The definition and function of excavator engine rocker arm
Excavator engine rocker arm refers to a part on the engine, which is used to control the switch of the engine valve. The rocker arm is connected to the valve shaft of the engine, and is connected to the camshaft through the rocker mechanism. As the camshaft rotates, the rocker arm transmits force to the valve to open or close the valve.
The function of the rocker arm is to control the opening and closing time and amplitude of the valve. It plays a role in transmitting force and changing the direction of movement, so that the engine valve can work correctly according to the design requirements. The rocker arm also plays a role in reducing the friction loss and noise of the engine. When the engine is working, the rocker arm helps the engine to run smoothly and maintains the stable opening and closing of the valve to ensure the normal working efficiency of the engine.
Structure and materials of excavator engine rocker arm
Excavator engine rocker arms are usually made of cast iron or cast steel. It is an important part connecting the engine cylinder and the valve, and is used to control the opening and closing of the valve. The rocker structure generally includes two parts, the rocker rod and the rocker seat.
The rocker lever is a long metal rod, one end is connected to the valve, and the other end is connected to the rocker seat. It needs to be strong and rigid enough to withstand engine workloads and vibrations. Typically, rocker levers are made of high-strength cast iron or steel for durability and reliability.
The rocker arm seat is a metal seat installed on the engine cylinder wall to support and fix the rocker arm rod. It needs to have good stiffness and stability to ensure the movement precision and reliability of the rocker arm. The rocker arm mount is also usually made of cast iron or cast steel material to meet its working requirements.
In short, the structure of the rocker arm of an excavator engine is generally composed of a rocker lever and a rocker seat, and the material is often made of cast iron or cast steel to meet its strength, rigidity and durability requirements.
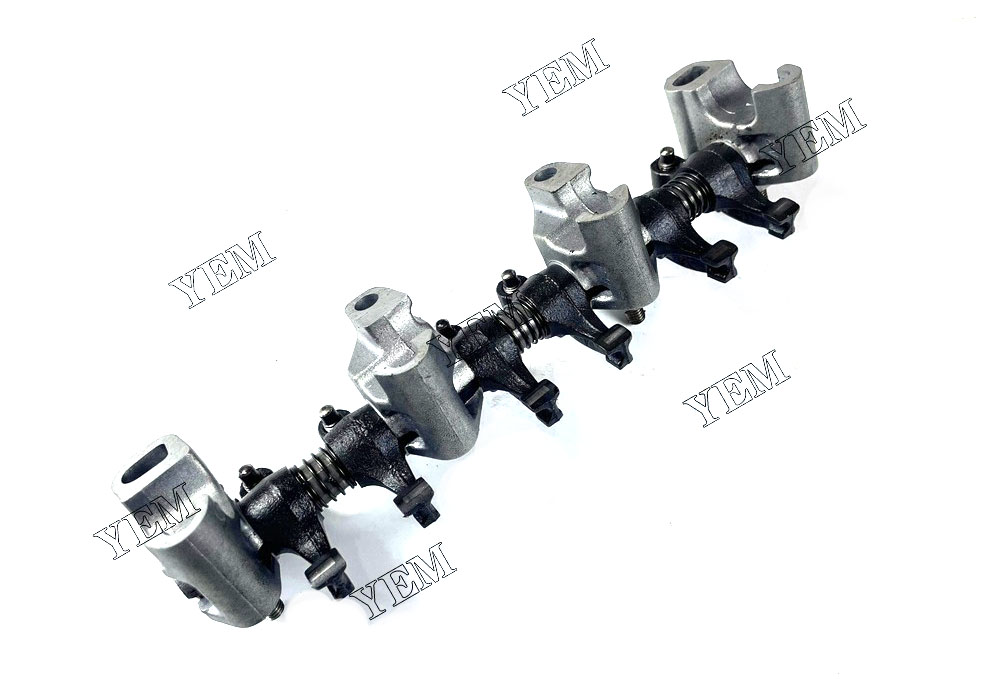
Excavator engine rocker arm
The working principle of the rocker arm of the excavator engine is to inject the compressed air or fuel in the engine cylinder to the valve through the cooperation of the rocker lever and the rocker seat to control the opening and closing of the valve.
When the piston in the engine cylinder rises, the rocker lever on the rocker seat will be pressed down by the air pressure in the cylinder. The lower end of the rocker lever is connected with the valve, and when the rocker lever is pressed down, the valve will also be pressed to close.
When the piston in the engine cylinder descends, the rocker arm on the rocker arm seat will be lifted up by the air pressure in the cylinder. The lower end of the rocker lever is connected to the valve, and when the rocker lever is lifted up, the valve is also lifted and opened, allowing gas or fuel to enter the cylinder.
Through the cooperative movement of the rocker lever and the rocker seat, the rocker arm can inject the compressed air or fuel in the cylinder to the valve, thereby controlling the opening and closing of the valve and realizing the normal operation of the engine. In this way, the engine can burn and discharge according to a certain rhythm, so as to drive the work of the excavator.
Excavator engine rocker arm
The manufacture and machining of engine rocker arms usually involves the following steps:
Design and simulation: Design and simulate the rocker arm according to the design requirements and performance requirements of the engine. This includes determining the size, shape and structure of the rocker arm, etc.
Material selection: Select the appropriate material according to the working requirements and load conditions of the rocker arm. Commonly used materials include cast iron, cast steel, etc., which have sufficient strength and wear resistance.
Casting: According to the design and simulation results of the rocker arm, the shape of the rocker arm is manufactured by casting process. Casting can be performed by sand casting, metal mold casting, and the like.
Finishing: After the casting is completed, the rocker arm needs to be finished to meet the design requirements and precision requirements. Finishing includes milling, drilling, grinding and other processes to ensure the accuracy of the size and shape of the rocker arm.
Surface treatment: In order to improve the surface quality and corrosion resistance of the rocker arm, surface treatment is usually carried out. Common surface treatment methods include heat treatment, coating, spraying, etc.
Quality inspection: In the process of manufacturing and processing, quality inspection of the rocker arm is required to ensure that it meets the design requirements and performance requirements. Commonly used quality inspection methods include dimensional measurement, hardness testing, non-destructive testing, etc.
Assembly and debugging: After the rocker arm is manufactured, it needs to be assembled and debugged to cooperate with other engine components to ensure the normal operation and motion accuracy of the rocker arm.
To sum up, the manufacture and processing of the engine rocker arm includes steps such as design and simulation, material selection, casting, finishing, surface treatment, quality inspection, assembly and debugging. Completion of these steps will ensure the quality and performance of the rocker arm to function properly in the engine.
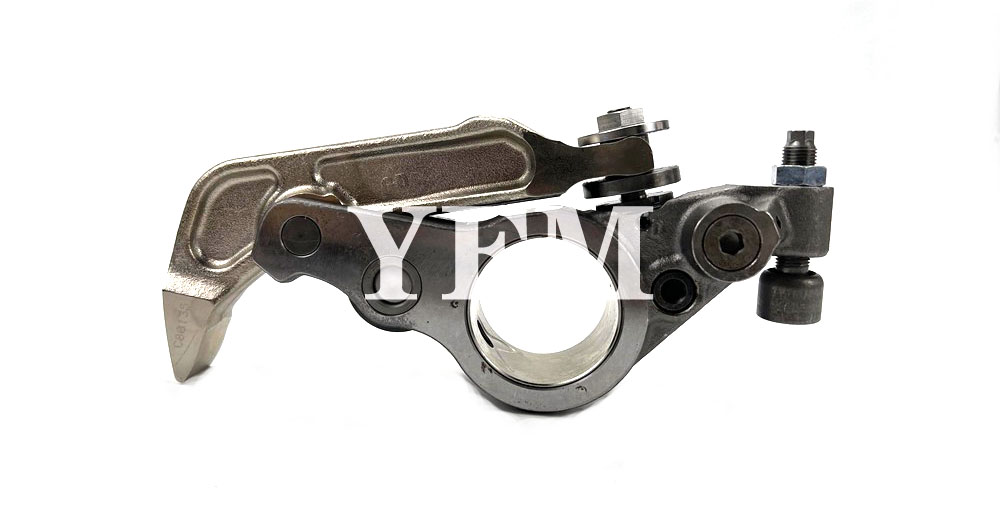
Application fields and development trends of engine rocker arms
Engine rocker arms are widely used in various fields such as internal combustion engines, diesel engines, automobile engines, ship engines, and construction machinery engines. The rocker arm plays an important role in connecting the cylinder and the valve in the engine, controls the opening and closing of the valve, and affects the working efficiency and performance of the engine.
In terms of the development trend of the engine rocker arm, there are mainly the following directions:
Lightweight: With the improvement of environmental protection and energy efficiency requirements, the lightweight of engine components has become an important development direction. By adopting new materials and design techniques, reducing the weight of the rocker arm can reduce the overall weight of the engine and improve fuel efficiency and power performance.
High strength and high durability: The engine rocker arm needs to withstand high frequency movement and high temperature and high pressure working environment, so it needs to have sufficient strength and durability. The development of higher strength and more durable materials and improved structural design can improve the life and reliability of rocker arms.
Reduce friction and wear: The contact surface between the rocker arm and the valve will generate friction and wear, affecting the efficiency and life of the engine. Research into new lubrication technologies and coating materials that reduce friction and wear can improve engine efficiency and reliability.
Electrification: With the development of electrification technology, future engines may use electric rocker arms to control the opening and closing of valves, thereby improving the accuracy and response speed of the engine. The electric rocker arm enables more precise valve control, improving combustion efficiency and emissions performance.
In general, the development trend of the engine rocker arm is lightweight, high strength, high durability, reduced friction and wear, and may develop in the direction of electrification. The application of these technologies will further enhance the performance, efficiency and reliability of the engine
Rocker related technologies and equipment
The related technology and equipment of rocker arm include:
CAD Design Software: Computer Aided Design (CAD) software is used to design and simulate the shape, size and structure of the rocker arm. Commonly used CAD software includes AutoCAD, Creo, SolidWorks, etc.
Casting equipment: Casting equipment used to manufacture the shape of the rocker arm. Common casting equipment includes sand casting equipment, metal mold casting equipment, etc.
Processing equipment: equipment used for finishing the cast rocker arm. Common processing equipment includes milling machines, drilling machines, grinding machines, etc.
Heat treatment equipment: equipment used to heat treat the rocker arm to improve the strength and durability of its material. Common heat treatment equipment includes furnaces, quenching equipment, etc.
Surface treatment equipment: equipment for surface treatment of rocker arms to improve their surface quality and corrosion resistance. Common surface treatment equipment includes spraying equipment, electroplating equipment, etc.
Quality testing equipment: equipment used for quality testing of rocker arms. Common quality inspection equipment includes coordinate measuring machines, hardness testers, non-destructive testing equipment, etc.
Test bench and test equipment: equipment used for performance testing and verification of rocker arms. Common test benches and test equipment include rocker arm fatigue test benches, rocker arm motion performance test equipment, etc.
The above are some examples of related technologies and equipment of the rocker arm. The application of these technologies and equipment can ensure the quality and performance of the rocker arm and meet the requirements and work needs of the engine.
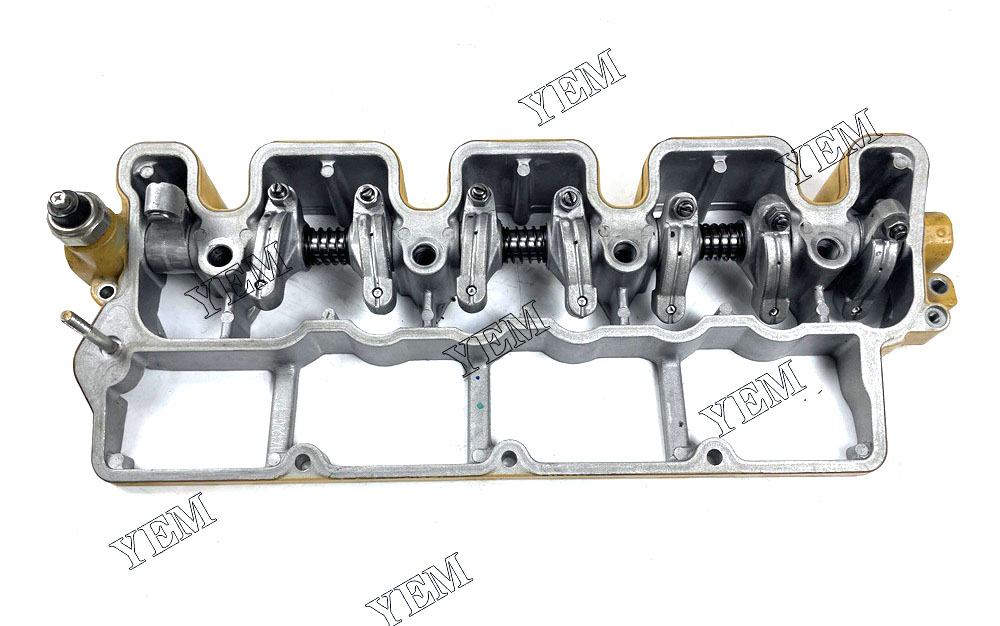
Rocker Arm Performance Testing and Evaluation
The performance test and evaluation of the rocker arm is to ensure that the quality, reliability and performance of the rocker arm meet the design requirements. The following are common rocker arm performance testing and evaluation methods:
Mechanical performance test: conduct static and dynamic mechanical performance tests on the rocker arm, including bearing capacity test, stiffness test, fatigue life test, etc. Evaluate the strength, stiffness and durability of the rocker arm by applying different loads and vibrations.
Dimensional measurement: measure each key dimension of the rocker arm to ensure its consistency with the design requirements. Commonly used dimensional measurement methods include three-coordinate measurement, projector measurement, caliper measurement, etc.
Surface quality evaluation: evaluate the surface quality of the rocker arm, including surface finish, surface roughness, etc. Commonly used surface quality assessment methods include optical inspection, surface roughness measurement, etc.
Wear and Friction Test: Evaluate the friction and wear between the rocker arm and the valve through a simulated test of the contact between the rocker arm and the valve. Commonly used testing methods include tribological testing, wear testing, etc.
Temperature and thermal stress test: Simulate the high temperature and thermal stress environment under the working conditions of the engine, and test the performance of the rocker arm under different temperatures and thermal stress. Commonly used test methods include thermal cycle test, thermal expansion test, etc.
Simulate the actual working condition test: assemble the rocker arm into the actual engine, conduct the actual working condition test, and evaluate the performance and reliability of the rocker arm under actual working conditions.
The above are common rocker arm performance testing and evaluation methods. Through these tests and evaluations, the quality and performance of the rocker arm can be guaranteed to meet the design requirements, and the working efficiency and reliability of the engine can be improved.
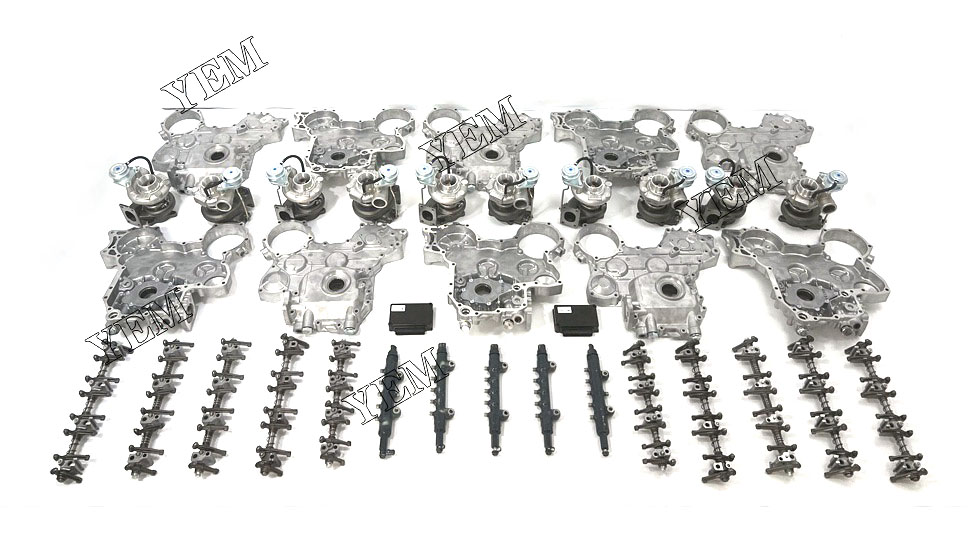
Rocker arm maintenance and upkeep
The maintenance and maintenance of the rocker arm is an important measure to ensure its normal operation and prolong its service life. The following are common maintenance and maintenance methods for rocker arms:
Regular inspection: Regularly check the appearance and connection parts of the rocker arm to ensure that there are no abnormalities such as cracks, deformation or looseness. Pay special attention to the contact surface between the rocker arm and the valve, and check for abnormal wear or damage.
Cleaning and maintenance: Regularly clean the rocker arm and its surrounding area to remove dust and debris. It can be cleaned with a soft brush or an air gun, and avoid using metal tools to scratch the surface of the rocker arm to avoid damage.
Lubrication and maintenance: According to the lubrication requirements of the rocker arm, apply appropriate lubricant to the rocker arm regularly. Lubricants can reduce the friction and wear between the rocker arm and the valve, and improve the working efficiency and life of the rocker arm.
Fastening inspection: Regularly check the connecting bolts and nuts of the rocker arm to ensure that they are fastened in good condition. If looseness or abnormality is found, it should be tightened or replaced in time.
Anti-corrosion and anti-rust: For the exposed surface of the rocker arm, anti-corrosion and anti-rust treatment can be carried out to prolong its service life. It can be painted with anti-rust paint or anti-corrosion paste.
Regular replacement: According to the service life and working conditions of the rocker arm, the rocker arm should be replaced regularly. When replacing, choose a rocker arm that meets the specifications and quality requirements, and replace it according to the correct installation steps.
Pay attention to the working environment: avoid exposing the rocker arm to harsh working environments, such as high temperature, high humidity, corrosive media, etc. If it must be used in these environments, corresponding protective measures should be taken.
In short, the maintenance and maintenance of the rocker arm can be carried out through measures such as regular inspection, cleaning and maintenance, lubrication maintenance, fastening inspection, anti-corrosion and anti-rust, regular replacement and attention to the working environment
Contact us
Thank you for reaching out to our YEM team. We take great pride in providing exceptional service and support to our valued customers. If you have any questions or need assistance, please don’t hesitate to reach out to us through any of the following channels:
Rest assured, we are here to assist you and are eager to resolve any inquiries you may have.