The role and importance of engine oil seal
The engine oil seal plays a crucial role in the proper functioning and longevity of the engine. Here are some key points highlighting its role and importance:
- Prevents oil leakage: One of the primary functions of the engine oil seal is to prevent the leakage of engine oil. It seals the gaps and spaces between moving parts, ensuring that the oil remains contained within the engine system.
- Protects engine components: The oil seal helps to protect various engine components from the harmful effects of oil leakage. It prevents oil from reaching areas where it can cause damage, such as the ignition system, timing belt, or electrical connections.
- Maintains proper lubrication: Engine oil is responsible for lubricating the moving parts within the engine. The oil seal ensures that the oil stays within the engine, allowing it to flow to the critical components that require lubrication for smooth operation.
- Reduces friction and wear: By maintaining a proper oil seal, friction and wear between engine components are minimized. This helps reduce the overall stress on the engine, leading to improved efficiency and a longer lifespan.
- Enhances engine performance: A well-functioning oil seal helps maintain the proper oil pressure within the engine, ensuring optimal lubrication. This, in turn, contributes to improved engine performance, including smoother operation, better fuel efficiency, and reduced emissions.
- Prevents contaminants entry: The oil seal acts as a barrier to prevent contaminants like dirt, dust, and debris from entering the engine. This helps maintain the cleanliness of internal components, minimizing the risk of damage or interference with the engine’s operation.
In summary, the engine oil seal plays a critical role in maintaining the integrity of the engine’s lubrication system, preventing oil leakage, protecting components, reducing wear, and improving overall engine performance and longevity. Regular inspection and replacement of worn or damaged oil seals are essential to ensure the optimal function of the engine.
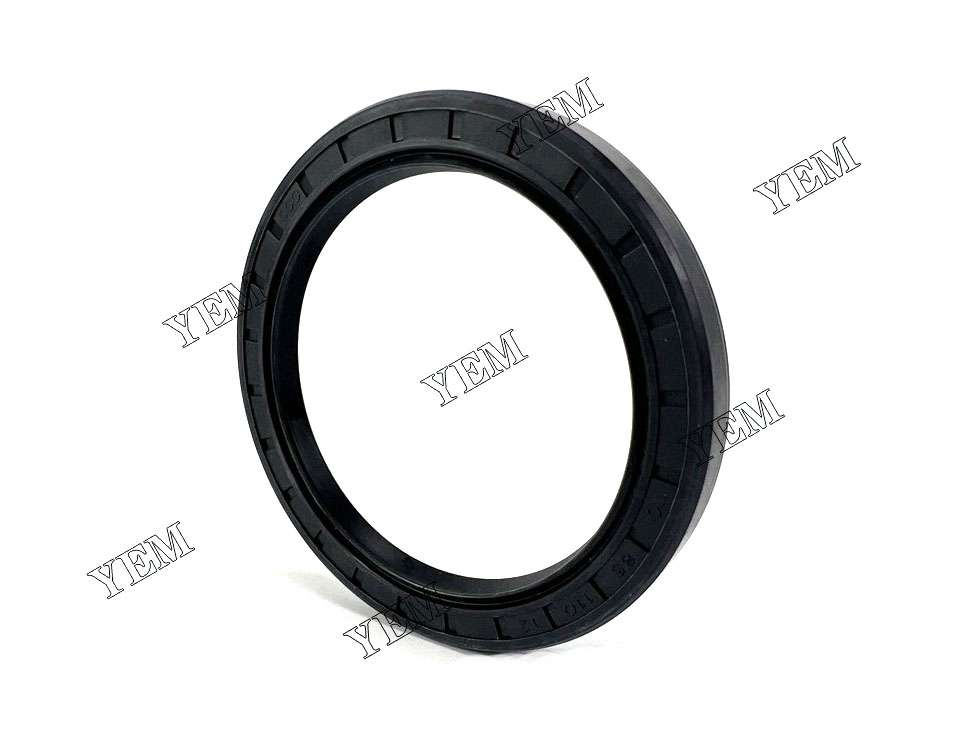
Common engine oil seal failures and causes
Common engine oil seal failures can occur due to various reasons. Here are some common failures and their potential causes:
- Oil leakage: Oil leakage is a common failure associated with engine oil seals. Possible causes include:
- Wear and tear: Over time, the oil seal can wear out or deteriorate, leading to gaps and leakage.
- Improper installation: Incorrect installation or improper sealing can cause oil leakage.
- High pressure or excessive heat: Extreme pressure or heat can cause the oil seal to fail and result in leakage.
- Contamination: Presence of contaminants, such as dirt or debris, can compromise the integrity of the oil seal and cause leakage.
- Seal hardening or shrinking: Engine oil seals can harden or shrink over time, leading to failure. Possible causes include:
- Age and usage: Continuous exposure to heat, pressure, and oil can cause the seal material to degrade and lose elasticity.
- Inadequate maintenance: Lack of regular oil changes or maintenance can accelerate seal deterioration.
- Seal damage: Engine oil seals can become damaged, resulting in leaks or compromised function. Possible causes include:
- Physical damage: Accidental impact, improper handling, or contact with sharp objects can damage the seal.
- Misalignment or misinstallation: Incorrect installation or misalignment during assembly can cause damage to the seal.
- Contamination or clogging: Engine oil seals can get clogged or contaminated over time, affecting their performance. Possible causes include:
- Dirty or low-quality engine oil: The use of dirty or low-quality oil can lead to the accumulation of debris or sludge around the seal.
- Improper maintenance: Neglecting regular oil changes or using the wrong type of oil can contribute to seal contamination.
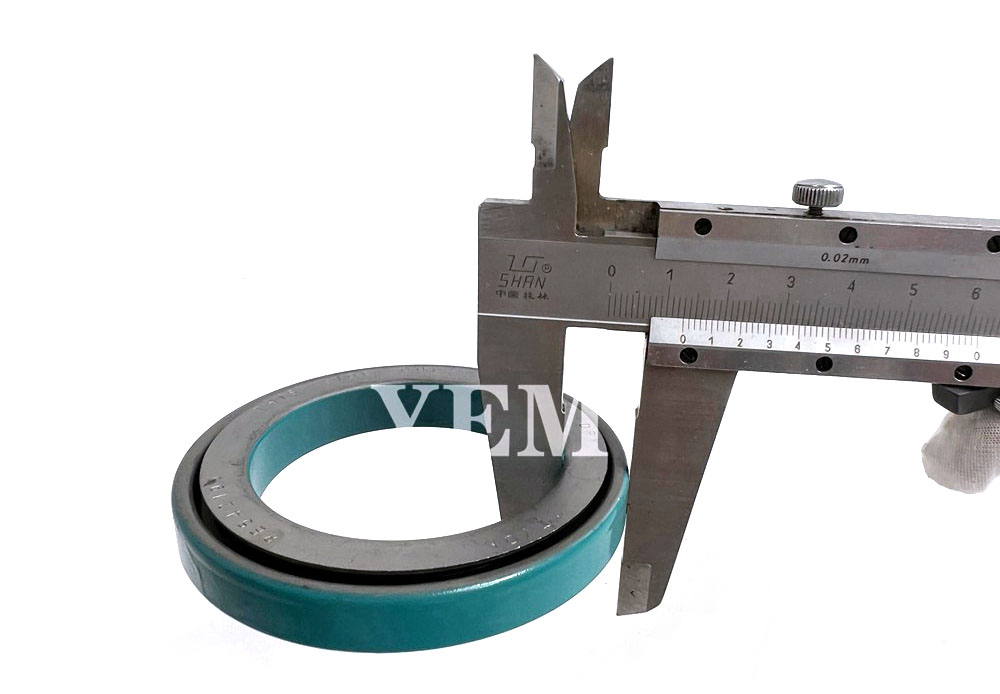
It’s important to note that the specific causes of oil seal failures can vary depending on the engine type, usage conditions, and maintenance practices. Regular inspection, timely replacement of worn or damaged seals, and adherence to proper maintenance procedures are crucial to prevent oil seal failures and maintain the integrity of the engine’s lubrication system.
Choose the right engine oil seal
Choosing the right engine oil seal is crucial for ensuring proper sealing and preventing oil leakage. Here are several factors to consider when selecting the appropriate oil seal:
- Compatibility: Ensure that the oil seal is compatible with the specific engine make and model. Different engines may have varying requirements in terms of dimensions, materials, and design.
- Material: Oil seals are commonly made of materials such as rubber, silicone, or polytetrafluoroethylene (PTFE). Consider factors such as the operating temperature range, resistance to chemicals and fluids, and durability when selecting the material. For example, PTFE seals offer excellent heat resistance and chemical compatibility, while rubber seals are more economical but may not withstand high temperatures as well.
- Design: The design of the oil seal should match the application requirements. There are various types of oil seals, including radial lip seals, axial lip seals, and camshaft seals. The design should take factors such as shaft speed, direction of rotation, and pressure differentials into account.
- Quality: Choose oil seals from reputable manufacturers or suppliers known for producing high-quality seals. Quality seals are less likely to fail prematurely and offer better sealing performance.
- OEM specifications: Refer to the original equipment manufacturer’s (OEM) specifications or recommendations for the engine. OEM specifications often provide detailed information on the required oil seal dimensions, materials, and performance criteria.
- Professional advice: If you are unsure about the right oil seal for your engine, consult with a qualified mechanic, engine specialist, or the manufacturer’s technical support for expert advice.
By considering these factors and ensuring the compatibility, material, design, quality, and adherence to OEM specifications, you can choose the right engine oil seal that will effectively seal the engine and prevent oil leakage.
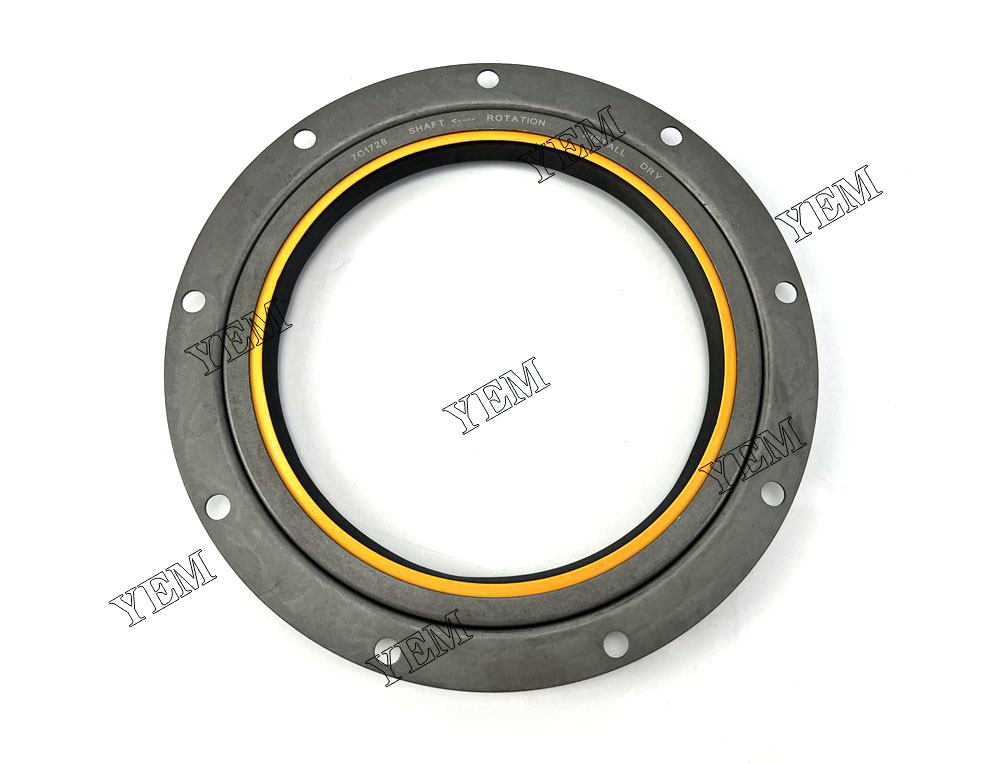
Installation and maintenance of engine oil seal
Proper installation and maintenance of engine oil seals are crucial for their effectiveness and longevity. Here are some guidelines to follow:
Installation:
- Preparation: Ensure that the sealing surfaces are clean and free from dirt, debris, and old seal remnants. Thoroughly clean the surfaces with an appropriate solvent if necessary.
- Lubrication: Apply a small amount of clean engine oil to the sealing lip of the oil seal before installation. This lubrication helps to prevent dry start-up and minimize friction during initial operation.
- Alignment: Pay attention to the proper alignment of the oil seal during installation. Use a seal installation tool or a suitable alternative to press the seal squarely into the housing or bore. Avoid cocking or tilting the seal, as it can lead to improper sealing and premature failure.
- Inspection: Inspect the sealing surfaces and shaft for any signs of damage or wear. If necessary, address any issues before installing the new oil seal to prevent further problems.
Maintenance:
- Regular inspection: Periodically check for any signs of oil leakage around the seal area. If you notice any leaks or oil seepage, it may indicate a failing or worn-out seal that requires replacement.
- Monitoring oil levels: Keep an eye on the engine oil level to ensure it remains within the recommended range. Oil leaks from faulty seals can lead to oil loss, which can negatively impact engine performance and longevity.
- Cleanliness: Maintain cleanliness around the engine area to prevent the accumulation of dirt and debris, which can potentially damage the oil seal. Regularly clean the engine and ensure that surrounding components are in good condition.
- Follow manufacturer recommendations: Refer to the engine manufacturer’s guidelines for specific maintenance instructions related to oil seal inspection and replacement intervals. Adhering to these recommendations can help ensure optimal seal performance and longevity.
- Professional assistance: If you encounter persistent oil leakage or face challenges with oil seal installation or maintenance, it is advisable to seek assistance from a qualified mechanic or automotive professional. They can provide expertise and guidance tailored to your specific engine and circumstances.
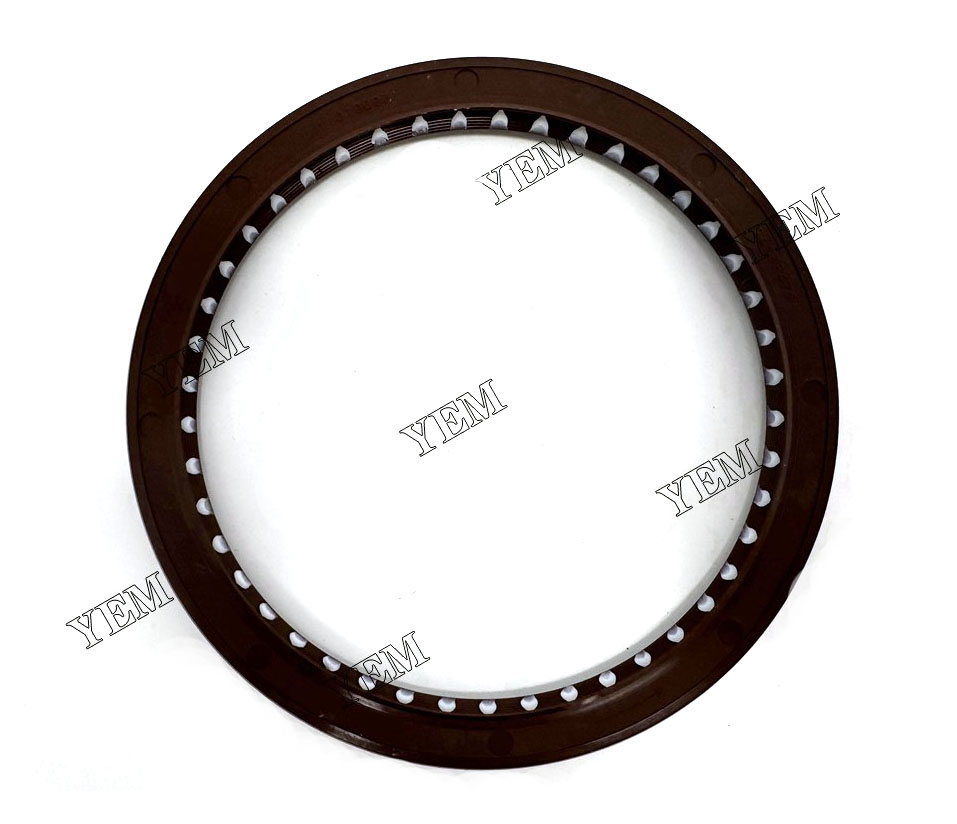
By following these installation and maintenance guidelines, you can help ensure the proper functioning and longevity of engine oil seals, ultimately minimizing the risk of oil leakage and related issues.
The Latest Engine Oil Seal Technology and Innovation
When it comes to the latest engine oil seal technology and innovation, several advancements have been made to improve the performance and longevity of engine oil seals. Here are a few notable developments:
- Advanced Materials: Traditional rubber seals have been replaced with high-performance materials like synthetic rubbers and elastomers. These materials offer better resistance to heat, friction, and chemical degradation, resulting in improved seal life and performance.
- Coatings and Treatments: Engine oil seals are now being treated with specialized coatings and treatments that enhance their performance. For example, some seals are coated with PTFE (polytetrafluoroethylene) for reduced friction, improved sealing, and resistance to oil leaks.
- Integrated Sealing Systems: Modern engines are equipped with integrated sealing systems that improve overall sealing efficiency. These systems often include multiple seals and gaskets working together to enhance performance, reduce leaks, and prevent contamination.
- Adaptive Sealing Technologies: Some engine oil seals now feature adaptive technologies that dynamically adjust their sealing properties based on various conditions. These adaptive seals can accommodate changes in temperature, pressure, and vibration, providing better sealing effectiveness and reducing the risk of oil leaks.
- Sensor Technology: Advanced engine oil seal technologies incorporate built-in sensors to monitor the condition of the seal and detect potential issues in real-time. This allows for timely maintenance or replacement, preventing major failures and reducing downtime.
It’s important to note that while these advancements improve the performance and reliability of engine oil seals, regular maintenance, such as oil changes and inspections, remains crucial for optimal seal function. Consult your vehicle manufacturer or a trusted mechanic for specific recommendations on oil seal technology and maintenance for your vehicle.
Engine oil seal case study
One notable case study related to engine oil seals is the implementation of advanced materials and design in the automotive industry.
Case Study: SKF’s Dynamic Lip Seals
SKF, a leading manufacturer of bearings and seals, developed an innovative engine oil seal solution known as the Dynamic Lip Seal (DLS). This seal was designed to address the challenges faced by traditional radial shaft seals in automotive engines, such as high operating temperatures, aggressive fluids, and dynamic application conditions.
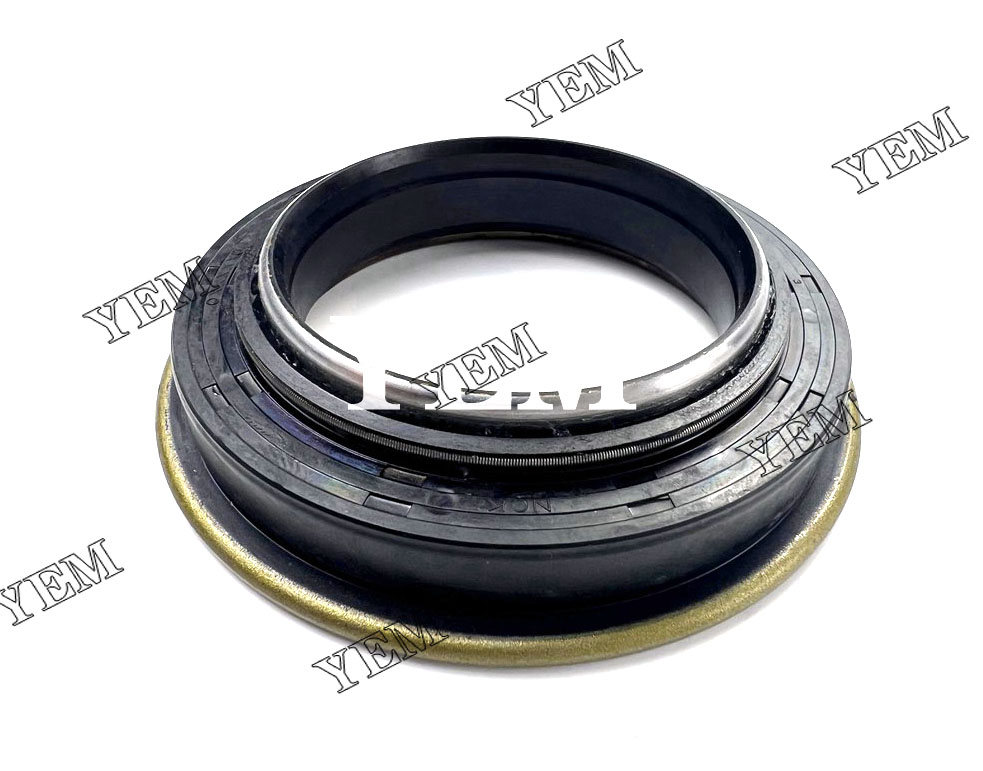
The SKF DLS features a unique design that incorporates advanced materials and a dynamic lip profile. Some key features and benefits of this seal include:
- Enhanced Lubricant Retention: The dynamic lip profile of the DLS seal facilitates better retention of oil within the engine while preventing leakage. This improves lubrication and reduces the risk of engine damage due to insufficient oil supply.
- Reduced Friction and Wear: The use of low-friction materials, combined with optimized lip geometry, minimizes friction and wear between the seal and the rotating shaft. This not only prolongs the seal’s lifespan but also improves engine efficiency and power output.
- Resistance to Contaminants: The DLS seal is designed to resist various contaminants present in the engine environment, such as dirt, dust, and chemicals. This helps maintain proper seal performance and prevents premature seal failure.
The implementation of SKF’s Dynamic Lip Seals has shown positive results in increasing the reliability and durability of engine oil seals. These seals have been used in various automotive applications, including passenger cars, commercial vehicles, and racing engines, contributing to improved engine performance, reduced maintenance costs, and overall customer satisfaction.
It’s worth noting that this is just one example of an engine oil seal case study, and there are many other innovative solutions and advancements being implemented by different manufacturers in the industry.
Contact us
Our YEM team comprises a dedicated group of skilled and passionate engineers and technicians specializing in excavator parts. With our years of experience and expertise, we are committed to delivering top-notch excavator accessories and comprehensive solutions tailored to meet our customers’ specific requirements.
We possess a profound understanding of various types and brands of excavators, along with a profound knowledge of their working principles and the functionalities of accessories. As a result, we can provide customers with accurate and professional recommendations. By forging partnerships with renowned excavator parts manufacturers and suppliers, we guarantee the quality and reliability of the products we offer.
Our services extend beyond the provision of excavator accessories. We also facilitate transportation, installation, repair, and after-sales support for these components. Whether you need to replace a damaged accessory or enhance the excavator’s performance and capabilities, our team can provide you with comprehensive solutions. We tailor the options to suit your needs and budget, ensuring a seamless experience throughout the installation and maintenance processes.
At YEM, customer satisfaction is our utmost priority. We strive to deliver excellent service and the best possible solutions. Should you have any inquiries or requirements, please do not hesitate to contact us. We are here to collaborate with you, offering high-quality excavator accessories and professional technical support.