The crankshaft plays a vital role in the engine. It is one of the key components that converts the up and down reciprocating motion of the piston into the rotational motion of the engine output shaft. Following are the functions and importance of crankshaft:
- Conversion motion type: The crankshaft converts the linear up and down reciprocating motion of the piston into the rotational motion of the output shaft. This conversion is the basis for the normal operation of the engine, allowing the internal combustion engine to generate power through continuous combustion and pushing of the piston.
- Balance and Stability: The balance of the crankshaft design is crucial to the stable operation of the engine. It must precisely balance the force of piston movement to ensure smooth engine operation and low vibration levels.
- Provide power output: The crankshaft drives mechanical equipment or vehicles through rotational motion. Therefore, it directly affects the engine output and performance.
- Support engine operation: The crankshaft not only converts the type of motion, but also plays a supporting role in supporting various internal components of the engine. It must be able to withstand operating conditions at high pressures and high rotational speeds while maintaining stability and durability.
- Affects fuel efficiency: The design and manufacturing quality of the crankshaft directly affect the fuel efficiency of the engine. By reducing friction losses and energy losses, an optimized crankshaft design can improve the engine’s fuel utilization, thereby reducing fuel consumption and emissions.
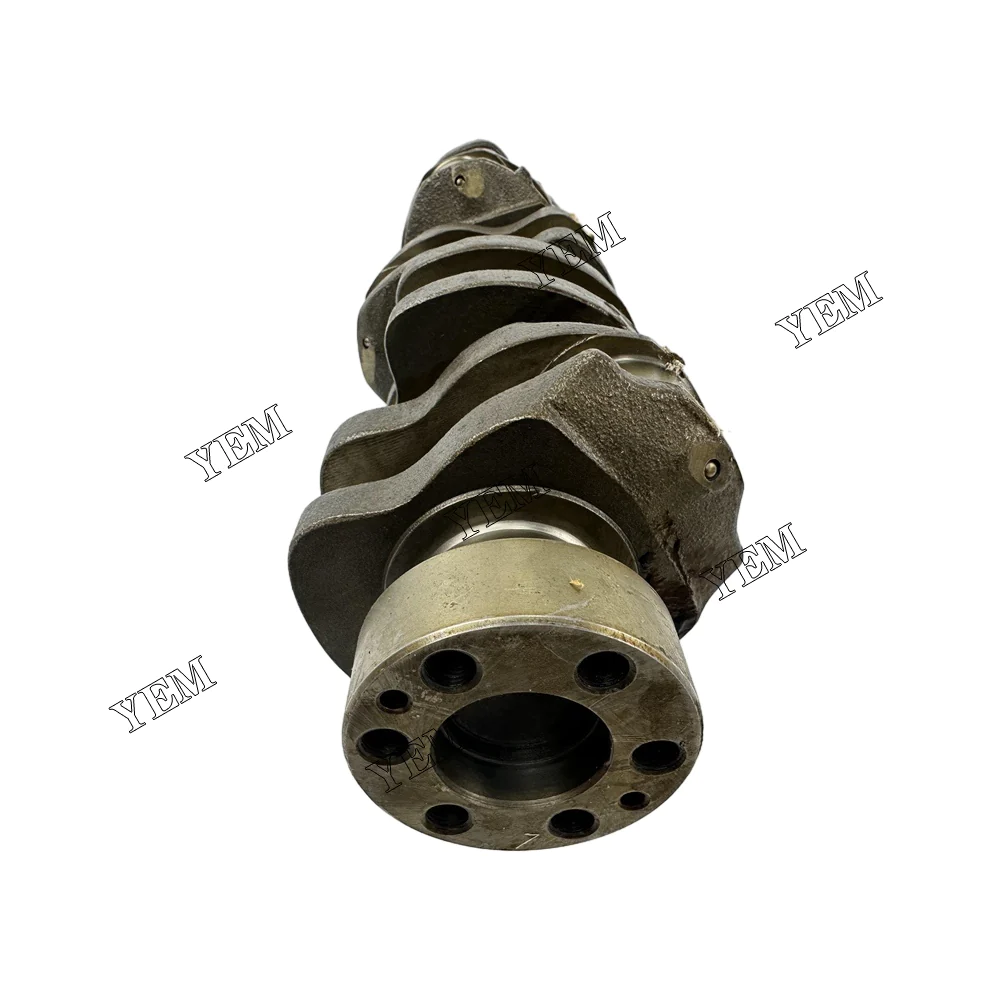
Therefore, the crankshaft can be said to be one of the most crucial components in the engine. Its design, manufacturing and performance directly affect the performance, stability and reliability of the engine. When selecting a crankshaft, consider its quality, balance, durability and suitability for a specific application to ensure the engine can achieve the expected performance requirements.
As a leading manufacturer of construction machinery and agricultural machinery, Kubota’s crankshaft design embodies the characteristics of high quality, high performance and high reliability. The following are Kubota crankshaft design features:
- Precision Machining: Kubota crankshafts undergo precision machining processes to ensure precise dimensions and smooth surfaces to minimize friction and energy loss and improve engine efficiency and performance.
- High-Quality Materials: Kubota crankshafts are made of high-quality cast iron or steel materials, which have excellent strength and wear resistance and can maintain stable working conditions under high pressure and high speed.
- Balance Design: Kubota crankshaft is well designed and has excellent balance, which can effectively reduce vibration and noise and improve engine stability and comfort.
- Professional testing: Kubota conducts strict quality control and testing on crankshafts, including dynamic balance testing, material strength testing, etc., to ensure that each crankshaft can meet high standards of performance and reliability requirements.
- Strong adaptability: Kubota crankshaft design is flexible and can be customized according to different engine models and application scenarios to meet the specific needs of customers and ensure a perfect match between the crankshaft and the engine.
- High durability: Kubota crankshafts have undergone long-term durability testing and can maintain stable working performance in harsh working environments, with long service life and reliability.
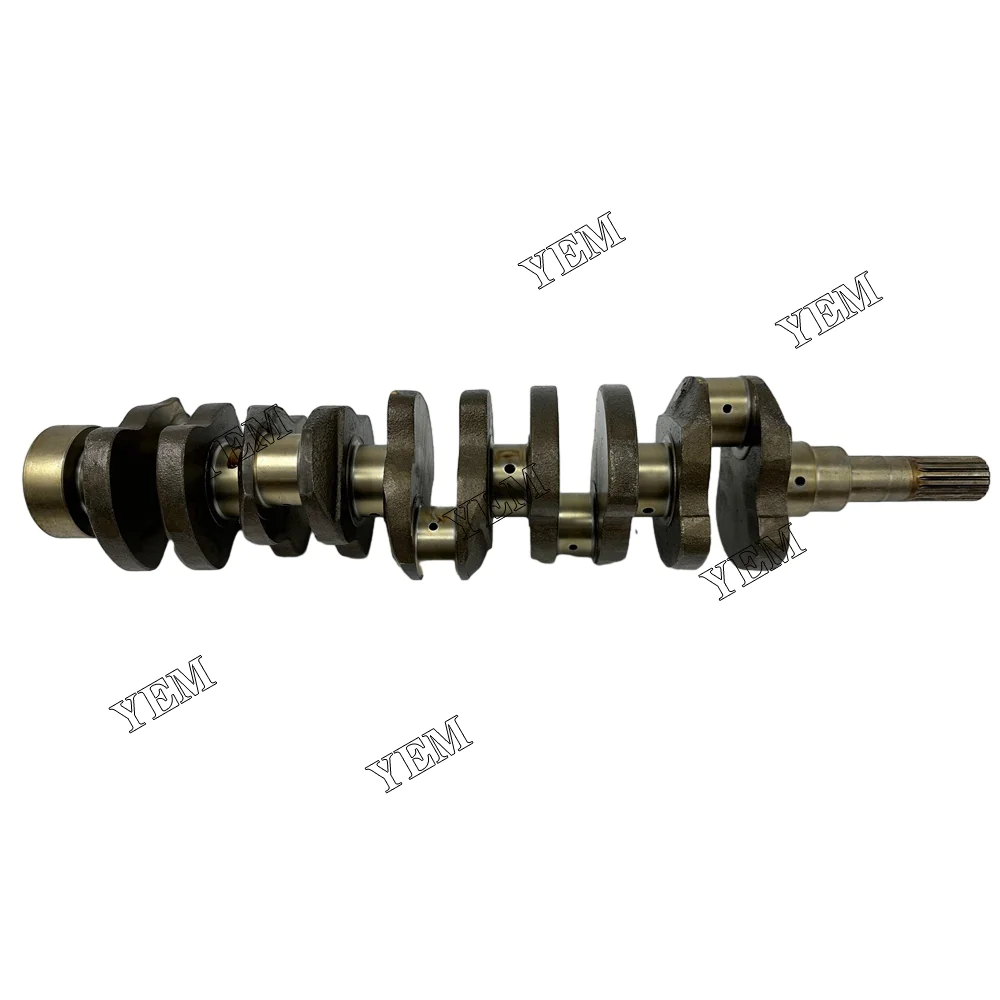
In general, Kubota crankshafts are well designed, reliable in quality and excellent in performance. They are suitable for various construction machinery and agricultural machinery and equipment, and are one of the first choices trusted by users. Its continuous pursuit of innovation and technological improvement has enabled Kubota crankshaft to always be at the forefront of the industry and provide customers with excellent products and services.
The manufacturing process of crankshaft is a complex and precise process, involving a variety of processing technologies and processes. The following is the general process flow of crankshaft manufacturing:
- Material Selection: Crankshafts are usually made of materials such as high-strength alloy steel or cast iron. The selection of materials should take into account factors such as the strength, hardness, wear resistance and processing performance required by the crankshaft.
- Forging: The manufacture of a crankshaft usually begins with a solid piece of metal blank. First, a metal blank of appropriate size is selected, heated and then forged. The forging process can improve the internal structure of the metal and increase its strength and durability.
- Rough machining: After forging, the crankshaft needs to be rough machined, including turning, milling and other operations, to process the overall shape and size of the crankshaft within the accuracy range required by the design.
- Heat treatment: After rough machining, the crankshaft needs to be heat treated, including quenching, tempering and other processes, to adjust the structure and performance of the material and improve its hardness and wear resistance.
- Finishing: After heat treatment, the crankshaft needs to be precision processed, including grinding, polishing and other processes to improve the smoothness and accuracy of the crankshaft surface and reduce friction and energy loss.
- Balance: After the crankshaft is processed, a dynamic balance test is required to ensure that the crankshaft will not produce excessive vibration and imbalance when rotating at high speed, and to ensure the smooth operation of the engine.
- Surface treatment: In order to improve the corrosion resistance and surface hardness of the crankshaft, the crankshaft is usually surface treated, such as coating, spraying, etc.
- Quality Inspection: Finally, the crankshaft needs to undergo strict quality inspection, including dimensional measurement, hardness testing, surface quality inspection, etc., to ensure that it meets the design requirements and standards.
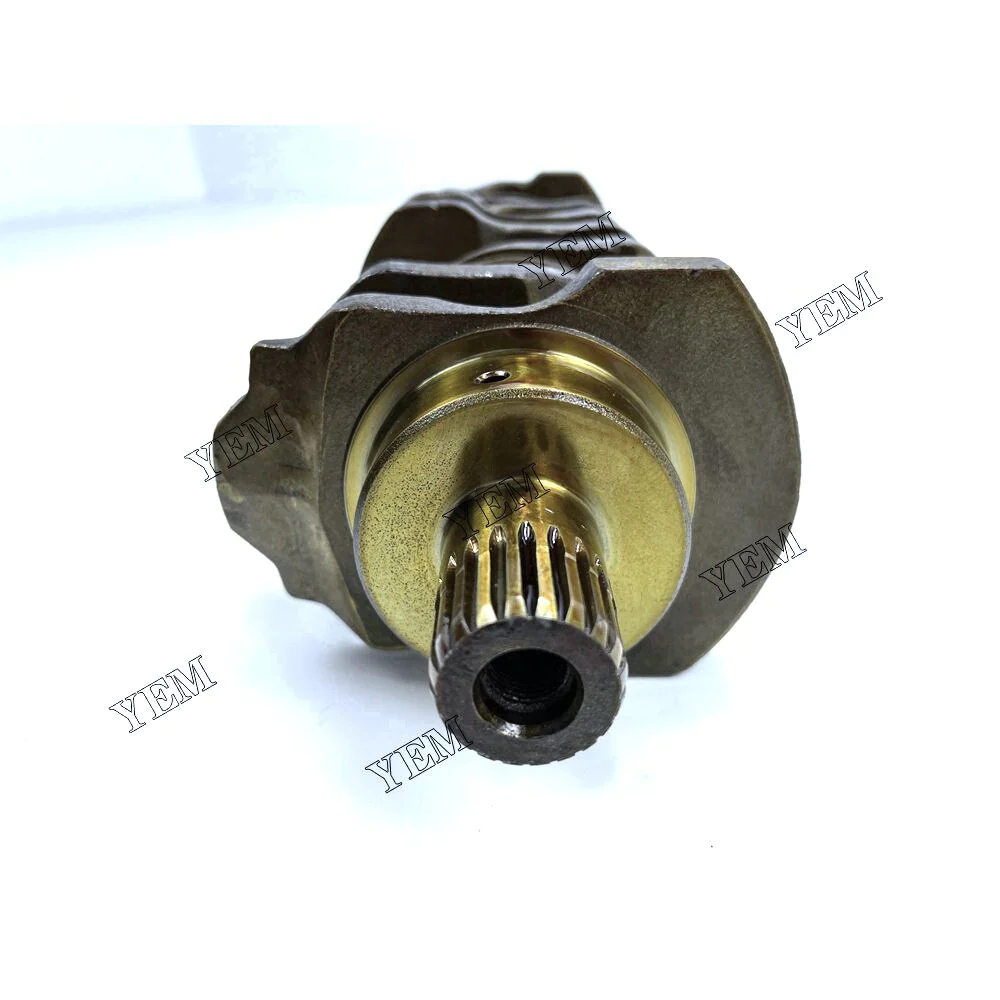
The precise operation and strict control of these processes ensure the quality and performance of the crankshaft, allowing it to play a stable and reliable role in the engine.
The crankshaft is an important component widely used in various internal combustion engines and mechanical equipment. Its application fields include but are not limited to:
- Automotive Engine: Automobile engine is one of the most common application fields of crankshaft. The crankshaft converts the up-and-down reciprocating motion of the piston into rotational motion, which drives the car’s tires.
- Motorcycle Engine: Similar to car engines, motorcycle engines also use a crankshaft to convert the motion of the piston into rotational motion to provide power to drive the motorcycle.
- Aircraft Engine: Aircraft engines also use a crankshaft as a conversion device to convert the linear motion of the piston into rotational motion to propel the aircraft into flight.
- Ship Engine: The working principle of a ship engine is similar to that of a car and motorcycle engine. It also requires a crankshaft to convert the movement of the piston into rotational motion to drive the ship.
- Construction Machinery: Crankshafts are also widely used in various engineering machinery and equipment, such as excavators, loaders, bulldozers, etc., to drive the engine to provide power to perform various engineering tasks.
- Agricultural machinery: Agricultural machinery and equipment such as tractors, harvesters, etc. also require crankshafts as a key component of power transmission to drive the engine to provide power to complete agricultural operations.
- Generator set: The engines in diesel generator sets and gasoline generator sets also need a crankshaft to convert the movement of the piston into rotational motion to drive the generator to generate electrical energy.
- Industrial Equipment: In addition to the above fields, crankshafts are also widely used in various industrial equipment, such as pumps, compressors, generators, etc., to convert and transmit power.

In general, the crankshaft, as a core power transmission device, plays a vital role in various internal combustion engines and mechanical equipment, and is one of the indispensable key components in modern industrial production.
Maintaining and servicing your crankshaft is critical to ensuring the proper operation of your engine and mechanical equipment. Here are some maintenance and care recommendations:
- Regular inspection of crankshaft: Regularly check the surface of the crankshaft for cracks, wear or other abnormalities. In particular, the installation parts of the main bearing of the crankshaft and the small end bearing of the connecting rod need to be carefully checked for abnormal wear or looseness.
- Keep Lubricated: The crankshaft needs good lubrication when running to reduce friction and wear. Check and replace the lubricating oil regularly to ensure that the crankshaft and bearings are in good lubrication condition.
- Avoid overload operation: Try to avoid running the engine or mechanical equipment under overload conditions for a long time. This will increase the load and wear of the crankshaft and shorten its service life.
- Pay attention to the operating temperature: The crankshaft is prone to deformation or thermal cracks at high temperatures, so ensure that the cooling system of the engine or mechanical equipment is working properly to avoid the crankshaft being overheated for a long time.
- Periodic balancing: Regularly check the balance status of the crankshaft, especially when the crankshaft has experienced a certain operating time or is subject to external impact, perform a dynamic balance test and make balance corrections as necessary.
- Replace worn parts in time: Once the crankshaft or other related parts are found to be severely worn or damaged, they should be replaced in time to avoid more serious damage.
- Keep it clean: Clean the crankshaft and other related parts regularly to ensure that their surfaces are clean to prevent dust, oil and other impurities from entering the bearings and affecting the lubrication effect.
- Follow manufacturer recommendations: The most important thing is to follow the maintenance and maintenance recommendations provided by the crankshaft manufacturer and operate according to its recommended maintenance intervals and methods to ensure the normal operation and long-term use of the crankshaft.
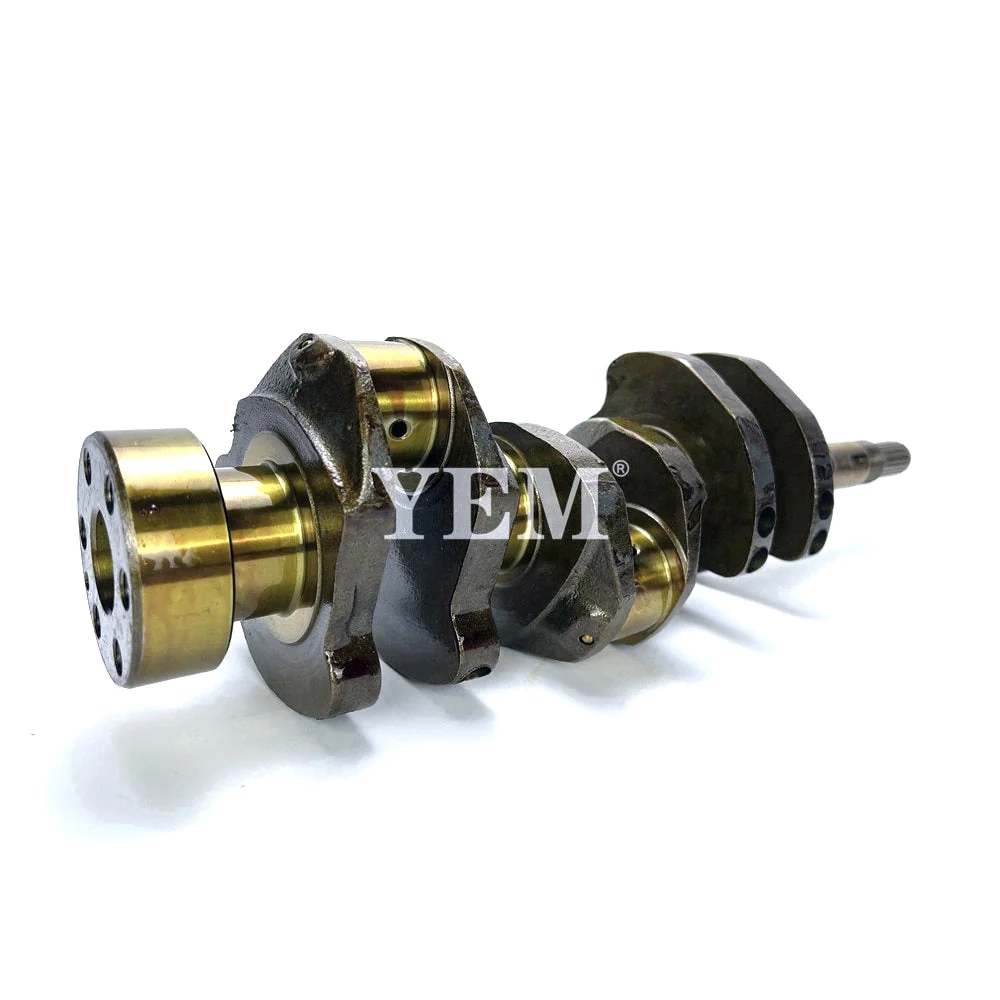
Through the above maintenance and upkeep measures, the service life of the crankshaft can be effectively extended, the stable operation of the engine and mechanical equipment can be ensured, and the failure rate and maintenance costs can be reduced.
Contact us
Thank you for your interest in YEMPARTS and our excavator parts. We have a dedicated team of experienced professionals ready to assist you with any inquiries or issues you may have regarding part identification, accessories, customer guidance, and more.
Please note that machinery engine parts can be complex, so if you have any product-related questions, we may need to contact you to gather additional information. To ensure the best results, it would be helpful if you could provide us with your model number, serial number, engine number, part number, or even pictures of your old parts.
To receive a free quotation, please leave your information by emailing us at :power@yempart.com. Our team will promptly respond to your inquiry and provide you with the necessary information.
Thank you again for considering YEMPARTS for your excavator parts needs. We look forward to serving you!