The working principle and function of engine oil-water separator
The working principle of an engine oil-water separator is based on the difference in density between oil and water. It functions to separate the oil and water mixture, allowing for the removal of water and the proper lubrication of the engine.
The engine oil-water separator typically consists of a separator element or filter media, housing, inlet, and outlet ports. When the mixture of oil and water enters the separator, it passes through the filter media. The filter media is designed to allow the oil to pass through while blocking the water.
The filter media typically uses hydrophobic properties, meaning it repels water and allows oil to pass through. As the mixture flows through the filter media, the water droplets adhere to the media and coalesce into larger droplets due to their cohesive properties. These larger droplets then settle at the bottom of the separator due to gravity.
The separated water is collected in a sump or collection chamber at the bottom of the separator and can be drained periodically. On the other hand, the oil flows through the filter media and exits through the outlet port, ready to lubricate the engine components.
The function of the engine oil-water separator is crucial in protecting the engine from the harmful effects of water. Water in the engine oil can lead to decreased lubrication, corrosion of engine parts, and potential engine damage. By effectively separating the oil and water, the separator ensures that the engine is properly lubricated and operates efficiently.
It is important to note that while an engine oil-water separator can effectively separate oil and water, regular maintenance is necessary to ensure its proper function. This includes periodic inspection, cleaning or replacement of the filter media, and draining the collected water from the separator.
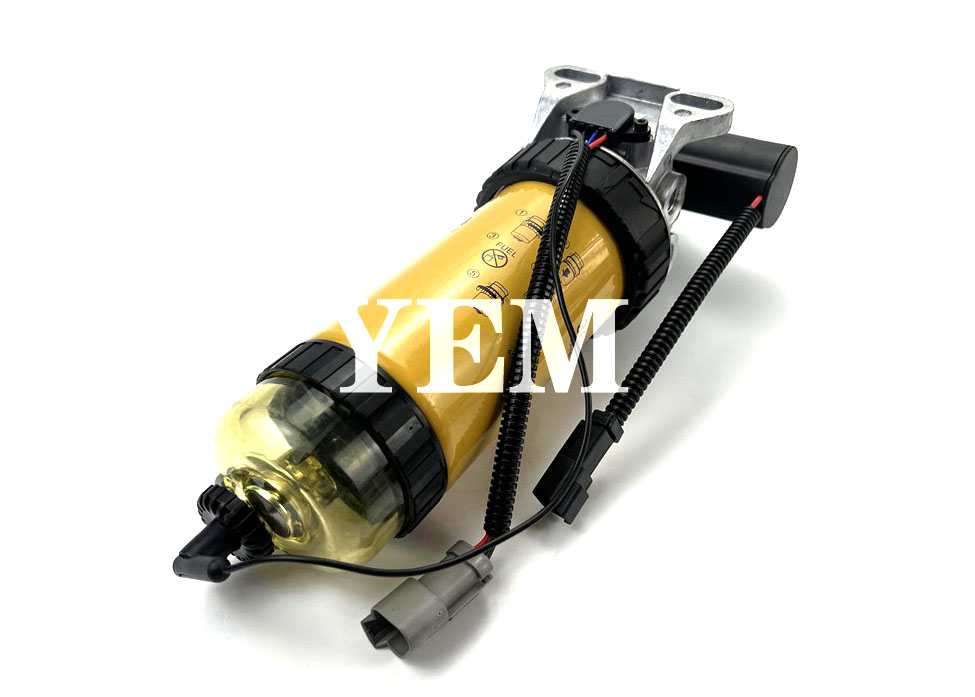
Different types of engine oil and water separators
There are various types of engine oil and water separators available, each with its own design and functionality. Here are some common types:
- Coalescing Separators: These separators use filter media that coalesce smaller water droplets into larger ones, making it easier for the droplets to be separated from the oil. Coalescing separators typically have a combination of hydrophobic and oleophilic (oil-attracting) filter media to effectively separate water from the oil.
- Centrifugal Separators: These separators rely on centrifugal force to separate oil and water. The mixture is introduced into a cylindrical chamber, where it is spun at high speeds. Due to the difference in density, the heavier water droplets are forced to the outer edges of the chamber and collected, while the lighter oil is directed towards the center for further use.
- Gravity Separators: Gravity separators, also known as oil-water gravity separators or simple oil separators, work on the principle of gravity. The mixture of oil and water enters a large tank where the separation occurs naturally. The oil, being less dense, rises to the top, while the water settles at the bottom. Baffles and weirs may be used to enhance the separation process.
- Membrane Separators: Membrane separators use specialized membranes that allow only oil molecules to pass through while blocking water molecules. These membranes are typically made of hydrophobic materials that repel water and selectively allow oil to permeate. Membrane separators are effective in removing even trace amounts of water from the oil.
- Electrostatic Separators: Electrostatic separators utilize electrical charges to attract and separate water droplets from oil. The mixture is passed through an electrostatic field that charges the water droplets, causing them to cluster together and separate from the oil. These separators can achieve high levels of water removal.
The selection of the appropriate type of engine oil and water separator depends on factors such as the intended application, the volume and type of contaminants, required efficiency, and available space for installation. It is recommended to consult with experts or manufacturers to determine the most suitable separator for specific needs.
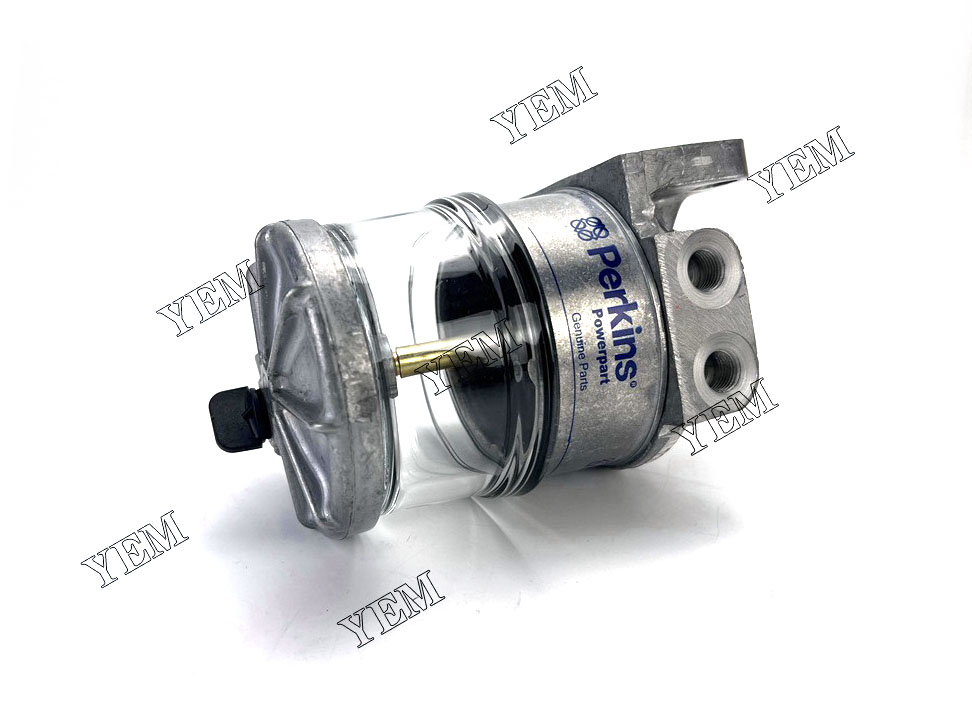
Installation and maintenance of engine oil-water separator
Installation and maintenance of an engine oil-water separator are crucial for its effective and efficient operation. Here are some general guidelines:
Installation:
- Determine the optimal location: Choose a suitable location for the separator that allows easy access for maintenance and meets any local regulations or guidelines.
- Proper plumbing: Ensure that the separator is installed in the oil-water system’s plumbing correctly. The separator should be integrated into the system with appropriate inlet and outlet connections.
- Use quality materials: Use high-quality pipes, fittings, and connectors to ensure proper functioning and durability. Ensure that all connections are secure and leak-free.
- Follow manufacturer’s instructions: Read and follow the manufacturer’s installation guidelines and recommendations to ensure proper setup and functionality.
- Maintenance:
- Regular inspections: Inspect the oil-water separator regularly for any signs of damage, leaks, or clogs. Check the condition of the internal elements, such as coalescing plates or filters, and clean or replace them if needed.
- Clean or replace components: Depending on the type of separator, clean or replace the coalescing plates, filters, or other components as recommended by the manufacturer or based on your maintenance schedule.
- Monitor performance: Keep an eye on the separator’s performance to ensure proper oil-water separation. If you notice any significant decrease in efficiency, address the issue promptly.
- Follow maintenance schedule: Adhere to the recommended maintenance schedule provided by the manufacturer. This may include regular inspections, cleaning, and component replacements.
- Training and expertise: Ensure that the individuals responsible for maintaining the oil-water separator are adequately trained and have the necessary expertise.
- Remember, these guidelines are general in nature, and it’s essential to refer to the specific instructions and recommendations provided by the manufacturer of your engine oil-water separator for accurate installation and maintenance procedures.
Raw materials and manufacturing processes of oil-water separators
Oil-water separators are devices designed to separate and remove oil, grease, and other contaminants from water. The raw materials used and manufacturing processes employed in their production can vary depending on the specific type and design of the separator. However, here are some general aspects to consider:
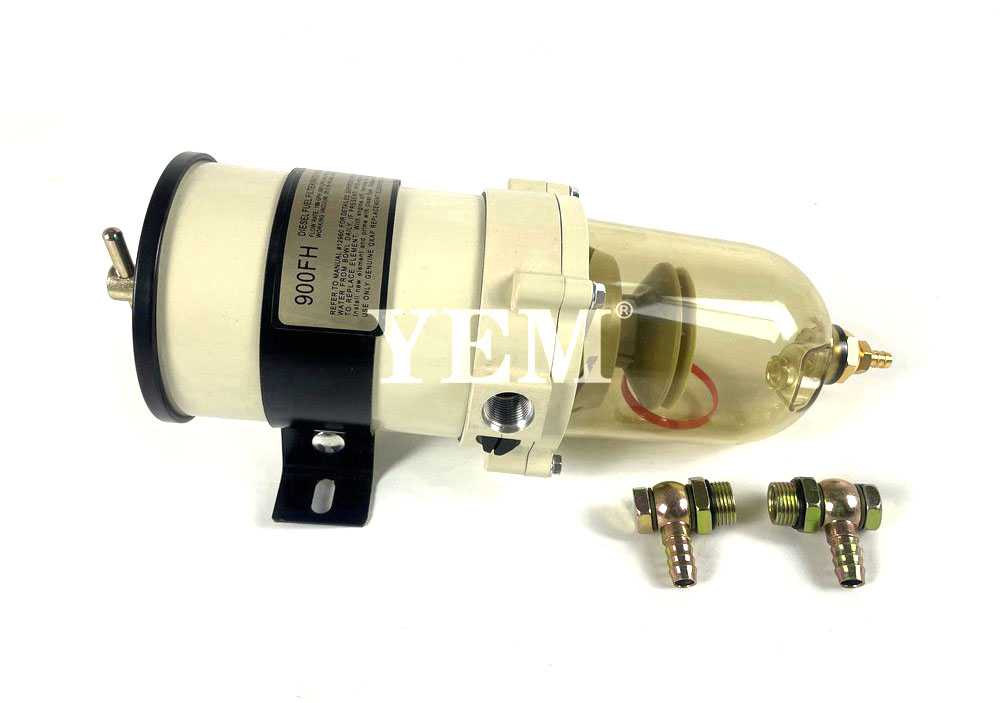
Raw materials:
- Tank and housing: The main body of the separator is typically constructed using corrosion-resistant materials such as steel, stainless steel, or synthetic materials like fiberglass or polyethylene.
- Coalescing media: Many oil-water separators incorporate coalescing media, such as coalescing plates, media packs, or cartridges. These are usually made from materials like polypropylene, fiberglass, or special synthetic fibers that have a high affinity for oil.
- Collection and discharge components: Drain valves, collection sumps, and discharge outlets are typically made from materials like PVC (polyvinyl chloride), stainless steel, or other corrosion-resistant materials.
Manufacturing processes:
- Tank fabrication: The tanks or housings are manufactured using techniques such as welding, molding, or forming, depending on the chosen raw material. Steel tanks are often fabricated using welding processes, while fiberglass tanks are typically fabricated using a molding process.
- Coalescing media production: Coalescing media, like plates or cartridges, are manufactured by shaping or forming the chosen material into the desired geometry. This can involve processes such as injection molding, extrusion, or assembly of multiple layers.
- Component assembly: After the individual parts are produced, they are assembled into a complete oil-water separator unit. This may involve joining the tank, installing the coalescing media, fitting drain valves, and other necessary components.
- Quality control: Throughout the manufacturing process, quality control measures are implemented to ensure that the finished oil-water separators meet the required specifications and standards. This often includes inspections, testing, and certification processes.
It’s important to note that the specific materials and manufacturing processes can vary among manufacturers and may also depend on the intended application and size of the oil-water separators. It is recommended to consult with specific manufacturers to understand the exact details of their products.
Typical problems and solutions
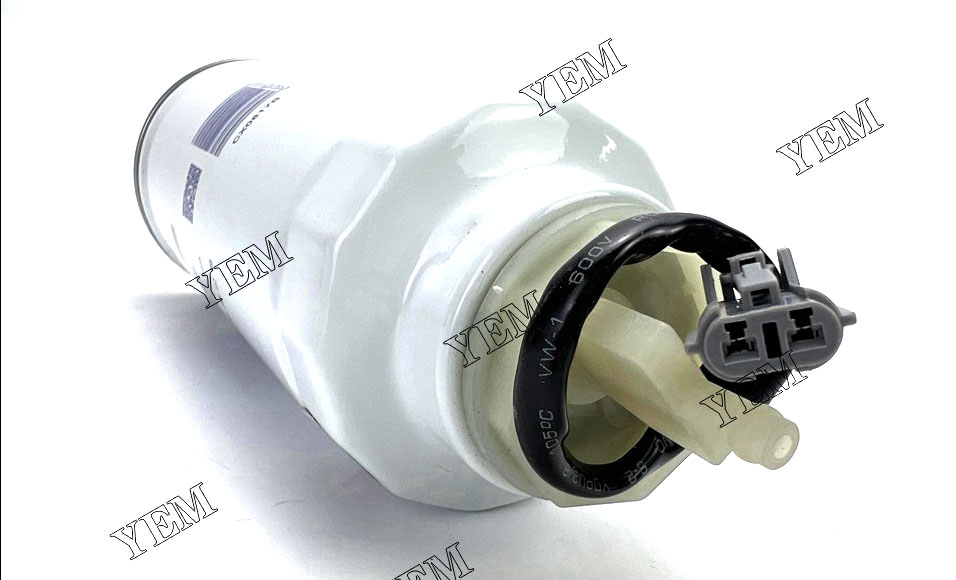
Typical problems that can occur with oil-water separators include:
- Ineffective oil-water separation: The separator may fail to effectively separate oil and water, resulting in high oil content in the discharged water. This can be caused by clogged or degraded coalescing media, improper sizing of the separator, or excessive flow rates.
Solution: Regular inspection, maintenance, and cleaning of the coalescing media are essential to ensure proper functioning. If the separator is undersized or experiencing high flow rates, upgrading to a larger or more efficient separator may be necessary.
- Accumulation of sludge or solids: Over time, solid particles and sludge can accumulate in the separator, impairing its performance and potentially causing blockages.
Solution: Regular cleaning and removal of accumulated solids are crucial to maintaining optimum performance. This can involve manual cleaning, backwashing, or using solids-handling mechanisms installed within the separator.
- Corrosion and deterioration: If the construction materials are not corrosion-resistant, the separator can corrode over time, leading to leaks, structural degradation, and decreased effectiveness.
Solution: Selecting appropriate corrosion-resistant materials during the manufacturing process is key to preventing this issue. Regular inspections and maintenance, such as coating or painting exposed surfaces, can help mitigate corrosion.
- Maintenance and operational issues: Lack of regular maintenance, failure to perform necessary inspections, and improper operation can result in overall system inefficiency.
Solution: Implementing a routine maintenance schedule and following proper operating procedures are essential. This includes monitoring water levels, checking and cleaning components, and ensuring proper drainage and disposal of collected oil.
- Environmental compliance: If the separator fails to meet environmental regulations and discharge limits, it can lead to legal and environmental issues.
Solution: Regularly monitoring the water quality, ensuring compliance with relevant regulations, and implementing proper treatment and disposal methods for the captured oil are vital.
It’s important to note that specific problems and solutions can vary depending on the design, size, and operating conditions of the oil-water separator. Regular maintenance, monitoring, and adherence to manufacturer guidelines are crucial for optimal performance and longevity of the separator.
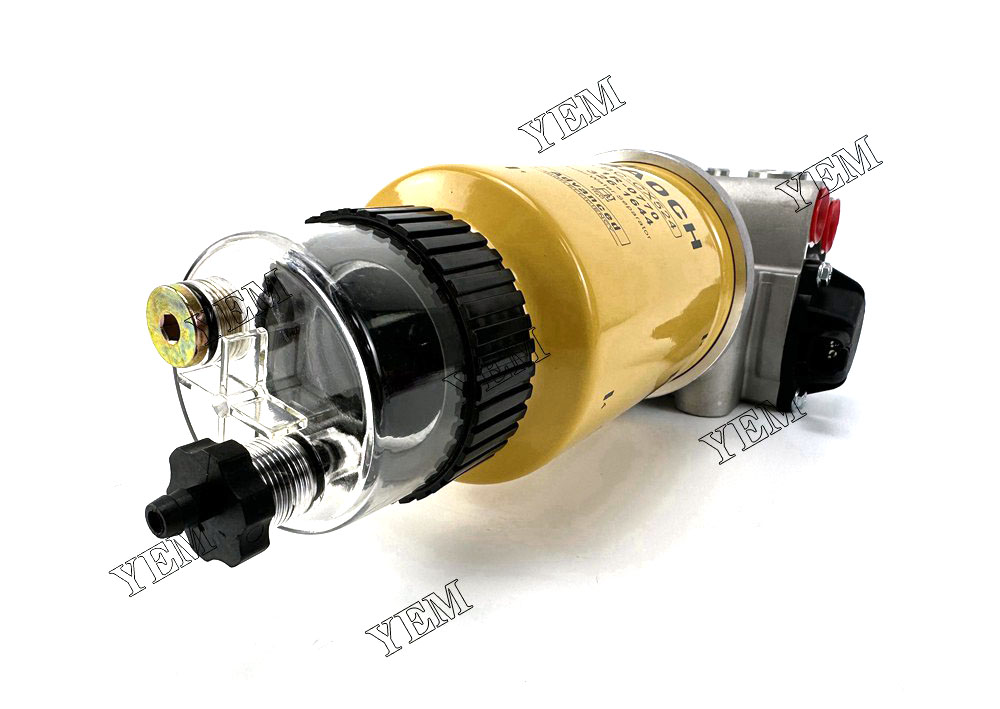
Development and future trends of engine oil-water separators
Engine oil-water separators are important devices used in various industries to separate and remove oil particles from water. They play a crucial role in maintaining environmental compliance and ensuring the efficient operation of equipment. Over the years, these separators have undergone significant development, and several future trends are emerging in this field.
- Advanced Filtration Technologies: Engine oil-water separators are incorporating advanced filtration technologies to enhance their efficiency and effectiveness. These technologies, such as membrane filtration, electrocoagulation, and coalescing filters, offer improved oil removal capabilities and reduce maintenance requirements.
- Automation and Remote Monitoring: The future of engine oil-water separators is moving towards automation and remote monitoring. Integrated control systems and sensors allow for real-time monitoring of separator performance, oil-water interface detection, and automated maintenance alerts. This improves operational efficiency and reduces the need for manual intervention.
- Compliance with Stringent Regulations: The development of engine oil-water separators is driven by increasing environmental regulations. To meet these stringent standards, separators are designed to achieve higher levels of oil removal efficiency. Manufacturers are continually innovating to ensure compliance with evolving regulations and to minimize environmental impact.
- Eco-friendly Solutions: There is a growing demand for eco-friendly solutions in various industries. Engine oil-water separators are being developed with a focus on reducing energy consumption, water usage, and the generation of waste. This includes utilizing energy-efficient pumps, incorporating water recycling systems, and optimizing separation processes.
- Integration with IoT and AI: The integration of engine oil-water separators with the Internet of Things (IoT) and artificial intelligence (AI) technologies is a future trend. This enables remote monitoring, predictive maintenance, and data-driven optimization. AI algorithms can analyze performance data to identify patterns, detect anomalies, and optimize separator operation for maximum efficiency.
Overall, the development and future trends of engine oil-water separators focus on improving efficiency, automation, environmental compliance, and sustainability. These advancements contribute to better performance, reduced operational costs, and minimized environmental impact in industries that rely on such separators.
Contact us
If you have any inquiries or requirements regarding excavator parts, our skilled and passionate team at YEM is here to assist you. We specialize in providing top-quality excavator accessories and comprehensive solutions tailored to meet your needs.
With years of experience in the industry, our team of engineers and technicians has a profound understanding of excavators, their working principles, and the functionalities of accessories. This allows us to offer accurate recommendations and professional advice.
We work closely with renowned excavator parts manufacturers and suppliers to ensure that the products we provide are of exceptional quality and reliability. Our expertise covers all types and brands of excavators, and we can help you with anything from replacing damaged accessories to upgrading your excavator’s function and performance.
In addition to supplying excavator accessories, we also offer services such as transportation, installation, repairs, and after-sales support. Customer satisfaction is our top priority, and we always strive to deliver outstanding service and the best solutions.
If you have any questions or if there’s anything we can assist you with, please don’t hesitate to get in touch. We are excited to provide you with high-quality excavator accessories and professional technical support.