Principle and working principle of engine diesel pump
The Engine Diesel Pump is a critical component in a gasoline or diesel engine that delivers fuel from the fuel tank to the injectors or injectors for combustion in the engine’s combustion chamber. Its principle and working principle are as follows:
- Principle:
The principle of a diesel pump is based on pressure transmission and fuel injection. Diesel fuel is compressed by a plunger or roller in the pump body, creating high-pressure fuel. High-pressure fuel enters the engine combustion chamber through the injection hole or nozzle, and is atomized, mixed and burned under high pressure and high temperature to generate power. - Working principle:
The working principle of a diesel pump is based on the synergy of several main components:
- Diesel Pump Body: Contains one or more plungers or rollers that work within the pump body to compress the fuel.
- Plunger/Roller: Connected to the drive shaft via a connecting rod, it reciprocates in the pump body to compress the fuel by building and reducing the volume of the chamber.
- Positioning/manipulating mechanism: Control the reciprocating motion of the plunger/roller through a connecting rod, camshaft or other driving device. These mechanisms adjust the displacement and fuel injection time of the diesel pump according to the working state and load requirements of the engine.
- Fuel inlet and outlet: through the oil inlet and return pipelines, the fuel is introduced from the fuel tank to the diesel pump, and then output from the pump body to the fuel injector or nozzle.
- Fuel Injector/Nozzle: The part connected to the diesel pump, which injects high-pressure fuel into the engine combustion chamber through the injection hole or nozzle.
During the working process, the plunger or roller of the diesel pump is controlled by the driving device and reciprocates when the throttle valve is opened. When the plunger/roller moves downward, the volume of the pump chamber increases, and the fuel is drawn into the pump body; when the plunger/roller moves upward, the volume of the pump chamber decreases, and the fuel is compressed to form high-pressure fuel. High-pressure fuel is then injected into the engine combustion chamber to complete the combustion process.
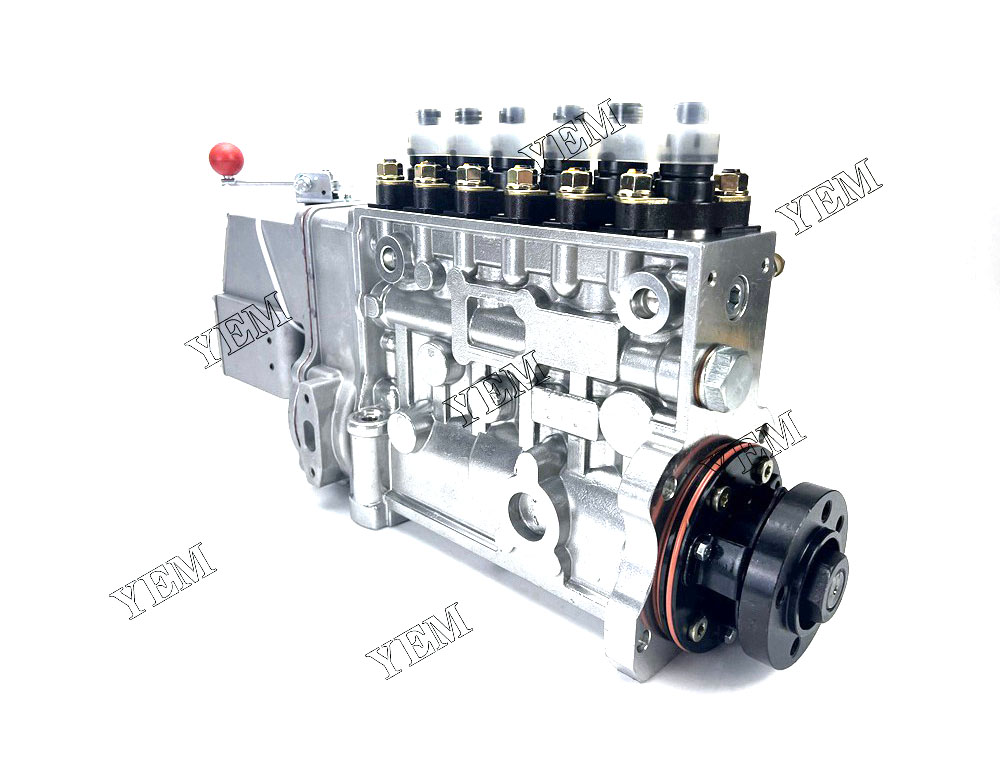
The working principle of the diesel pump is to ensure the accurate supply and injection of fuel by precisely controlling the position and speed of the plunger/roller, as well as the injection time and pressure of the injector/injector. This enables efficient combustion and power delivery, and minimizes fuel consumption and emissions.
Different types of diesel pumps
There are several different types of diesel pumps, some of the common ones are listed below:
- Atmospheric pump (Inline Pump): Inline pump is a mechanical diesel pump, suitable for diesel engines with smaller power. Its working principle is to drive the movement of the plunger through the camshaft in the diesel pump body, so as to realize the compression and supply of fuel.
- VE pump: VE (distributed electronic) pump is an electronically controlled diesel pump, often used in light duty diesel engines. It controls fuel supply and injection timing through solenoid valves, thereby achieving more accurate fuel control and higher combustion efficiency.
- Built-in injector (Pump-injector): The built-in injector is a device that combines a diesel pump and a fuel injector, and is often used in modern diesel engines. It integrates the functions of diesel pump and fuel injector, and can control the injection pressure and injection quantity of fuel more accurately.
- Common Rail system (Common Rail): The common rail system is a high-pressure electronically controlled diesel injection system that provides high-pressure fuel to all injectors through the common rail pipeline. It has higher fuel injection pressure and more accurate fuel control, which can achieve higher combustion efficiency and low emissions.
- Pressure pump (Unit Pump): The pressure pump is an advanced electronically controlled diesel pump system, which is widely used in heavy-duty diesel engines. It achieves higher precision fuel control and injection through the combination of high pressure pump and fuel injector.
These different types of diesel pumps are different in structure, working principle and application fields, but they are all designed to provide efficient fuel supply and precise fuel control for efficient combustion and power output. Selecting the proper diesel pump type depends on factors such as engine power requirements, emissions requirements, and economic considerations.
Structure and composition of diesel pump
The structure and composition of diesel pumps can vary according to different types of diesel pumps, but generally include the following basic components:
- Pump Body: The main outer casing of a diesel pump that houses and supports the internal components. It is usually made of cast iron, aluminum alloy or steel for high strength and corrosion resistance.
- Plunger/Roller: The moving part inside a diesel pump that compresses and delivers fuel. They can be of the plunger or roller type and produce compression through a reciprocating motion. Plungers are usually made of metallic materials with precision surfaces and seals.
- Camshaft/drive unit: used to control the reciprocating motion and working rhythm of the plunger/roller. Camshafts are usually made of steel and have a convex and concave shape that determines the trajectory of the plunger/roller. The drive means can be a linkage, gear or other mechanical transmission.
- Fuel inlet and fuel return port: The diesel pump introduces fuel from the fuel tank through the fuel inlet, and returns unnecessary fuel to the fuel tank through the fuel return port. These ports usually have fittings or connectors to connect with other components in the fuel system.
- Fuel injectors/nozzles: Diesel pumps are usually connected to fuel injectors or nozzles to inject compressed fuel into the engine combustion chamber. The structure and composition of the injector vary according to different types and technologies of diesel pumps, but generally include parts such as injection holes, nozzle bodies and control devices.
In addition, diesel pumps may also include some other auxiliary components, such as:
- Fuel filter: used to filter the impurities and pollutants in the fuel to protect the normal operation of the diesel pump and fuel injector.
- Regulating valve: used to regulate and control the fuel supply and injection pressure of the diesel pump.
- Electronic control unit (ECU): used to electronically control the working state and injection process of the diesel pump, and realize precise control of fuel supply and injection through sensors and actuators.
Please note that different types of diesel pumps and their structure and composition will be different, and the components mentioned here are generally common components, and the structure and composition of specific diesel pumps may vary depending on the manufacturer, model and application.
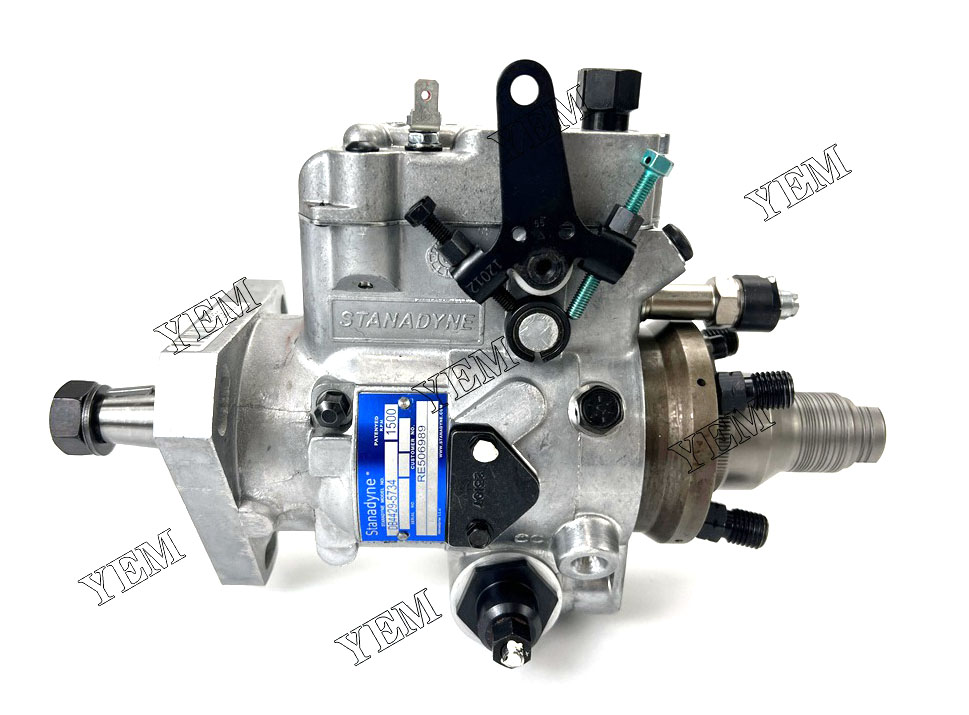
Diesel pump troubleshooting and maintenance
For diesel pump troubleshooting and maintenance, here are some suggestions and procedures:
Troubleshooting:
- Observe and listen: Carefully observe the appearance of the diesel pump and the surrounding environment, and check for signs of leakage, leakage or damage. At the same time, pay attention to listening to abnormal sounds, such as noisy, harsh or abnormal sounds.
- Check the fuel supply system: Check whether the fuel supply system is working normally, including checking whether the fuel filter is blocked, whether there is oil leakage in the fuel supply pipeline, etc.
- Check the power supply system: Check whether the battery power supply voltage is normal, and ensure that the power supply of the diesel pump’s electronic control unit (ECU) and solenoid valve is stable.
- Use fault diagnosis tools: Use appropriate fault diagnosis tools, such as fault code scanners, oscilloscopes, etc., to diagnose the electronic components of the diesel pump to obtain fault codes and parameter data.
- Seek professional help: For complex fault problems, it is recommended to seek the help of professional mechanics or diesel pump maintenance technicians, who have professional knowledge and equipment for more in-depth fault diagnosis.
Maintain:
- Regularly replace the fuel filter: Regularly replace the fuel filter to ensure the purity and fluidity of the fuel, so as to prevent particles and impurities from entering the diesel pump and affecting its normal operation.
- Clean fuel injectors/nozzles: Regularly clean fuel injectors or nozzles to prevent clogging and carbon deposits, as well as to ensure that their injection effects and injection angles are normal.
- Check and adjust the fuel pressure: Regularly check and adjust the fuel pressure of the diesel pump to ensure that it is within the parameters specified by the manufacturer.
- Regularly check and fasten bolts: Regularly check the bolts and fasteners of diesel pumps and accessories to ensure their safety and fastening.
- Regular maintenance: According to the manufacturer’s suggestion and maintenance manual, carry out routine maintenance of diesel pumps on a regular basis, including changing lubricating oil, checking transmission parts, checking shaft seals, etc.
- Keep clean and dry: keep the diesel pump clean and dry as a whole, and prevent moisture, dust and pollutants from entering the diesel pump.
The above suggestions are for reference only, and the specific maintenance and troubleshooting steps may vary according to the diesel pump type, model and manufacturer’s requirements. Always follow the manufacturer’s guidelines and recommendations, and seek professional repair support when needed.
Development Trend of Diesel Pumps Application Fields of Diesel Pumps
The development trend and application fields of diesel pumps are as follows:
- High pressure common rail system: High pressure common rail system is the mainstream trend of diesel pump technology at present. It adopts electronic control technology to provide higher pressure fuel supply through common rail pipeline to achieve more precise fuel injection and higher combustion efficiency. High-pressure common rail systems are widely used in various diesel engines, including cars, trucks, ships and construction machinery.
- Electronic control technology: The electronically controlled diesel pump can more accurately control the fuel injection time and pressure to meet the needs of different loads and working conditions. Electronic control technology also enables the diesel pump to be more closely integrated with the engine control system, providing more efficient fuel supply and injection control.
- Clean fuel and low emission: With the increasing awareness of environmental protection, the development trend of diesel pumps is to meet the needs of clean fuels, such as low-sulfur diesel, biodiesel and synthetic fuels. In addition, diesel pumps also need to meet stricter emission standards, and reduce emissions through advanced fuel injection technology and nitrogen oxide emission reduction devices.
- Multi-stage injection technology: One of the development trends of diesel pumps is multi-stage injection technology. By injecting fuel multiple times during the combustion process, more complete combustion and lower emissions are achieved. Multi-stage injection technology adopts advanced control algorithms and high-speed fuel injectors to provide more flexible and fine fuel control.
- Application fields: Diesel pumps are mainly used in the field of internal combustion engines, including automobiles, trucks, ships, agricultural and construction machinery, etc. With the development of electric vehicles and hybrid technology, the application field of diesel pumps may face certain challenges. However, in some special application scenarios, such as long-distance transportation, heavy transportation and high power requirements, diesel engines still have advantages.
It should be noted that the specific development trends and application areas of diesel pumps are affected by many factors, such as policies and regulations, technological innovation, market demand, etc. Therefore, the future development of diesel pumps still needs to pay close attention to the dynamic changes of related industries and technologies.
Diesel pump performance testing and optimization
Performance testing and optimization of diesel pumps can usually be performed through the following steps:
- Preparation before the test: Before performing the performance test, ensure that the diesel pump and related components and systems are in normal working condition, such as ensuring smooth fuel supply, normal electronic control unit (ECU), stable voltage supply, etc.
- Performance parameter test: perform performance parameter test on the diesel pump, including fuel injection pressure, injection quantity, injection time, etc. This can be done with specialized test equipment and tools such as high voltage test benches, fault code scanners, etc. At the same time, diesel engines and related sensors can be used for real-time monitoring and data collection.
- Analyze the test results: analyze and compare the performance of the diesel pump according to the parameters and data obtained from the test. Compare with the manufacturer’s specifications and standards to determine whether the expected performance requirements are met.
- Optimization measures: According to the test results and analysis, determine the optimization measures for the performance of the diesel pump. This may involve the adjustment of the fuel injection system, the replacement of parts, the optimization of electronic control parameters, etc. Depending on the situation, several iterations and adjustments may be required until an optimized result is achieved.
- Validation and retest: After optimization, the diesel pump is validated and retested to ensure improved and stable performance. Repeat the test steps to compare the new test results with the previous data to confirm whether the optimization has achieved the expected results.
- Regular maintenance and monitoring: In order to maintain the good performance of diesel pumps, regular maintenance and monitoring are crucial. This includes changing filters regularly, checking sensors and connecting lines, keeping injectors clean, and more. Regular maintenance and monitoring can help identify potential problems and take timely action.
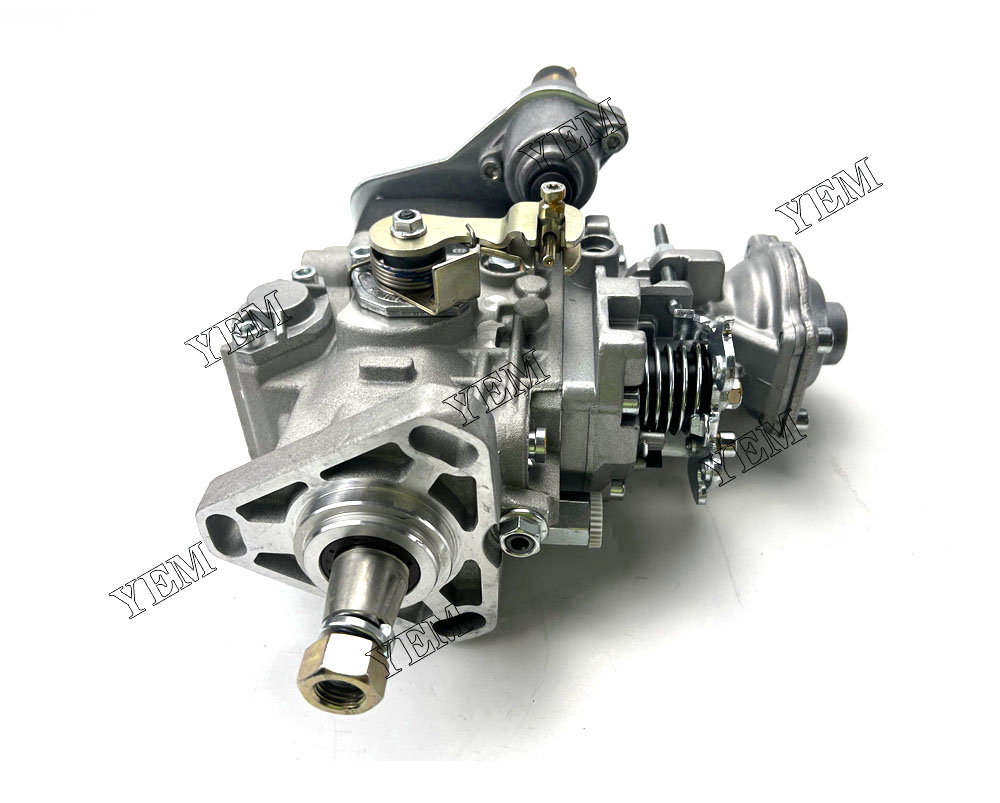
In short, the performance testing and optimization of diesel pumps need to rely on professional equipment and technology, and at the same time combine the manufacturer’s specifications and standards for evaluation. Through comprehensive testing of diesel pump performance, data analysis and implementation of optimization measures, the performance, combustion efficiency and reliability of diesel pumps can be improved to meet the needs of various engine applications.
Research progress of diesel pump technology
Diesel pump technology is constantly being researched and developed, the following are some current research developments:
- Further optimization of high pressure common rail system: High pressure common rail system is one of the main development directions of diesel pump technology. Researchers are working to increase the working pressure and precision of the common rail system to achieve more precise fuel injection and higher combustion efficiency.
- Further research on multi-stage injection technology: multi-stage injection technology can achieve more refined and flexible fuel injection control, thereby further optimizing the combustion process and emission performance. Researchers are working on aspects such as injection strategies, injector design and control algorithms to achieve greater injection precision and control.
- Application of solenoid valve technology: Traditional diesel pumps use mechanical critical injectors to control fuel injection timing, but researchers are working hard to develop diesel pumps that use solenoid valves. The solenoid valve has faster response speed and more flexible control ability, which can achieve higher fuel injection accuracy and more reliable performance.
- Intelligence and electronic control: With the advancement of intelligent technology, the electronic control and monitoring functions of diesel pumps are continuously enhanced. Researchers are developing more advanced electronic control units (ECUs), sensors and algorithms to enable more precise control of fuel delivery and injection to improve combustion efficiency and emissions performance.
- Research on the adaptability of clean fuels: With the improvement of environmental protection requirements, diesel pumps need to adapt to more types of clean fuels, such as low-sulfur diesel, biodiesel and synthetic fuels. Researchers are studying the injection and combustion characteristics of different fuels in diesel pumps to optimize fuel adaptation and performance.
These research advances aim to improve the efficiency, reliability and environmental performance of diesel pumps. Through continuous research and innovation, diesel pump technology will further meet the needs of different application fields, and at the same time provide support for the development of future fuel supply systems.
Experience sharing and case analysis
The following are some experience sharing and case studies of diesel pump failures:
- Case study: The fuel injection volume of the diesel pump is abnormal
Description: The diesel engine of a truck was underpowered. Inspection found that the amount of diesel fuel injected was abnormal, and the injectors showed no obvious signs of clogging or failure.
Solution: After further inspection and testing, it was found that the fuel inlet pressure of the diesel pump was too low, resulting in insufficient fuel injection. By replacing the fuel filter and checking the connection of the fuel supply line, the problem of abnormal fuel injection quantity of the diesel pump was successfully solved. - Experience sharing: regular maintenance and inspection of diesel filters
Lesson learned: Changing the diesel filter regularly is the key to keeping the diesel pump working properly. The blockage of the filter or the accumulation of impurities will lead to insufficient fuel supply and affect the performance and combustion efficiency of the diesel pump.
Measures: According to the manufacturer’s recommendations, replace the filter regularly, check the status of the filter during the replacement process, and clean or replace the clogged filter element. In addition, keep the fuel supply system clean to prevent impurities and moisture from entering the diesel pump. - Experience sharing: regular inspection and maintenance of injectors
Experience: The fuel injector is one of the key components of the diesel pump and needs regular inspection and maintenance. A clogged or damaged injector can result in uneven or incomplete fuel injection, affecting engine performance and combustion efficiency.
Measures: Regularly check and clean the fuel injector, especially the hole and injection angle of the fuel injector. If it is found to be clogged or damaged, clean or replace it in time. At the same time, maintain the quality of fuel and avoid using low-quality fuel to reduce carbon deposition and damage to the injector.
Please note that the above cases and experiences are for reference only. In actual application, the specific fault diagnosis and maintenance measures may vary according to the type, model and manufacturer’s requirements of the diesel pump. Always follow the manufacturer’s guidelines and recommendations, and seek professional repair support when needed.
The future development direction of diesel pumps
The future development direction of diesel pumps may include the following aspects:
- Electrification and hybrid technology: As electric vehicles and hybrid technology develop, diesel pumps may need to adapt to new powertrain requirements. The development of diesel-electric hybrid systems may require more efficient and compact diesel pump designs to accommodate the power output and energy recovery of electric motors.
- Clean fuels and low emissions: Diesel pumps need to accommodate more types of clean fuels, such as low sulfur diesel, biodiesel and synthetic fuels. At the same time, diesel pumps still need to meet stricter emission standards, and reduce emissions through advanced fuel injection technology and nitrogen oxide reduction devices.
- Advanced injection control technology: With the continuous development of fuel injector technology, diesel pumps can achieve higher precision and more levels of fuel injection control. There may be more types of fuel injection strategies and modes to adapt to combustion requirements under different operating conditions and improve fuel economy and emission performance.
- Intelligence and electronic control: The intelligence and electronic control technology of diesel pumps will be further improved. More advanced electronic control units (ECUs), sensors and algorithms can achieve more precise fuel injection and combustion control, improving fuel efficiency and power performance.
- Lightweight and energy-saving: In the future, diesel pumps may pursue lighter and energy-saving designs to reduce the weight and energy consumption of the system. More advanced materials and manufacturing processes may be used to optimize the structure and components of diesel pumps to improve overall efficiency.
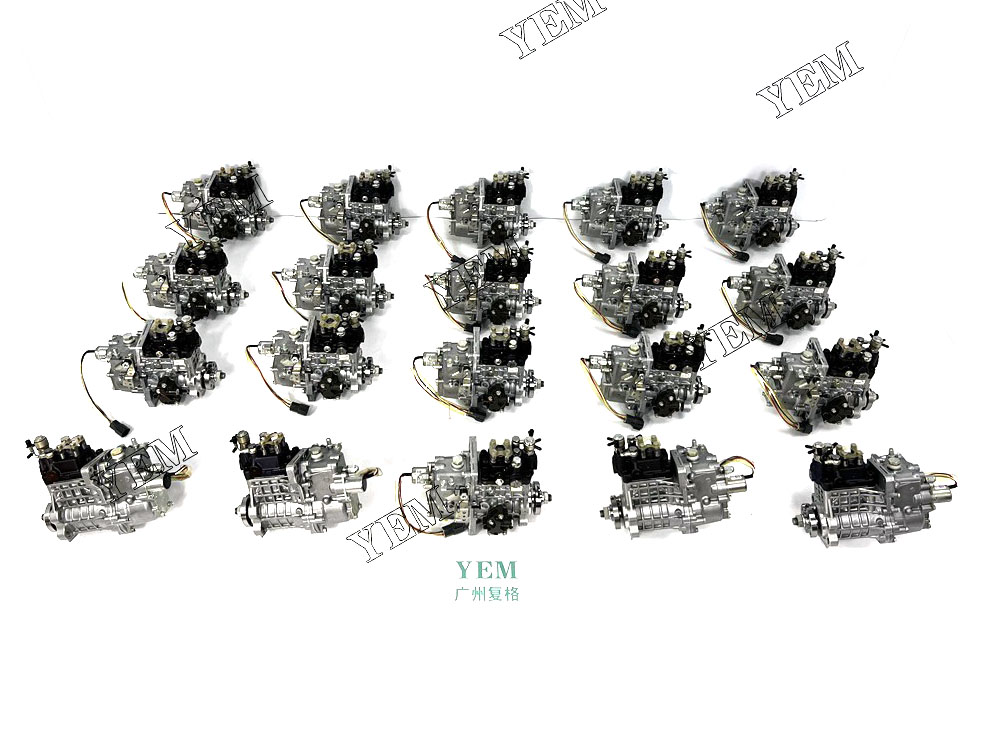
It should be noted that the future development direction of diesel pumps is affected by many factors, such as technological progress, environmental protection regulations, market demand and economic conditions. At the same time, with the rapid development of new energy technologies, diesel pumps may face some challenges, requiring continuous innovation and adaptation in terms of cleaning performance, energy efficiency and environmental protection. Therefore, the future development direction of diesel pumps has certain uncertainties, and it is necessary to pay close attention to the dynamic changes of related technologies and industries.
Contact us
Thank you for your interest in YEM Excavator Parts Team! We are a professional team specializing in excavator accessories. We are dedicated to providing our customers with high-quality and reliable solutions for all their excavator parts needs.
With years of industry experience and extensive technical knowledge, our team is capable of accurately identifying and resolving various excavator parts issues. Whether you require replacement of a damaged part, an upgrade to an existing accessory, or a specific accessory tailored to your requirements, we are here to provide professional advice and assistance.
As a responsible excavator parts supplier, we collaborate with reputable manufacturers to ensure the parts we offer are of excellent quality and reliable performance. Our extensive range of excavator accessories includes standard options, and we can also accommodate customizations based on your specific needs.
We understand the importance of timely response and efficient supply in your excavator operations. Therefore, we are committed to delivering fast and efficient parts supply services. No matter where you are located, we can ensure timely accessibility and accurate delivery of the accessories you need.
If you are interested in our services or have any requirements for excavator accessories, please do not hesitate to contact us. Our dedicated team is ready to provide you with the best service and support in resolving any issues you may encounter. We look forward to working with you!