the structural form:
- Single stage pump: a simple pump consisting of one impeller.
- Multistage pumps: Compound pumps consisting of several impellers.
- Submersible pumps: installed in liquids, driven directly by electric motors.
- According to the purpose and characteristics:
- Petroleum pump: used for the transportation of liquids such as petroleum and fuel.
- Chemical pump: suitable for chemical industry, can transport various corrosive and flammable liquids.
- Slurry pump: used to transport high-concentration liquid containing solid particles, such as slag, coal cinder, etc.
- Sewage pump: used to treat waste water such as sewage and sludge.
- Dense delivery pump: suitable for slurry and high-concentration liquid delivery.
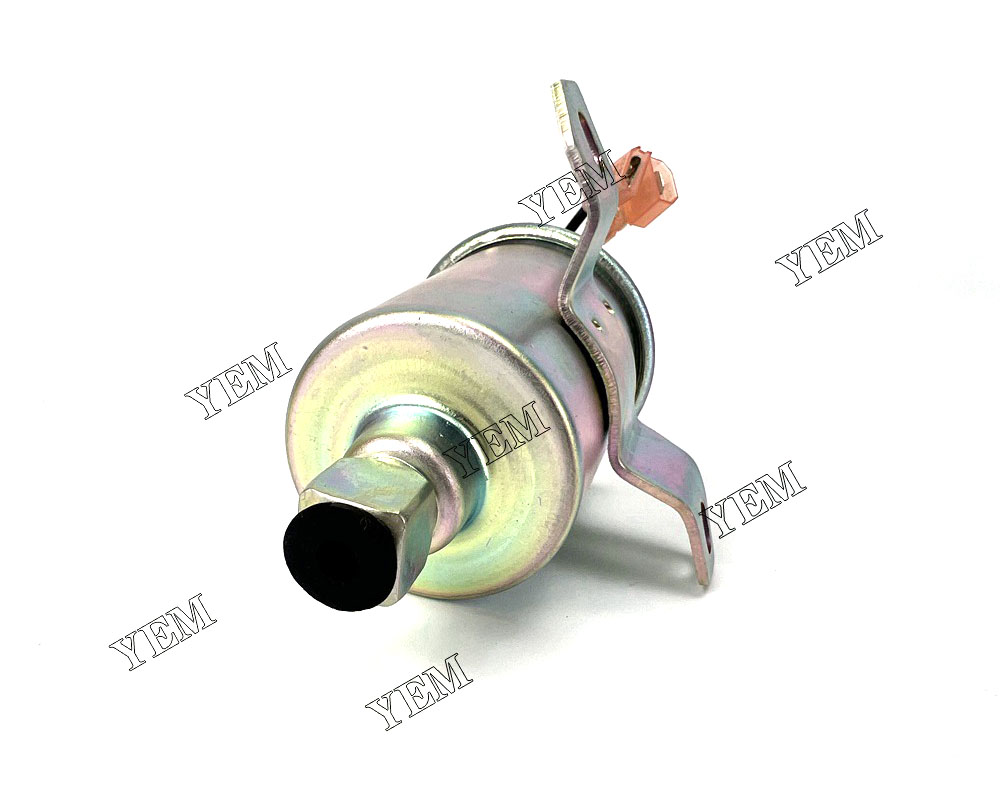
Generally speaking, there are many types of oil transfer pumps, which are suitable for liquid transfer needs in different industries and fields. The specific selection of the appropriate type depends on factors such as the nature of the conveying medium, flow requirements, pressure requirements, and the use environment.
Fuel transfer pump troubleshooting and maintenance
Troubleshooting and maintenance of oil transfer pumps are very important to ensure their normal operation and prolong their service life. Here are some common troubleshooting and maintenance actions:
- Troubleshooting:
- Check the power supply: ensure that the fuel pump is powered normally, and eliminate the power failure.
- Check the seal: check whether the packing seal or mechanical seal is damaged, and replace it in time if there is leakage.
- Clean the inlet pipe: If the inlet pipe is blocked or there are foreign objects, clean it in time to ensure that the liquid enters the pump body smoothly.
- Check the impeller: Check the impeller for damage, breakage or foreign objects stuck, clean or replace if necessary.
- Check the bearings: check if the bearings are well lubricated, if there is any abnormal noise or friction, add lubricating oil or replace the bearings if necessary.
- Maintenance measures:
- Regular inspection and replacement of seals: Regularly check the degree of wear of packing seals or mechanical seals, and replace them in time if necessary.
- Regularly maintain the lubricating system: check the lubricating system to ensure the quality and sufficient supply of lubricating oil, and replace and add lubricating oil in time.
- Clean the pump body and inlet and outlet: regularly clean the inside of the pump body and the inlet and outlet to prevent debris from accumulating and clogging.
- Regularly check the motor and transmission: check the running state of the motor and the fastening of the transmission, and perform maintenance and adjustments if necessary.
- Regularly check the performance and working conditions of the pump: regularly perform the performance test of the pump, check the flow, pressure and other parameters, find out the problems in time and take measures.
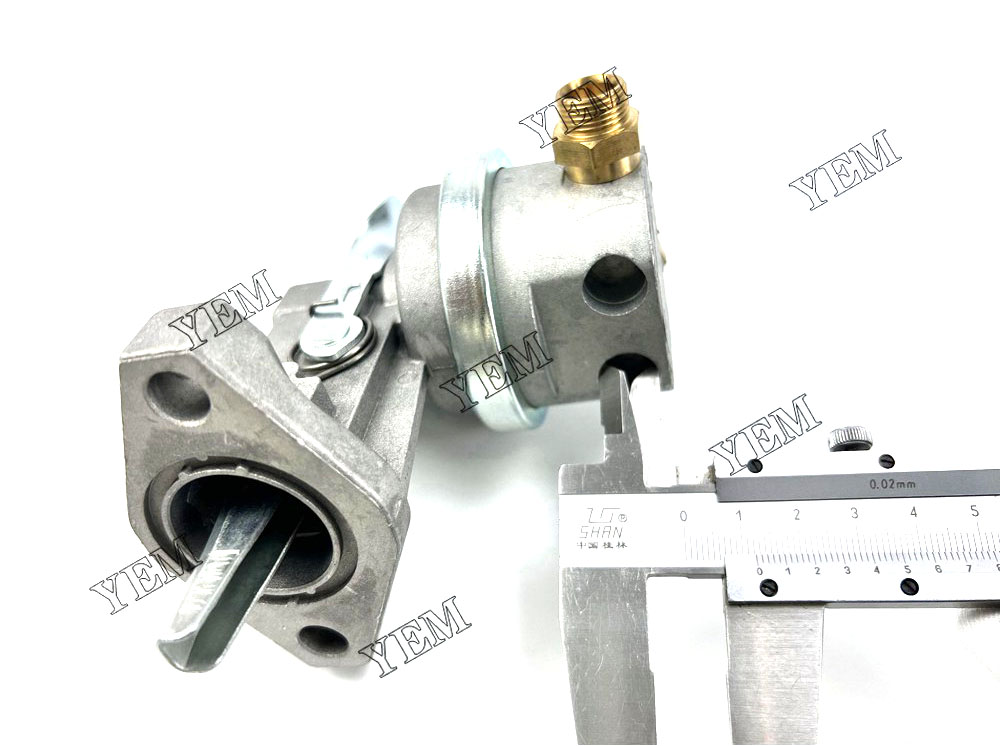
In addition, it is recommended to follow the specific operating manual and maintenance guidelines provided by the manufacturer to ensure proper use and maintenance. Regular maintenance and timely handling of faults can maximize the reliability and service life of the oil transfer pump.
Application areas of oil transfer pumps
The selection and installation of the oil delivery pump is an important link to ensure the normal operation of the oil delivery system. The following are general guidelines for sizing and installation:
- Selection:
- Determine the flow and pressure requirements: According to the flow and pressure requirements of the conveying medium, determine the required flow and head (pressure) range of the oil delivery pump.
- Consider the properties of the medium: consider the viscosity, temperature, corrosiveness and other characteristics of the conveying medium, and select the appropriate material and type of oil pump, such as stainless steel pumps for corrosive media.
- Consider environmental conditions: Consider the environmental conditions of the oil transfer pump, such as temperature, humidity, altitude, etc., and select a suitable oil transfer pump to ensure its reliable operation.
- Consider maintenance and maintenance: choose an oil transfer pump with good maintainability and maintainability to facilitate subsequent maintenance and maintenance work.
- Install:
- Positioning and foundation: According to the installation location and weight, select a suitable foundation and support structure to ensure that the oil transfer pump can be placed stably.
- Connecting pipelines: According to the specifications of the inlet and outlet of the oil pump, connect the inlet and outlet pipelines correctly to ensure smooth flow of pipelines and avoid leakage.
Sealing device: choose a suitable sealing device according to the medium characteristics, such as stuffing seal or mechanical seal, and ensure good sealing to prevent leakage.
- Driving device: According to the type and demand of the oil transfer pump, select the appropriate driving device, such as electric motor, engine, etc., and connect and debug correctly.
- Commissioning and testing: After the installation is completed, carry out necessary commissioning and testing to ensure the normal operation of the oil pump and check whether the parameters meet the requirements.
It is important that the selection and installation should be carried out according to the specific application requirements and environmental conditions. It is recommended to follow the installation manual and guidelines provided by the manufacturer to ensure correct selection and installation, and to ensure the safe and reliable operation of the oil transfer pump. If you are not sure, it is best to consult a professional engineer or technical support from the manufacturer.
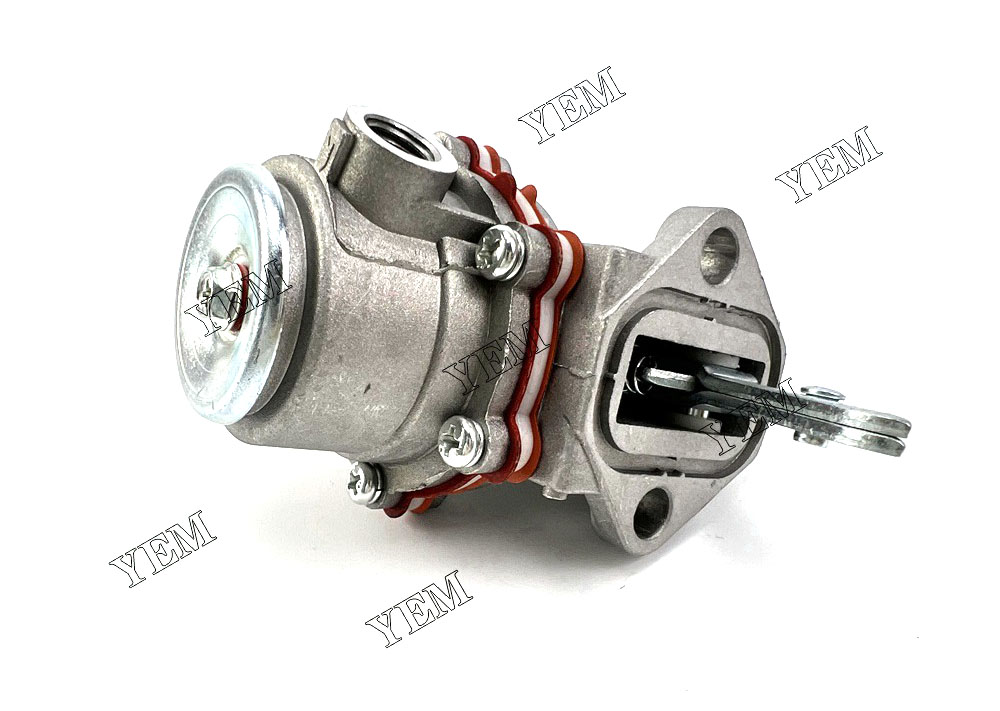
Oil pump industry trends and technological progress
In recent years, the fuel pump industry has made some important progress in technological innovation and development. Here is an overview of some industry dynamics and technological advances:
- Environmental protection and energy efficiency: With the increasing awareness of environmental protection and attention to energy consumption, the oil pump industry continues to promote the development and adoption of high-efficiency and energy-saving pump products. Use efficient power system and control technology to reduce pump energy consumption, and use energy-saving materials and Coulomb closed system to reduce leakage and pollution.
- Intelligence and automation: The oil pump industry pays more and more attention to the application of intelligence and automation technology. Through the use of advanced sensors, remote monitoring and control systems, remote monitoring, fault diagnosis and intelligent optimal control of the pump are realized. Improve operational efficiency and reduce manual intervention and maintenance costs.
- High-performance materials and coatings: In order to cope with the corrosion and wear of different media, the oil pump industry continues to research and adopt high-performance materials and coating technologies, such as corrosion-resistant alloys, ceramic coatings, etc., to improve the durability and resistance of pumps. corrosive.
- New pump design: In terms of pump design, some new pump designs have emerged to improve pump efficiency and reliability. For example, the application of new pumps such as screw pumps, magnetic pumps, and shaft sealless pumps is gradually increasing, with lower leakage risks and longer service life.
- Digitalization and virtual reality: Through digitalization technology and virtual reality technology, provide a visual and interactive working environment for design, simulation and training. This helps optimize product design and process flow, and provides better training and safety management.
Overall, the fuel pump industry is developing towards more efficient, energy-saving, intelligent and sustainable development. With the advancement of technology and the requirements of the industry, it is expected that new technologies and solutions will continue to emerge to promote the development and innovation of the fuel pump industry.
Standards and specifications related to oil transfer pumps
The design, manufacture and application of fuel pumps need to follow a series of standards and specifications to ensure product quality and safety. The following are some of the main standards and specifications related to oil transfer pumps:
- API standard:
- API 610: Standard for centrifugal pumps for the petroleum, petrochemical and natural gas industries, covering requirements for design, manufacture, installation and maintenance.
- API 674: Particular requirements for positive displacement pumps and axial piston pumps for pumping high pressure and high temperature media.
- API 675: Specification for Adjustable Positive Displacement Pumps for Accurate Metering and Delivery.
- API 682: Standard for Mechanical Seals and Sealing Systems to Control and Reduce Leakage in Pumps.
- ISO standard:
- ISO 2858: Standard specification for general purpose centrifugal pumps, centrifugal pumps for industrial applications.
- ISO 5199: Technical specification for chemical process pumps, for pumps in the chemical, petrochemical and pharmaceutical sectors.
- ASME standard:
- ASME B73.1: Particular requirements and dimensions for chemical process pumps, similar to ISO 5199.
- ASME B73.2: Requirements for corrosion-resistant centrifugal pumps, suitable for the transfer of corrosive media.
- ANSI/HI standard:
- ANSI/HI 1.6: Centrifugal Pump Efficiency Test Specification for testing and evaluating the performance of centrifugal pumps.
- ANSI/HI 11.6: Efficiency Test Specification for Positive Displacement and Axial Piston Pumps.
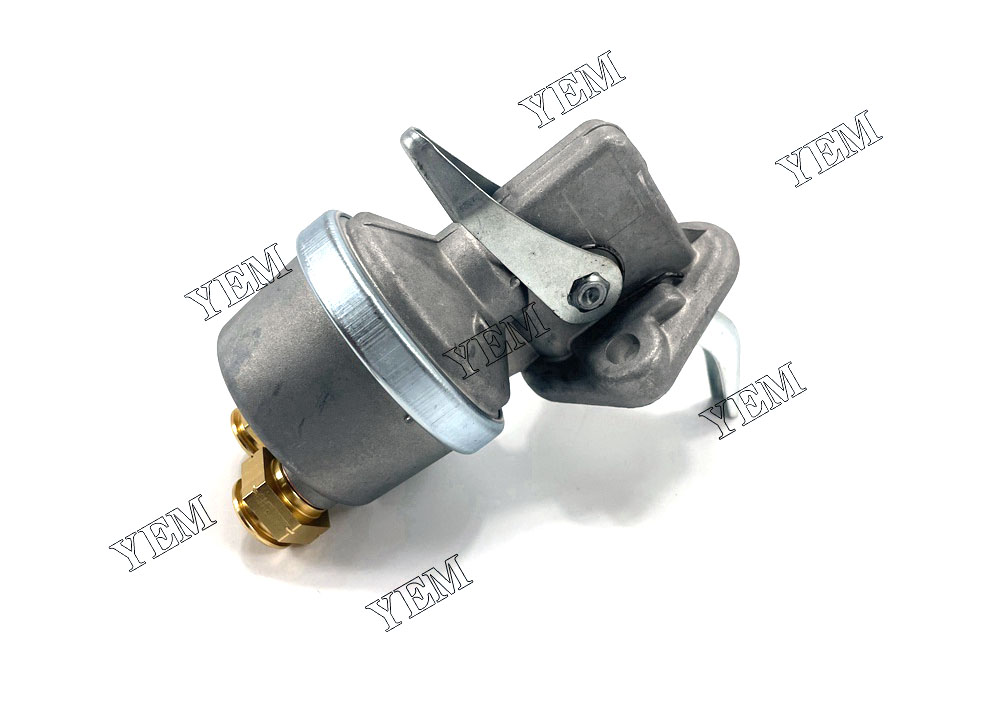
In addition to the main standards and norms mentioned above, there are some industry-specific standards, such as API 674 or API 675 for the oil and gas industry, and ISO 2858 for the chemical industry, etc. These standards and specifications provide guidance and basis for the design, manufacture and application of oil transfer pumps, and help ensure product quality, performance and safety. When selecting and using oil transfer pumps, it is recommended to refer to the applicable standards and codes and to follow the relevant installation and maintenance guidelines.
Contact us
Our YEM team comprises a dedicated group of skilled and passionate engineers and technicians specializing in excavator parts. With our years of experience and expertise, we are committed to delivering top-notch excavator accessories and comprehensive solutions tailored to meet our customers’ specific requirements.
We possess a profound understanding of various types and brands of excavators, along with a profound knowledge of their working principles and the functionalities of accessories. As a result, we can provide customers with accurate and professional recommendations. By forging partnerships with renowned excavator parts manufacturers and suppliers, we guarantee the quality and reliability of the products we offer.
Our services extend beyond the provision of excavator accessories. We also facilitate transportation, installation, repair, and after-sales support for these components. Whether you need to replace a damaged accessory or enhance the excavator’s performance and capabilities, our team can provide you with comprehensive solutions. We tailor the options to suit your needs and budget, ensuring a seamless experience throughout the installation and maintenance processes.
At YEM, customer satisfaction is our utmost priority. We strive to deliver excellent service and the best possible solutions. Should you have any inquiries or requirements, please do not hesitate to contact us. We are here to collaborate with you, offering high-quality excavator accessories and professional technical support.