The function, material, manufacturing process, design, fault maintenance and other issues of the head gasket
Definition and function of head gasket
Head gasket is a seal located between the engine cylinder head and cylinder block. Its main function is to ensure that the gas and liquid inside the engine flow under different conditions, and to prevent leakage between compressed gas, coolant and engine oil.
Head gaskets are usually made of metal composite materials, which are resistant to high temperature and high pressure. It is installed between the cylinder head and cylinder block, forming a sealed interface to prevent mixing between the combustion chamber and the cooling system.
The functions of the head gasket include:
- Sealed cylinders: Head gaskets ensure that each cylinder can maintain pressure, preventing compressed gas in the combustion chamber from leaking to adjacent cylinders or the external environment.
- Separation of coolant and oil: Head gaskets prevent mixing between coolant and oil. It ensures that the coolant only circulates in the cooling system, while the engine oil circulates in the lubrication system, avoiding mutual contamination between the two.
- Separate the combustion chamber and the cooling system: the head gasket ensures the separation between the combustion chamber and the cooling system, prevents compressed gas or explosive gas from entering the cooling system, and also prevents the coolant from entering the combustion chamber.
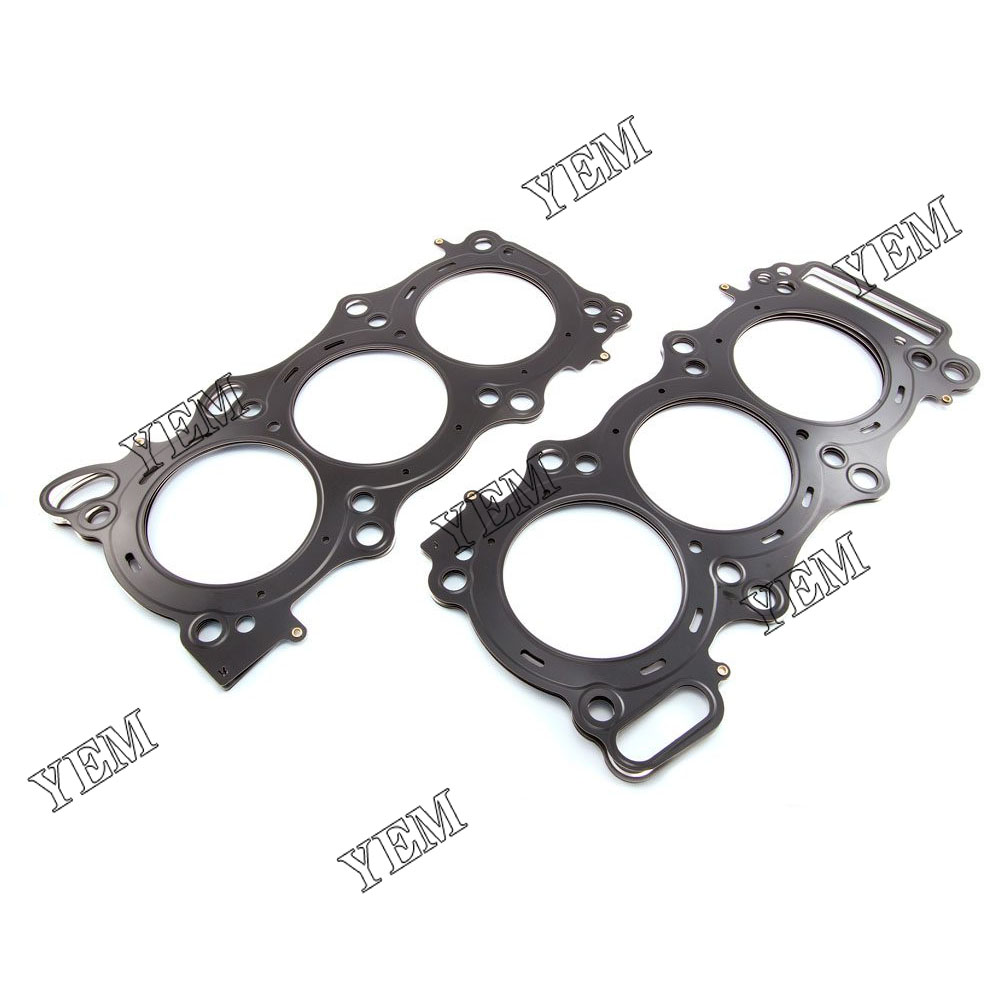
Overall, head gaskets play a critical sealing role in an engine, ensuring proper functioning between systems and preventing fluid and gas leakage.
Head gasket material and manufacturing process
The head gasket is a seal installed between the engine block and the cylinder head to prevent leakage between the combustion chamber, the coolant passage and the oil passage. The following are common materials and manufacturing processes for cylinder head gaskets:
- Materials:
- Composite metal gaskets: Composite metal gaskets are composed of multiple metal sheets, usually including stainless steel, copper, aluminum and other materials. These sheets are fixed together by pressing or welding to form a gasket with elastic and sealing properties.
- Cellulose paper gasket: Cellulose paper gasket is composed of cellulose paper or cellulose substrate and coated with high-temperature oil-resistant adhesive. This gasket has good sealing performance and reliability, and is relatively cheap.
- Manufacturing process:
- Pressing method: Composite metal gaskets are usually manufactured by pressing method. In this process, the metal sheets are stacked according to the design requirements, and then through the high and high pressure pressing process, the layers of sheets are tightly combined to form the overall structure of the gasket.
- Coating method: Cellulose paper gaskets are usually manufactured by coating method. In this process, the cellulose substrate is combined with an oil-resistant adhesive, and the mixture is evenly coated on the substrate by coating or dipping, and then dried and compressed to form a gasket with a certain thickness and elasticity.
It should be noted that different types of engines and application scenarios may require different cylinder head gasket materials and manufacturing processes. When selecting a cylinder head gasket, comprehensive consideration should be given to factors such as engine design requirements, operating conditions and budget, and suitable materials and manufacturing processes should be selected. Also, it is not important to check and maintain the engine regularly to ensure the proper functioning of the gaskets.
Head gasket design and construction
A car’s engine is made up of many important parts, one of the key parts is the cylinder head gasket (head gasket), which is located between the engine cylinder head and the cylinder block. The design and construction of the cylinder head gasket is critical to the proper operation of the engine.
The main function of the cylinder head piece is to seal the cylinder force, coolant and oil passages to ensure that they do not mix with each other or leak. The following are general design and structural features of cylinder head gaskets:
- Material: Cylinder head gaskets are usually made of metal composite materials, such as bent sheet metal and rubber coating. This material is resistant to high temperature, pressure and chemical attack.
- Sealing area: The cylinder head gasket forms a sealing area between the cylinder head and the cylinder block to prevent the high-pressure gas of the combustion chamber from leaking into the cooling passage or the oil passage.
- Channels and holes: There are many channels and holes in the cylinder head gasket to guide the flow of coolant and oil through various parts of the engine. These channels and holes need to butt up properly to ensure proper circulation of coolant and oil.
- Reinforced areas: Some critical areas of the cylinder head gasket may be designed to be reinforced to withstand stresses in high and high temperature conditions. These areas are usually thickened or reinforced.
- Leak-proof design: In order to prevent the leakage of coolant and engine oil, the cylinder head gasket usually has special designs such as sealing lips, protrusions and grooves. These designs can provide better sealing performance.
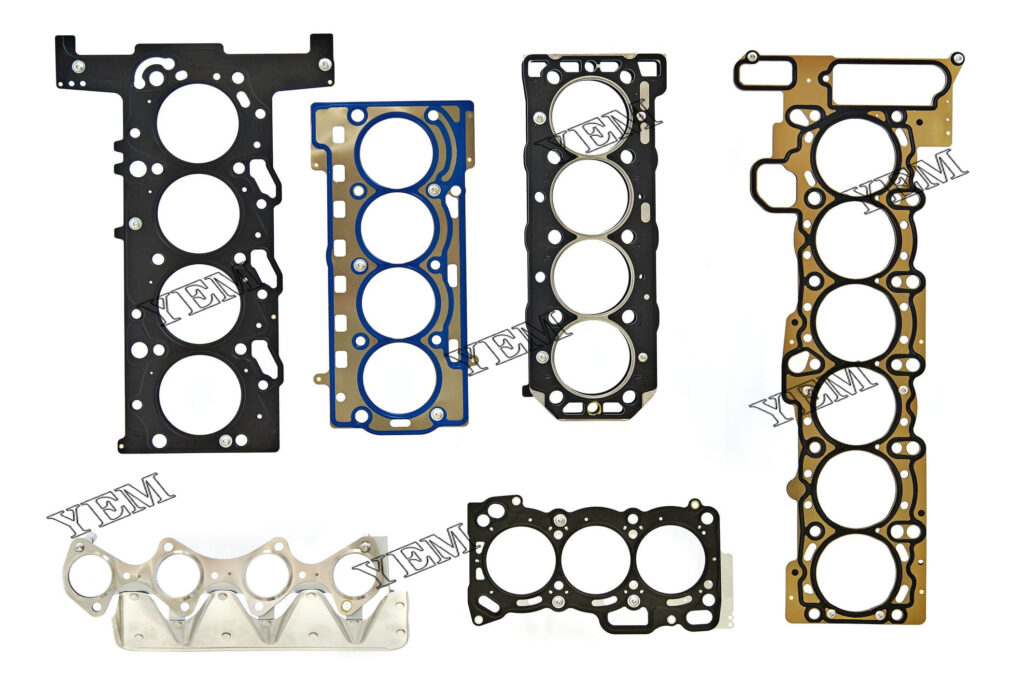
In general, the design and structure of the cylinder head piece is in the realization of reliable sealing performance, good durability and ability to adapt to various working conditions. Different types of engines and car manufacturers may have slightly different designs and construction details, but the above characteristics are generally applicable.
Head gasket grinding and machining technology
The head gasket of an automobile engine is a key sealing element connecting the cylinder head and the cylinder block. When the engine is running, it is subjected to high temperature and high pressure environment, so it needs to have good sealing performance and durability.
Grinding and machining processes are one of the important steps in the manufacture and repair of engine cylinder head gaskets. The following is the general cutting and processing process:
- Inspection: First, conduct a comprehensive inspection of the cylinder head gasket, including checking for damage, cracks or deformation. If severe damage is present, the gasket may need to be replaced with a new one.
- Cleaning: Clean the cylinder head gasket to ensure that there is no oil, chips or other impurities on the surface. Cleaning can be done with a suitable solvent and a brush.
- Grinding: If the surface of the cylinder head gasket is uneven or pitted, grinding is required to restore the flatness. Grinding can be done using special grinding tools and abrasives to ensure a smooth and even surface.
- Machining In some cases, it may be necessary to machine the cylinder head gasket to suit specific engine requirements. For example, gaskets may need to be cut or trimmed to shape and size to ensure a good fit with the cylinder head and cylinder block.
- Coating: Before the cylinder head gasket is installed, a layer of sealant is usually applied to its surface. This helps provide additional sealing energy and prevents leakage of lubricating oil, coolant or combustion gases.
- INSTALLATION: Place the chipped and machined head gasket on the cylinder ensuring proper alignment and install as specified by the manufacturer. When tightening bolts, follow the specified torque values and proceed in order to ensure even pressure distribution.
Please note that exact milling and processing may vary by engine type and manufacturer. In actual operation, it is recommended to follow the relevant manufacturer’s guide or consult industry technicians for accurate steps and requirements.
Head gasket failure and maintenance
The head gasket (Head gasket) is a key component in the engine, located between the cylinder head and the cylinder block. Its main function is to seal the cylinder pressure to ensure that coolant, oil and combustion gases do not mix with each other.
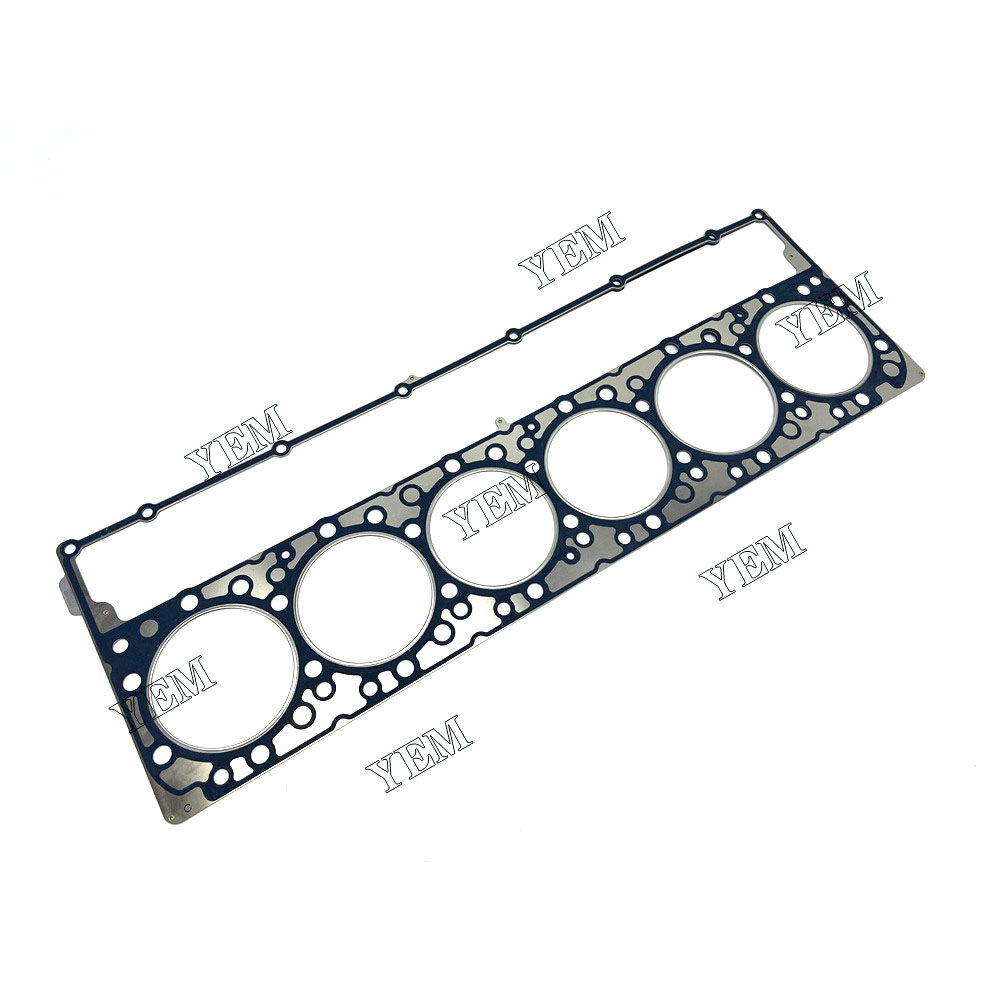
Faulty head gaskets can cause the following problems:
- Coolant and oil mixing: If the head gasket is cracked or damaged, the coolant and oil may mix with each other. This often results in cloudy coolant, thinner oil, and can cause engine overheating, white smoke, and more.
- Compression leaks: Cracked head gaskets can also cause cylinder compression leaks. This reduces the compression efficiency of the engine, causing problems such as loss of power, loss of cylinder pressure, etc.
The maintenance and care of the head gasket is not important, here are some suggestions:
- Regularly check the coolant and engine oil. Regularly check the color and quality of the coolant and engine oil. If the two are found to be mixed or abnormal, it may be a sign of head gasket failure.
- Pay attention to engine temperature: If the engine temperature rises abnormally, it may be one of the manifestations of head gasket failure. Timely inspection and repair is necessary.
- Avoid excessive acceleration and overheating: Excessive acceleration and heat may increase the load on the engine and put additional pressure on the head gasket. The life of your head gasket can be extended by following a proper driving and cooling system maintenance schedule.
- Replace degraded parts in time: Other aging or damaged parts in the engine may also affect the head gasket. Regular inspection and replacement of these parts can reduce the risk of head gasket failure.
If head gasket damage is suspected, it is recommended to contact a professional auto mechanic for inspection and repair as soon as possible. They can use methods such as compression testing, coolant and oil analysis to confirm the problem and take appropriate steps to fix it.
Head gasket improvements and performance optimizations
Improving and optimizing the head gasket of an automotive engine is a common practice to improve performance and reliability. Here are some possible modifications and optimizations:
- Material selection: Use higher quality materials to manufacture head gaskets, such as multi-layer metal () gaskets. This gasket consists of multiple metal layers for better sealing and durability.
- Thickness adjustment: By adjusting the thickness of the head gasket, the compression ratio of the engine can be changed. Thinner shims increase compression ratio, improving combustion efficiency and power output.
- Improved sealing: ensure that the head gasket can provide good sealing during installation to prevent leakage between coolant and engine oil. Using a high-quality sealant or coating can improve the seal.
- Cooling system optimization: Improving the cooling system of the engine can reduce the temperature of the engine, reduce the thermal stress on the head gasket, and prolong its life. This can be achieved by increasing the radiator capacity, improving the water pump design, or using high-efficiency coolant.
- Strengthened structure: In high performance applications, it may be necessary to strengthen the structure of the head gasket to withstand higher pressure and thermal stress. This can be achieved by adding metal or using reinforcements.
- Combustion chamber design: The combustion chamber design of the optimized engine can improve the combustion efficiency and reduce the load on the head gasket. For example, no partition design, optimized cylinder wall shape, etc.
- Regular maintenance: Regular inspection and replacement of head gaskets is an important step to maintain engine performance and reliability. Follow the manufacturer’s recommendations for maintenance and address any leaks promptly.
Note that tool modifications and optimization methods may vary by engine type, vehicle make and application. It is recommended to consult a professional automotive engineer or an experienced mechanic for the best advice for your specific vehicle needs.
Head gasket and emission control
The head gasket is a key component in the engine, located between the cylinder head and the cylinder block. Its main function is to seal the cylinder pressure, ensure that the coolant and oil do not mix, and prevent cylinder pressure leakage.
Emission control refers to the treatment of the exhaust gas generated by the engine to reduce the emission of harmful substances into the atmosphere. Emission control systems typically include multiple components such as catalytic converters, oxygen sensors, exhaust gas recirculation systems, and more. The goal of these components is to reduce the content of harmful substances such as hydrocarbons, nitrogen oxides and particulate matter in the exhaust gas to meet the requirements of environmental protection regulations.
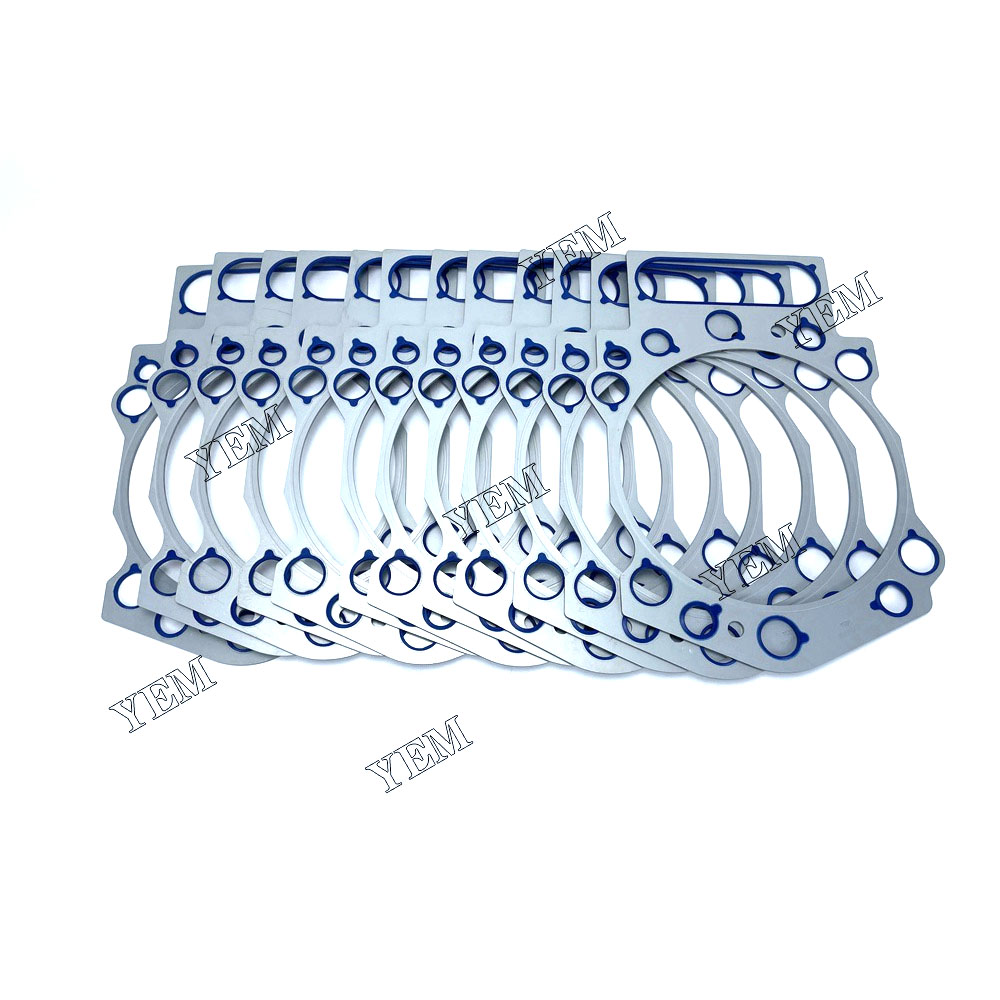
There is no direct correlation between head gaskets and emission control. The head gasket mainly affects the sealing performance of the engine, while the emission control is a system for exhaust gas treatment. However, if the head gasket fails or is damaged, it may cause cylinder pressure leakage, affecting the combustion efficiency and emission performance of the engine. Therefore, a well-maintained head gasket is very important for proper engine operation and emission control.
Head gasket future development trend
Based on technology and industry trends, the following are some factors that may affect the future development of automotive engine cylinder head gaskets:
- Material innovation: With the advancement of materials science and engineering, the development of new shapes may improve the performance and durability of head gaskets. For example, the use of materials that are more resistant to high temperature and pressure can improve the sealing performance of the head gasket.
- Sealing improvement: Manufacturers may invest more R&D resources to improve the sealing technology of the head gasket to reduce the risk of leakage and failure. This may include improved design, enhanced sealing surface treatment and the adoption of more advanced sealing materials.
- Emergence of alternative technologies: With the rise of electric vehicles and other alternative powertrains, the demand for traditional internal combustion engines may decline. This may have an impact on the market demand for head gaskets, but there is still a need to maintain and repair existing head gaskets in conventional internal combustion engine vehicles.
- Automated manufacturing: As the manufacturing industry becomes more automated, the production process of head gaskets may become more efficient and precise. This could reduce manufacturing costs and improve product quality.
Contact us
Thank you for contacting our YEM team. We are committed to delivering outstanding service and support to our esteemed customers. If you have any queries or require assistance, please feel free to reach out to through the following contact options
We are available to assist you and eagerly await the opportunity to address any questions you may have.