How the oil cooler works
The working principle of the oil cooler is to use heat exchange to reduce the temperature of the oil through the heat transfer between the cooling medium (usually coolant or air) and the oil. The following is the basic working process of the oil cooler:
- Cooling medium enters the cooler: The cooling medium (coolant or air) enters the oil cooler through the pipe.
- Oil enters the cooler: Hot oil exits the engine and enters the oil cooler. The oil flows through the cooling ducts inside the cooler.
- Heat transfer process: heat exchange occurs between the cooling medium and the oil. The heat transfer process can be performed by direct contact and heat radiation.
- In the case of a coolant cooler: The coolant flows through the cooling pipes, comes into contact with the oil, absorbs heat from the oil, and at the same time the coolant itself is heated.
- In the case of an air cooler: The air passes through the cooler and cools the oil by absorbing heat from the oil by coming into contact with cooling fins or cooling cores.
- Release of cooling medium: During the heat transfer process, the cooling medium absorbs the heat of the oil, and the temperature rises. The hot cooling medium then exits the cooler through pipes.
- Return the cooled engine oil to the engine: the cooled engine oil re-enters the engine and continues to be recycled to keep the engine’s operating temperature within a reasonable range.
The working principle of the oil cooler is simple and clear. The heat is transferred from the oil to the cooling medium through heat exchange to ensure that the temperature of the engine oil is controlled, thereby improving the stability and life of the engine. The specific working principle may vary according to different oil cooler designs and application scenarios.
Structure and composition of oil cooler
An oil cooler usually consists of the following main parts:
- Shell: The outer structure of the oil cooler, usually made of metal (such as aluminum alloy) or plastic material. The casing helps protect the cooling fins or core inside the cooler and provides channels for the cooling medium to flow.
- Cooling fins or cooling cores: Cooling fins or cooling cores are the most critical parts inside the oil cooler, usually made of metals (such as copper, aluminum or alloys), which have excellent thermal conductivity. Cooling fins or cooling cores have a sheet or honeycomb structure that provides a large surface area for heat exchange.
- Cooling medium channels: There are channels inside the oil cooler to guide the cooling medium (coolant or air) to flow through the cooling fins or cooling cores to exchange heat with the oil. These passages are usually elongated tubes or fine channel structures that maximize the contact area between the cooling medium and the oil.
- Import and export pipes: the connection channel between the oil cooler and the engine, which is used to guide the hot oil from the engine into the cooler and return the cooled oil to the engine. Typically, the oil cooler will have inlet and outlet connections that connect the oil circulation lines between the engine and the cooler.
- Mounting bracket: The oil cooler usually needs to be fixed on the engine or other appropriate positions through brackets. Mounting brackets can vary for different excavator models and installation conditions.
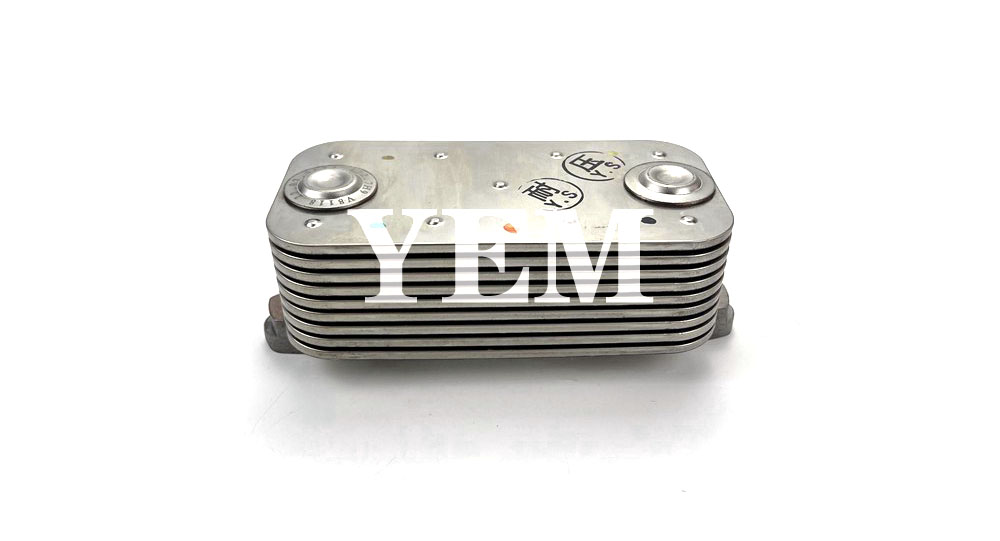
In addition to the above main components, the oil cooler may also include auxiliary devices such as cooling medium inlet and outlet valves, temperature sensors, and pressure sensors, which are used to control and monitor the operating status of the oil cooler and the temperature of the oil.
Please note that the specific oil cooler structure and composition can vary according to different excavator brands, models and application needs. The above is an overview of the basic components, and the actual structure of the oil cooler can be designed and constructed according to the actual situation.
Oil Cooler Operating Conditions and Requirements
The working conditions and needs of an excavator engine oil cooler depend on several factors, including the external environment, engine load, operating hours, etc. Below are some common working conditions and requirements:
- External ambient temperature: The external ambient temperature has an effect on the operation of the oil cooler. In a high temperature environment, the temperature of the engine oil will increase, requiring more powerful cooling capacity to maintain the normal operating temperature of the engine oil.
- Engine load: The engine load will affect the temperature of the engine oil. Under high load and long-term operation, the temperature of the oil may increase, requiring more effective cooling to control the oil temperature.
- Cooling medium flow and temperature: The flow and temperature of the cooling medium (coolant or air) are critical to the performance of the oil cooler. Sufficient cooling medium flow and proper temperature difference can effectively take away the heat of the oil.
- The cleanliness of the cooling medium: The cleanliness of the cooling medium has an impact on the working effect of the cooler. If there are impurities, deposits or dirt in the cooling medium, it may cause the cooler to block or reduce the heat transfer efficiency.
- Cooler design and performance: The design and performance of the oil cooler is also a key aspect of operating conditions and requirements. An effective cooler should have sufficient heat dissipation area, good thermal conductivity and reasonable fluid dynamic characteristics to ensure sufficient cooling capacity.
- Maintenance and maintenance: The regular maintenance and maintenance of the oil cooler is also the key to ensure its normal operation. Cleaning the surface and interior of the cooler, inspecting and replacing damaged seals, ensuring that the coolant is properly used and replaced are all important measures to keep the oil cooler working well.
To sum up, the working conditions and requirements of the oil cooler are multifaceted, and factors such as the external environment, engine load, cooling medium, cooler design and maintenance need to be considered to ensure that the oil cooler can effectively reduce the temperature of the oil and Maintain the normal operating temperature of the engine.
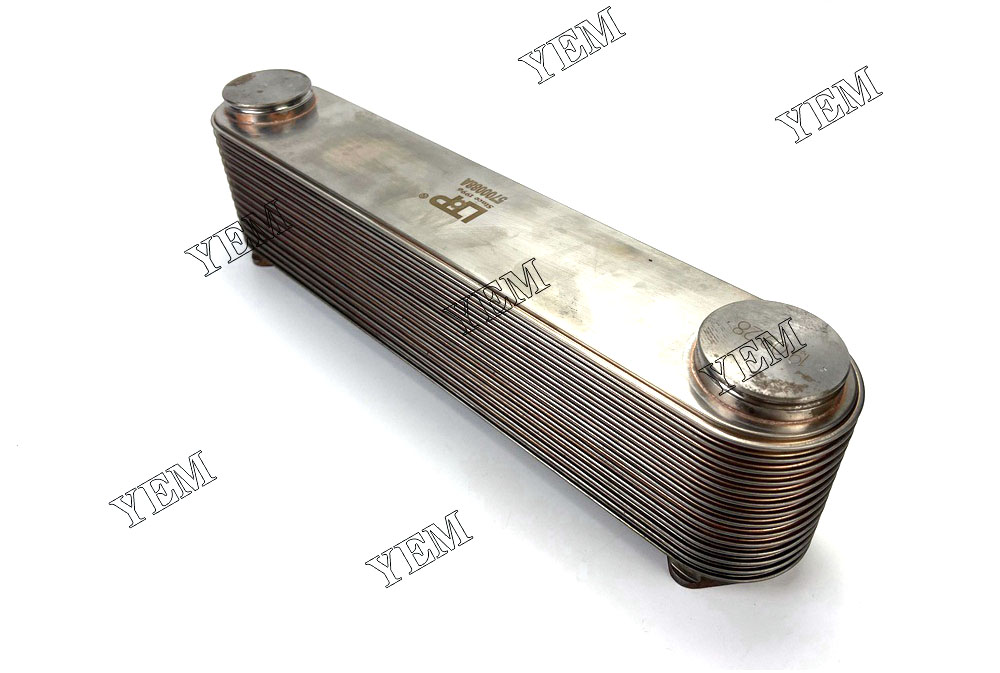
Oil cooler maintenance and care
Maintaining and servicing your oil cooler is critical to ensuring it works properly and lasts longer. Here are some common oil cooler maintenance and maintenance recommendations:
- Regularly clean the surface of the cooler: Regularly clean the outer surface of the oil cooler to remove dust, impurities and oil stains, etc. You can use a soft brush or a high-pressure water gun to gently clean the surface of the cooler, and be careful not to damage the cooling fins or cooling core.
- Maintenance of coolant: If the oil cooler uses coolant as the cooling medium, the level and quality of the coolant should be checked regularly. Replenish and replace the coolant in time to ensure that it achieves the set cooling performance and anti-corrosion function.
- Check the cooling medium channel: Regularly check the cooling medium channel inside the oil cooler to ensure that the channel is unobstructed. If blockage or impurities are found, the cooler should be cleaned or replaced in time.
- Check Seals and Piping Connections: Periodically check the seals and piping connections of the oil cooler to make sure they are intact and leak-free. If it is aging, damaged or leaking, it should be replaced in time.
- Check the temperature and pressure of the cooler: regularly monitor the temperature and pressure of the oil cooler to ensure its normal operation. If you notice an abnormal increase in temperature or pressure, troubleshooting and repair may be required.
- Pay attention to the use conditions and environment: When using the oil cooler, care should be taken to avoid long-term operation in harsh working environments, such as mud, sand, high temperature, etc. Reasonable use conditions and environment will help to prolong the service life of the oil cooler.
- Perform maintenance according to the manufacturer’s recommendations: perform regular maintenance and maintenance according to the manufacturer’s recommendations and instructions of the oil cooler, including replacing the coolant, cleaning the cooler, checking and adjusting the working parameters of the cooler, etc.
Please note that specific maintenance and maintenance measures may vary with different oil cooler models, brands and usage conditions. Following the manufacturer’s recommendations is the best way to ensure proper function and prolong the life of your oil cooler.
Common faults and solutions
The oil cooler may encounter some common faults during use. Here are some common faults and their solutions:
- Coolant leaks: Coolant leaks may be caused by aging or damaged seals. The solution is to check the seals and replace them in time. At the same time, you should also check whether the connection of the coolant pipe is tight to ensure that it is not loose or loose.
- Blockage of cooling medium channels: After prolonged use, the cooling medium channels may be blocked by impurities, sediment or dirt. The solution is to regularly clean the internal passages of the cooler, use appropriate cleaning agents or tools for cleaning, and ensure that the passages are unblocked.
- Damaged cooling fins or cooling cores: Damage to cooling fins or cooling cores may result in reduced heat dissipation. The solution is to check the condition of the cooling fins or cooling cores, if any damage or blockage is found, replace the cooling fins or cooling cores with new ones.
- Abnormal rise in temperature: If the temperature of the oil cooler rises abnormally, it may be caused by insufficient cooling medium flow, cooler blockage or cooling medium quality problems. Solutions include checking the cooling medium flow and temperature, cleaning the cooler, and ensuring that the cooling medium is of the required quality.
- Abnormal increase in pressure: If the pressure of the oil cooler increases abnormally, it may be caused by the blockage of the cooling medium passage or the overheating of the coolant. The solution includes checking the cooling medium channel to ensure that the channel is unobstructed, and at the same time checking the quality of the coolant and the heat dissipation effect of the cooler.
- Failures caused by improper maintenance: If the oil cooler is not properly maintained and maintained, it may cause various failures. The solution is to carry out regular maintenance and maintenance, including cleaning the cooler, replacing the cooling medium, checking and adjusting the working parameters of the cooler, etc.
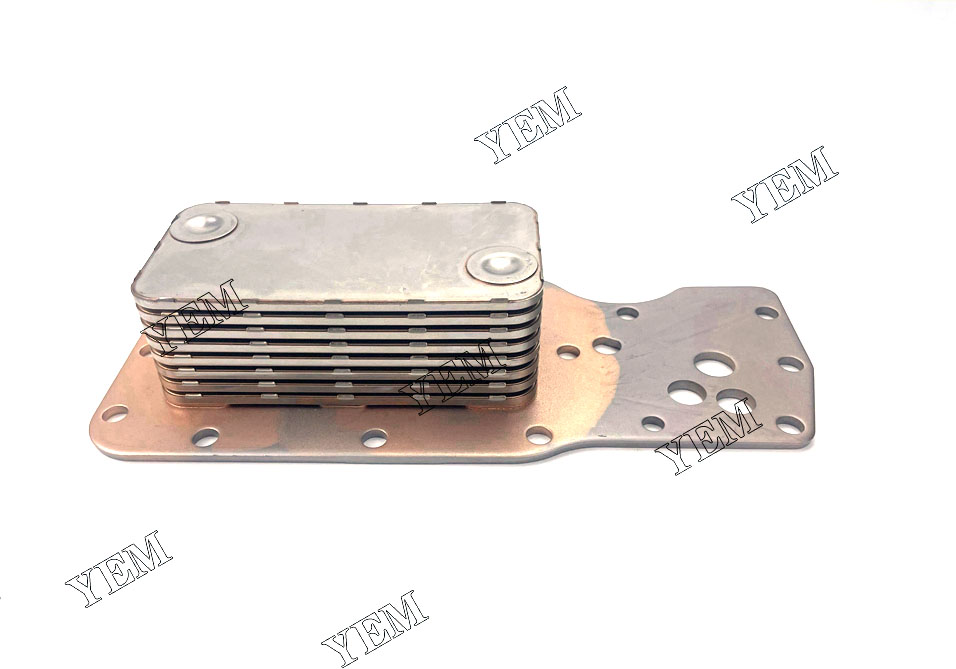
For more serious or complicated faults, it is recommended to seek help from professional technicians for fault diagnosis and repair. At the same time, according to the specific model of the oil cooler and the manufacturer’s recommendations, regular maintenance is an important measure to prevent failures.
Optimization and improvement of oil cooler
In order to optimize and improve the performance and effect of the oil cooler, the optimization and improvement of the following aspects can be considered:
- Increased heat dissipation area: increasing the heat dissipation area of the oil cooler can improve the cooling capacity of the cooler. This can be achieved by increasing the number of cooling fins or cooling cores, increasing the number of fins, or increasing the size of the cooler.
- Improvement of thermal conductivity: choose materials with good thermal conductivity to manufacture coolers, such as copper alloy or aluminum alloy with high thermal conductivity. In addition, changing the structural design of the cooler to increase the contact area for heat transfer can also improve thermal conductivity.
- Improved fluid dynamics: Improving the flow performance of the cooling medium inside the cooler can improve the cooling effect. The fluid dynamics can be improved by optimizing the design of the cooling medium channel, increasing the flow velocity of the fluid, or applying an airflow guiding device.
- Temperature and pressure control: add a temperature sensor and a pressure sensor to monitor the temperature and pressure changes of the oil cooler in real time, so as to adjust the flow and temperature of the cooling medium in time to ensure that the oil cooler operates within the set working range.
- Improvement of corrosion resistance of materials: Select materials with corrosion resistance properties to reduce corrosion and damage of oil coolers in harsh environments. The durability of the cooler can be improved by using corrosion-resistant alloys, coatings or anti-corrosion treatments.
- System optimization: Consider the synergy between the oil cooler and the entire cooling system, such as optimizing the design and matching of other components such as the engine radiator, oil pump, and cooling fan to achieve more effective heat management.
- Simulation and simulation analysis: Using simulation and simulation tools such as computational fluid dynamics (CFD) and heat transfer analysis to simulate and optimize the performance of the oil cooler can help predict and improve the cooler’s heat transfer and fluid dynamics characteristics.
These optimization and improvement methods can be tuned and applied according to specific application requirements and constraints. It should be noted that when improving the performance of the oil cooler, the overall working conditions and requirements of the system should be fully considered to ensure that all improvement measures can be implemented in a feasible and economical manner.
Typical application cases and market development trends
Oil coolers are widely used in various automobiles and mechanical equipment. The following are several typical application cases:
- Automotive field: Oil coolers are widely used in high-performance cars and racing cars. These vehicles usually work under high load and high temperature environment, the oil cooler can effectively control the temperature of the oil, protect the engine and improve the performance.
- Construction machinery: Construction machinery such as excavators, loaders, and trucks often require long-term high-intensity work. The oil cooler can effectively cool the engine oil, maintain the normal operating temperature of the engine, and extend the service life of mechanical equipment.
- Generator set: Large-scale generator sets usually have the characteristics of high power and long-term operation. The oil cooler can help control the temperature of the engine oil inside the generator set to ensure the stable operation and performance of the generator set.
- Industrial equipment and machinery: In addition to automobiles and generator sets, oil coolers are also widely used in various other industrial equipment and machinery, such as compressors, centrifuges, smelting equipment, etc.
In terms of market development trends, with the continuous development and upgrading of automobiles and mechanical equipment, the oil cooler market presents the following trends:
- High efficiency and energy saving: With the concern of energy and environment, the performance requirements of oil coolers are getting higher and higher. Future oil coolers will pay more attention to efficient heat transfer and low energy consumption to provide better cooling effect.
- Lightweight design: As the overall weight requirements of automobiles and mechanical equipment are getting higher and higher, the lightweight design of oil coolers has become a development trend. Reduce the weight of the oil cooler and improve overall efficiency through the use of lightweight materials and an optimized design.
- Intelligent control: With the development of information technology, the future oil cooler may adopt intelligent control system. Through sensors and data analysis technology, the real-time monitoring and intelligent adjustment of the working status of the oil cooler can be realized, and the cooling effect and energy efficiency can be improved.
- Application of new materials: Future oil coolers may use new materials, such as nano-materials, high thermal conductivity materials, etc., to improve heat dissipation and corrosion resistance.
- Customized and modular design: With the diversification of application scenarios, oil coolers increasingly need to meet the specific needs of different customers. Customized and modular design will become a major development trend in the oil cooler market to meet various application environments and requirements.
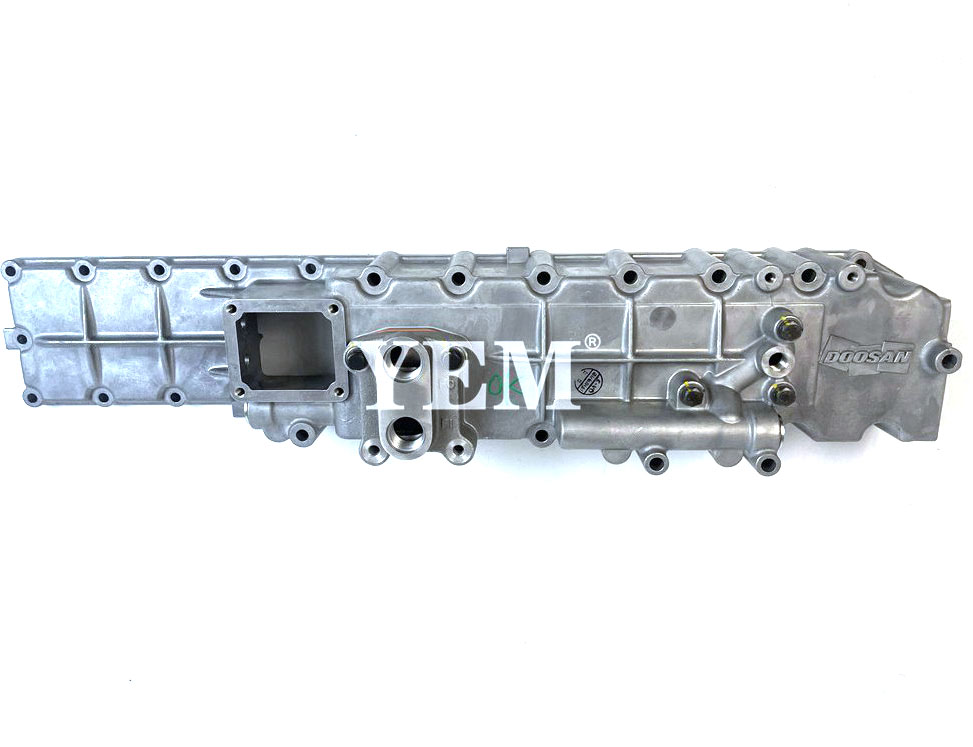
Generally speaking, the oil cooler market will continue to develop in the direction of high efficiency, light weight, intelligence and personalization to meet the ever-changing needs and requirements of automobiles and mechanical equipment.
Contact us
YEM Professional Excavator Parts Team is a professional and experienced team specialized in supplying high quality excavator parts. With our extensive knowledge and expertise in this field, we offer a comprehensive range of parts and components to meet the diverse needs of our customers.
Whether you need replacement parts for hydraulic systems, engine components, chassis components or other excavator components, the YEM team can support you from all angles. We source our products from trusted manufacturers and ensure that each component meets the highest standards of quality and durability.
What sets us apart is our commitment to exceptional customer service. We understand the importance of timely support and strive to respond quickly to inquiries and requests. Our knowledgeable staff is on hand to help customers identify the correct parts for their particular excavator model and provide installation and maintenance instructions.
To get in touch with the YEM Specialized Excavator Parts team, you can get in touch via our website, email or phone. We are committed to building long-term relationships with our customers and are passionate about assisting with your excavator parts needs.