The definition, function, type, etc. of engine fan blades.
The engine fan blade refers to the blade device located in the fan part of the engine, and its function is to generate air flow through rotation to provide cooling and increase engine efficiency.
Engine fan blades are usually divided into the following types:
- Steel aluminum blade: Made of steel and aluminum alloy, it has high strength and durability. This blade is suitable for high temperature environment and can provide a large air flow.
- Composite material blades: made of composite materials such as carbon fiber or glass fiber. The blades are lightweight, strong and resistant to oxidation, reducing engine load and improving fuel efficiency.
- Plate blades: blades formed by bending metal plates, suitable for low pressure and low temperature environments, such as auxiliary engine fans.
- Bucket blades: with curved blades, forming a cylindrical shape, which can increase the pressure and efficiency of the airflow.
- Blade pitch change mechanism: some fans with high bypass ratio use blades with a pitch change mechanism, and the distance of the blades can be adjusted according to needs to provide different efficiencies and thrusts.
These types of fan blades can be selected and applied according to engine type, use environment and design requirements.
Structure and materials of engine fan blades
The engine fan blades are an important part of the engine, which is responsible for compressing and pushing air into the combustion chamber to generate power.
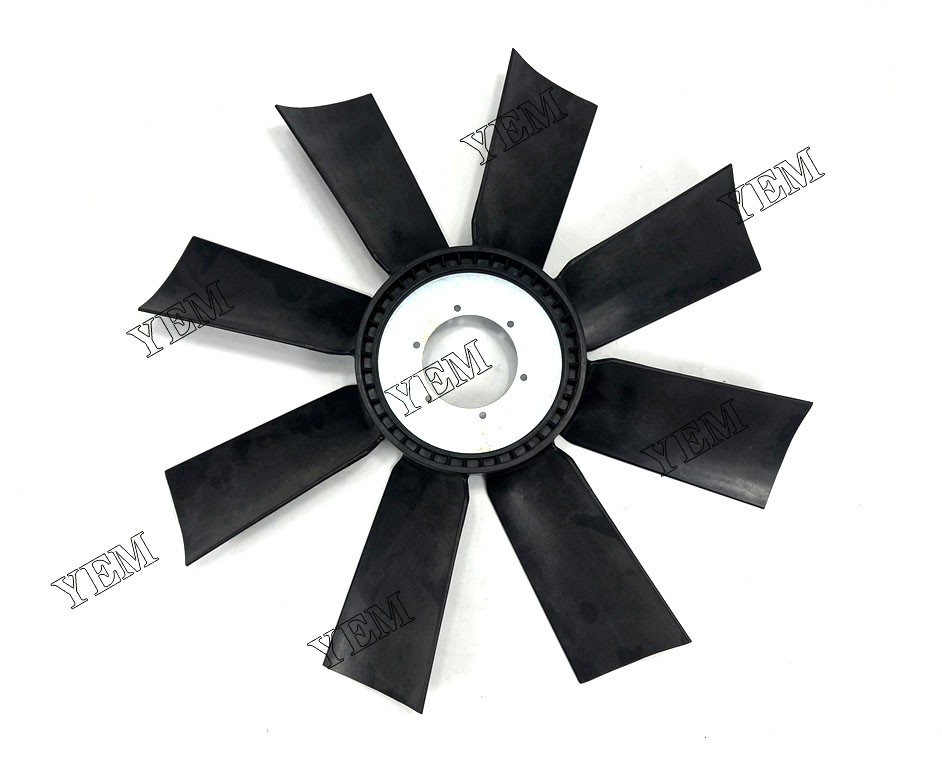
The structure of the engine fan blade is usually divided into two parts: the blade and the root.
- Blades: The blades of the engine fan blades are usually curved to improve the compression effect of the airflow. The shape and number of blades can affect the efficiency and noise of the fan. Generally speaking, the more fan blades, the better the airflow compression effect, but it will also increase wind resistance and noise. Modern engines typically use 3 to 6 blade designs. Blades are usually made of metal materials, such as titanium alloys, aluminum alloys, and the like.
- Root: The root of the engine fan blade is attached to the fan disc, usually by a bolt or similar attachment. The roots need to have a good seal to avoid airflow leaks. The roots are usually made of metal materials to ensure sufficient strength and durability.
The material selection of engine fan blades mainly considers the following factors:
- Strength: Engine fan blades need to be able to withstand high-speed rotation and wind pressure, so materials with sufficient strength need to be selected.
- Corrosion resistance: The fan blades of the engine are in a high-temperature, high-speed rotating environment, and are prone to oxidation and corrosion. Therefore, the material needs to have good corrosion resistance.
- Lightweight: The quality of fan blades is directly related to the weight and fuel efficiency of the entire engine. Therefore, the material needs to have sufficient lightweight properties.
Commonly used engine fan blade materials include:
- Titanium alloy: Titanium alloy has the characteristics of high strength, low density, and good corrosion resistance, and is often used to manufacture fan blades for high-performance engines.
- Aluminum alloy: Aluminum alloy has the advantages of high strength and light weight, and is easy to process and repair, so it is also a commonly used material for engine fan blades.
- Composite materials: Composite materials are composed of fiber reinforced materials (such as carbon fibers) and polymer matrix, which have high strength, light weight and corrosion resistance. In recent years, composite materials have become more and more widely used in the field of aerospace, and are gradually used in the manufacture of engine fan blades.
In short, the structure and material selection of the engine fan blade should be determined according to the requirements and performance requirements of the fan to ensure that it can withstand high-speed rotation and pressure, and has good corrosion resistance and lightweight characteristics.
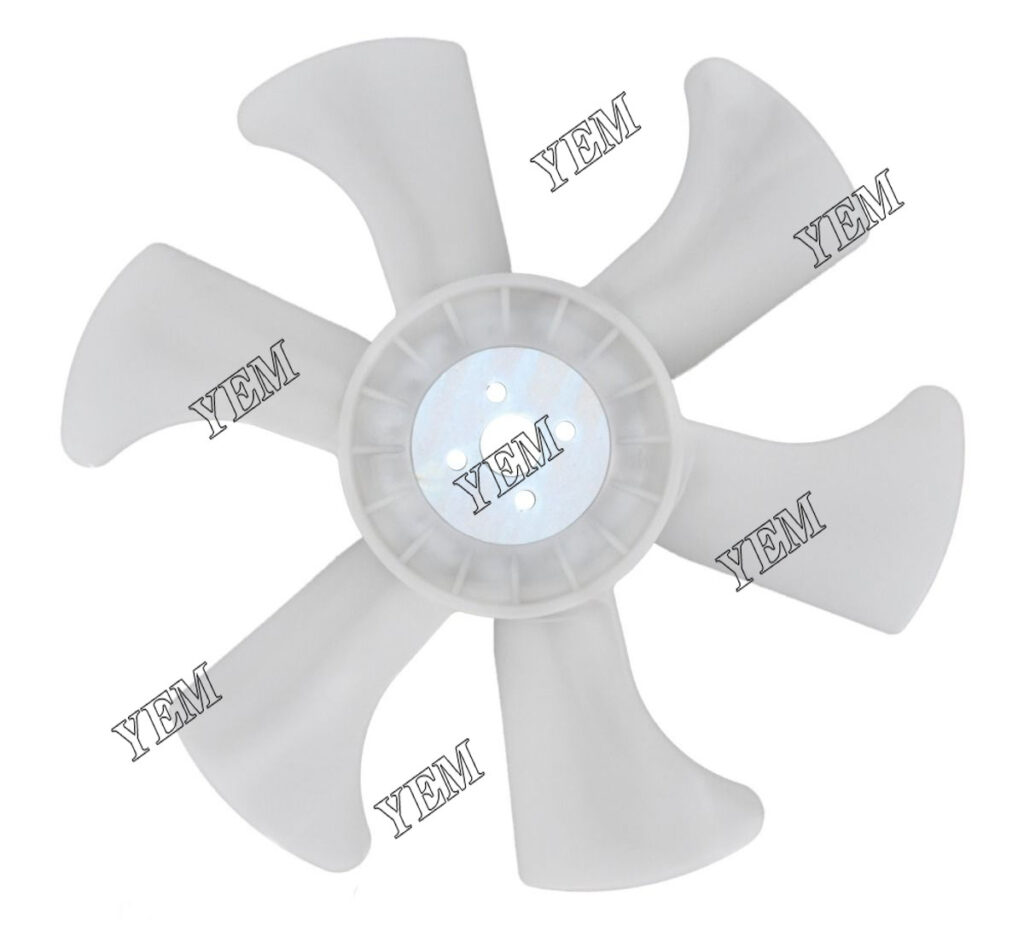
Manufacturing process of engine fan blades
The manufacturing process of engine fan blades usually includes the following steps:
- Material selection: Usually high-strength titanium alloy is used to ensure that the blade has sufficient strength and light-weight ratio.
- Cutting: First, according to the design requirements, the titanium alloy plate is cut into sheets of appropriate size.
- Sheet metal forming: Using sheet metal stamping technology, the cut sheet is pressed in the mold to make it the initial shape of the fan blade.
- Airfoil trimming: Use mechanical polishing or chemical polishing to trim the surface of the fan blades to ensure their shape and surface smoothness.
- Heat treatment: Through the heat treatment process, the strength and hardness of the fan blades are improved, and the internal stress is eliminated.
- Muffle grinding: using grinding technology to process and trim fan blades with precise dimensions.
- Balance: The fan blades are balanced and corrected by a dynamic balancing machine to ensure that the fan rotates smoothly and avoids vibration and noise.
- Surface treatment: processes such as anodizing, electroplating or coating can be carried out to improve the corrosion resistance and surface aesthetics of the fan blades.
- Assembly: Assemble the manufactured fan blades with other components (such as shafts, fan casings, etc.) to form a complete engine fan.
Troubleshooting and maintenance of engine fan blades
Failure of the engine fan blades can cause the engine to overheat or reduce performance. Here are some possible failure causes and solutions:
- Damaged or broken fan blades: The fan blades may be cracked or broken after being impacted by external forces or after being used for a long time. The solution is to replace the damaged fan blades.
- Fan blades falling off: Loose or falling fan blade bolts may cause the fan blades to separate from the rotor. The solution is to check the bolts and tighten them.
- Foreign objects on the fan blades: During flight, debris or foreign objects may enter the fan blades, causing the fan blades to become unbalanced or clogged. The solution is to remove foreign objects and perform balance correction.
- Carbon deposition on the fan blades: After long-term use, the fan blades of the engine may accumulate carbon, resulting in rough surface of the blades and reducing air flow efficiency. The solution is to clean the fan blades and perform regular maintenance.
- Fan blade drive failure: The transmission system driving the fan blade may be faulty, such as a broken connecting rod or worn transmission gear. The solution is to check the transmission parts and make necessary repairs or replacements.
- The cooling air passage of the fan blade is blocked: Dust, grease or other substances in the surrounding environment may block the cooling air passage of the fan blade, resulting in a decrease in the cooling effect of the fan blade. The solution is to clean the cooling air passages and ensure air circulation.
No matter what kind of failure, timely repair and regular maintenance are the key to ensure the normal operation of the engine fan blades and prolong their service life. It is important to ensure that fault repairs are performed by experienced technicians.
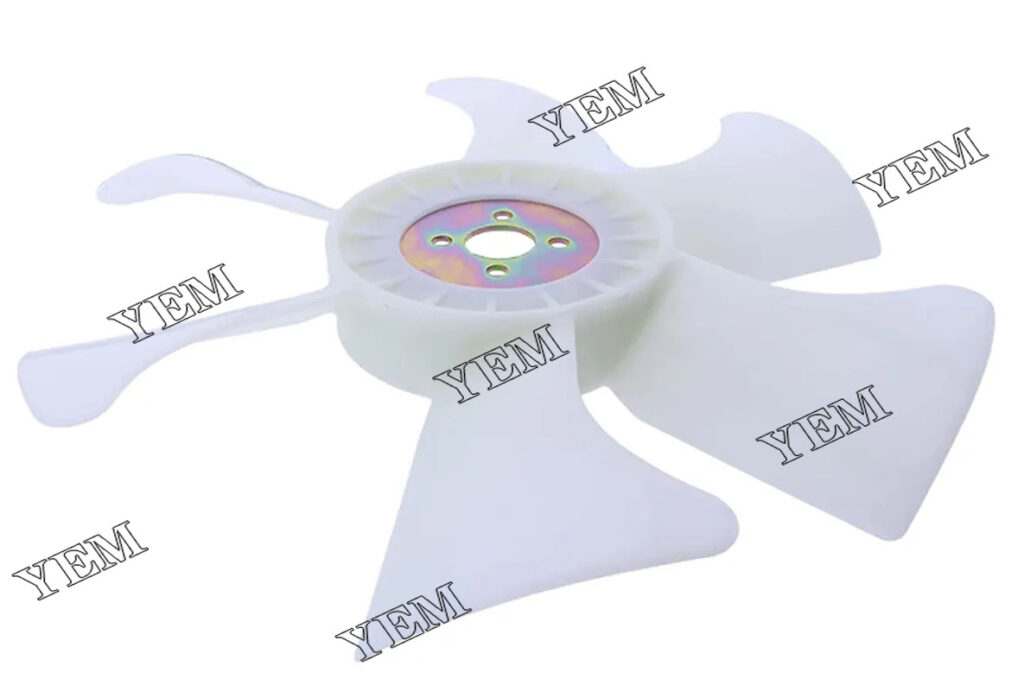
Optimized design of engine fan blades
The optimal design of engine fan blades involves many aspects, including blade geometry, material selection, number of blades, blade pitch, etc.
- Blade geometry: The optimal design needs to consider factors such as blade thickness, curvature, and twist angle. By reducing the thickness of the blades and increasing the curvature of the blades, fan noise can be reduced and efficiency can be increased. At the same time, adopting an appropriate twist angle can improve the aerodynamic characteristics of the blade so that it can maintain high efficiency under different working conditions.
- Material selection: Fan blades need to have high strength and rigidity, as well as good fatigue resistance and high temperature resistance. Commonly used blade materials include aluminum alloys, titanium alloys, and composite materials. Choosing appropriate materials can improve the durability and operating temperature range of the blades.
- Number of blades: The selection of the number of blades needs to consider the working conditions of the fan and the aerodynamic characteristics of the blades. Generally speaking, an appropriate number of blades can improve the efficiency of the fan, but too many blades will increase the resistance of the fan and affect the overall performance of the aircraft.
- Blade pitch: Proper blade pitch can reduce the noise and vibration of the fan. By rationally adjusting the pitch of the blades, the shock wave and flow interference can be reduced, and the working stability and efficiency of the fan can be improved.
In the optimal design of engine fan blades, it is necessary to comprehensively consider the influence of various factors, and conduct simulation analysis and experimental verification, and finally determine the appropriate parameters such as blade geometry, material selection, number of blades, and blade spacing to improve fan efficiency. and noise reduction goals.
Application cases of engine fan blades
The application cases of engine fan blades are as follows:
- Jet planes: Jet planes have fan blades in their engines that increase the flow of air and provide more thrust, allowing the plane to fly more efficiently.
- Ships: The engines of large ships also have fan blades, which can provide more power by increasing the flow of air, allowing the ship to move forward faster.
- Genset: Some large gensets also use fan blades, which can cool the genset by increasing air flow, improving its efficiency and stability.
- Industrial equipment: Some industrial equipment, such as compressors, coolers, etc., also use fan blades to increase air flow and improve the efficiency and performance of the equipment.
- Cars: Fan blades are also used in the cooling system of cars, which can reduce the temperature of the engine by increasing the air flow and keep the engine running normally.
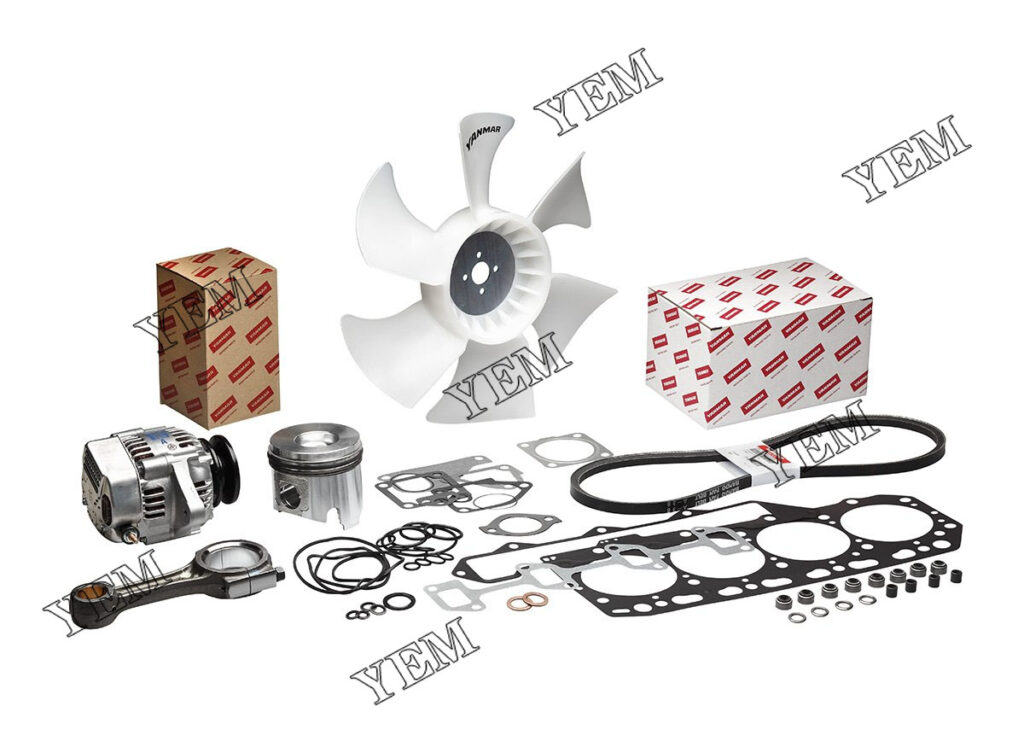
In general, the application cases of fan blades are very extensive, and they have played a role in increasing air flow and improving equipment performance in many fields.
Contact us
YEM Excavator Parts Co., Ltd. is a company specializing in the research, development, production and sales of excavator parts. We are committed to providing high-quality, high-performance excavator accessories solutions to global customers.
As a professional company, we have an experienced and skilled R&D team, capable of continuous research and innovation, and design and develop excavator accessories products that meet market demand. We pay attention to product quality control, adopt advanced production technology and equipment to ensure that each product can meet international standards and pass strict quality inspections.
Our product range covers all kinds of excavator accessories, including hydraulic cylinders, oil seals, filters, cabs, etc. These accessories have been carefully selected and designed to ensure compatibility with a wide range of excavators and to maintain outstanding performance and reliability in harsh operating environments.
We not only provide existing excavator accessories, but also customize design and production according to customer needs. Whether it is standard parts or non-standard parts, we can precisely manufacture and provide high-quality solutions according to the requirements provided by customers.
Our company not only pays attention to product quality, but also attaches great importance to customer service. We have a professional customer service team that can answer customer inquiries and solve customer problems in a timely manner. We also provide installation, maintenance and after-sales service of accessories to ensure that customers can get all-round support and assistance.