How Does a Fuel Shut Off Solenoid Work?
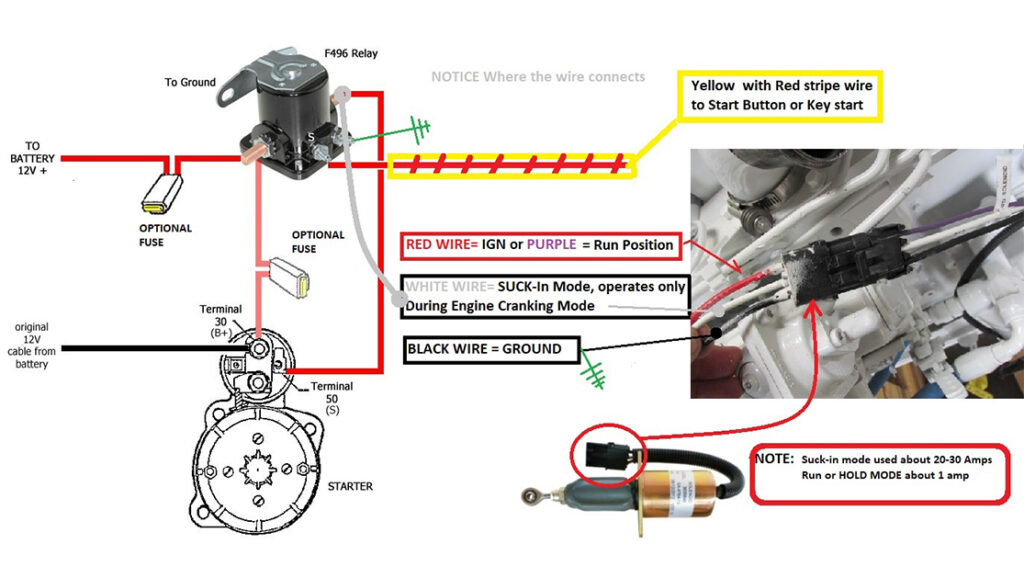
A fuel shut off solenoid is a pivotal component in engine management systems, serving the critical function of controlling the flow of fuel to an engine remotely.
This electromagnetically operated valve comprises a valve body, solenoid assembly, and a poppet valve with a spring mechanism.
Understanding its operation is key to appreciating its role in ensuring engine safety and efficiency.
Components of a Fuel Shut Off Solenoid
The fuel shut off solenoid consists of:
Valve Body: Houses the solenoid assembly and the internal components.
Solenoid Assembly: Includes a coil and plunger mechanism.
Poppet Valve and Spring Mechanism: Controls the flow of fuel through the valve.
Functioning of a Fuel Shut Off Solenoid
Activation Phase:
When energized, the solenoid generates an electromagnetic field.
This field attracts the solenoid’s plunger, which in turn lifts the spring-loaded poppet valve from its seat.
This action allows fuel to flow through the valve, facilitating the engine’s startup procedure.
Deactivation Phase:
Upon deactivation, the valve spring pulls the poppet valve back onto its seat.
This effectively shuts off the fuel flow, preventing any further supply to the engine when it is not in operation.
This mechanism safeguards against fuel flooding and potential hazards.
Operation Modes:
Fuel shut off solenoids can be activated:
Manually: Controlled directly by an operator.
Automatically: Integrated into engine management systems that monitor operational parameters and activate the solenoid as needed.
Applications and Significance
These solenoids are integral in various applications where remote fuel shut off is crucial, such as:
Automotive Industry: Used in diesel engines to control fuel supply and prevent engine damage.
Industrial Equipment: Ensures safety by cutting off fuel to engines or burners during emergencies or hazardous conditions.
Advantages of Fuel Shut Off Solenoids
Safety: Immediate response to hazardous conditions by swiftly cutting off fuel supply, thereby preventing potential accidents.
Efficiency: Ensures optimal engine performance by regulating fuel flow during start-up and shutdown phases.
Reliability: Designed to withstand harsh operating conditions and provide consistent performance in diverse environments.
Conclusion
In conclusion, the fuel shut off solenoid is a critical component that enhances the safety and efficiency of engines across various industries.
Its electromagnetically operated valve design allows precise control over fuel supply, contributing to the smooth operation and longevity of engines.
Whether manually activated or part of an automatic system, the fuel shut off solenoid plays a vital role in safeguarding against fuel-related hazards and maintaining overall engine performance.
Understanding its mechanisms and applications underscores its importance in modern engine management systems.
How to Troubleshoot the Furel Shut-off Solenoid if it Fails to Work?
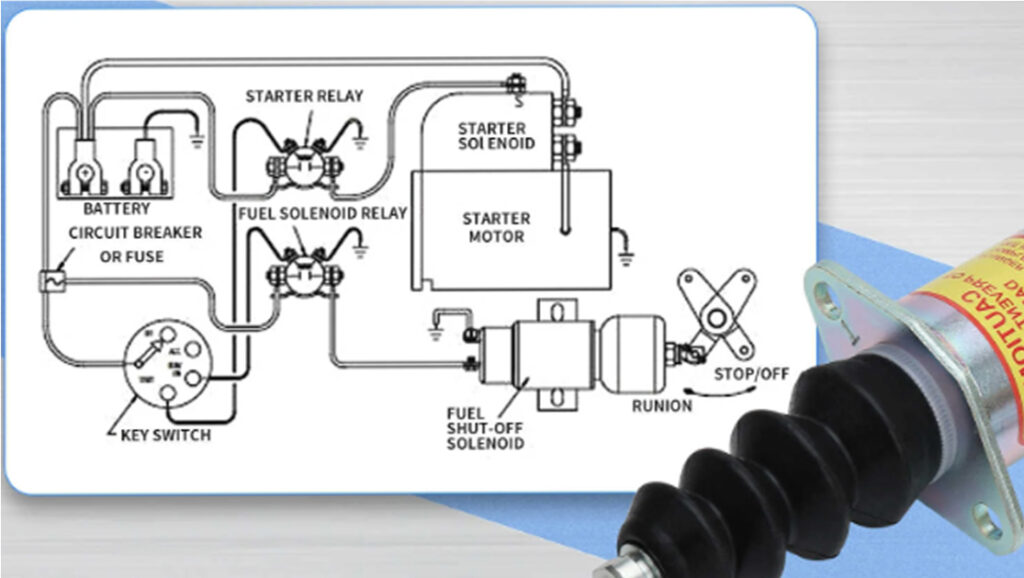
The fuel cut-off solenoid valve is a critical component within the fuel system of diesel engines, responsible for controlling the flow of fuel to the engine.
When this component malfunctions, it can disrupt engine operation and lead to potential issues.
To effectively troubleshoot and resolve problems with the fuel shut-off solenoid, it is crucial to follow a systematic approach.
Here’s an in-depth guide on how to troubleshoot a faulty fuel shut-off solenoid:
Introduction
The proper functioning of the fuel shut-off solenoid is essential for the reliable operation of diesel engines, ensuring fuel flow is managed effectively. Troubleshooting issues promptly helps maintain engine performance and prevents potential downtime.
Initial Checks
1. Power Connection
– Ensure the power connection to the solenoid is secure and not loose.
– Inspect wires for any signs of damage, corrosion, or wear.
– Use a multimeter to measure voltage at the solenoid terminals to verify proper power supply.
2. Verify Control Signal
– Utilize an oscilloscope or a voltmeter to check the integrity of the control signal.
– Analyze the waveform and voltage levels of the control signal to ensure they meet manufacturer specifications.
– Confirm that the control signal is reaching the solenoid as expected.
Inspect Core Components
3. Electromagnet and Spool
– Test the functionality of the electromagnet when the solenoid is energized.
– Ensure that the electromagnet generates sufficient magnetic force to actuate the solenoid effectively.
– Inspect the spool for any obstructions, such as dirt or debris, that may hinder its movement.
– Check for signs of wear or damage on the spool that could affect its performance.
Maintenance Practices
4. Cleaning and Regular Maintenance
– Regularly clean the fuel shut-off solenoid to prevent malfunctions caused by contaminants such as oil or dirt.
– Focus on cleaning the valve core and body thoroughly to maintain optimal operation.
– Follow manufacturer recommendations for cleaning agents and methods to avoid damaging sensitive components.
Critical Components
5. Springs and Seals
– Inspect the springs for any signs of damage, corrosion, or fatigue.
– Ensure that the springs provide sufficient tension for proper spool movement and return.
– Check seals for leaks or deterioration that could compromise the solenoid’s ability to maintain pressure and function correctly.
Examine Fuel Oil Circuit
6. Fuel Oil Circuit Inspection
– Evaluate the entire fuel oil circuit associated with the solenoid.
– Look for potential blockages or restrictions in fuel lines that could impact fuel delivery.
– Inspect connections for leaks that may affect the solenoid’s performance or lead to fuel loss.
Replacement of Faulty Components
7. Prompt Replacement
– If troubleshooting identifies a faulty component (e.g., solenoid, spool, springs, seals), replace it promptly.
– Use genuine or recommended replacement parts to ensure compatibility and reliability.
– Follow proper procedures for component replacement to avoid introducing new issues or compromising system integrity.
Testing and Debugging
8. Thorough Testing
– Conduct comprehensive testing after maintenance or repairs to verify the solenoid’s functionality.
– Test the solenoid under simulated operating conditions to ensure it operates as expected.
– Take necessary precautions during testing to prevent accidents or damage to equipment.
Conclusion
In conclusion, the diesel fuel shut-off solenoid valve is a critical component in diesel engine systems, regulating fuel flow for efficient and safe operation.
Proper troubleshooting techniques, including checking power connections, verifying control signals, inspecting core components, and maintaining cleanliness, are essential to quickly identify and resolve issues with the solenoid.
Regular maintenance and prompt replacement of faulty components ensure the reliable performance of the fuel shut-off solenoid, contributing to the overall longevity and efficiency of diesel engines.
By understanding and effectively troubleshooting the fuel shut-off solenoid, operators can minimize downtime and maximize engine reliability in various applications.
Contact us
Yem Parts is a company specializing in construction machinery parts, committed to providing customers with high-quality, high-performance, and durable parts products. The company not only has a first-class technical team, but also adheres to strict quality control standards to ensure that every component can meet user requirements.
The parts provided by Yem Parts cover multiple brands of excavators, loaders, bulldozers and other construction machinery, including Kubota, Doosan, Volvo, Caterpillar, etc., and based on years of deep involvement in the industry, it has accumulated a number of long-term Working with excellent suppliers can ensure that every component is of high quality and cost-effective.